FEEDBACK
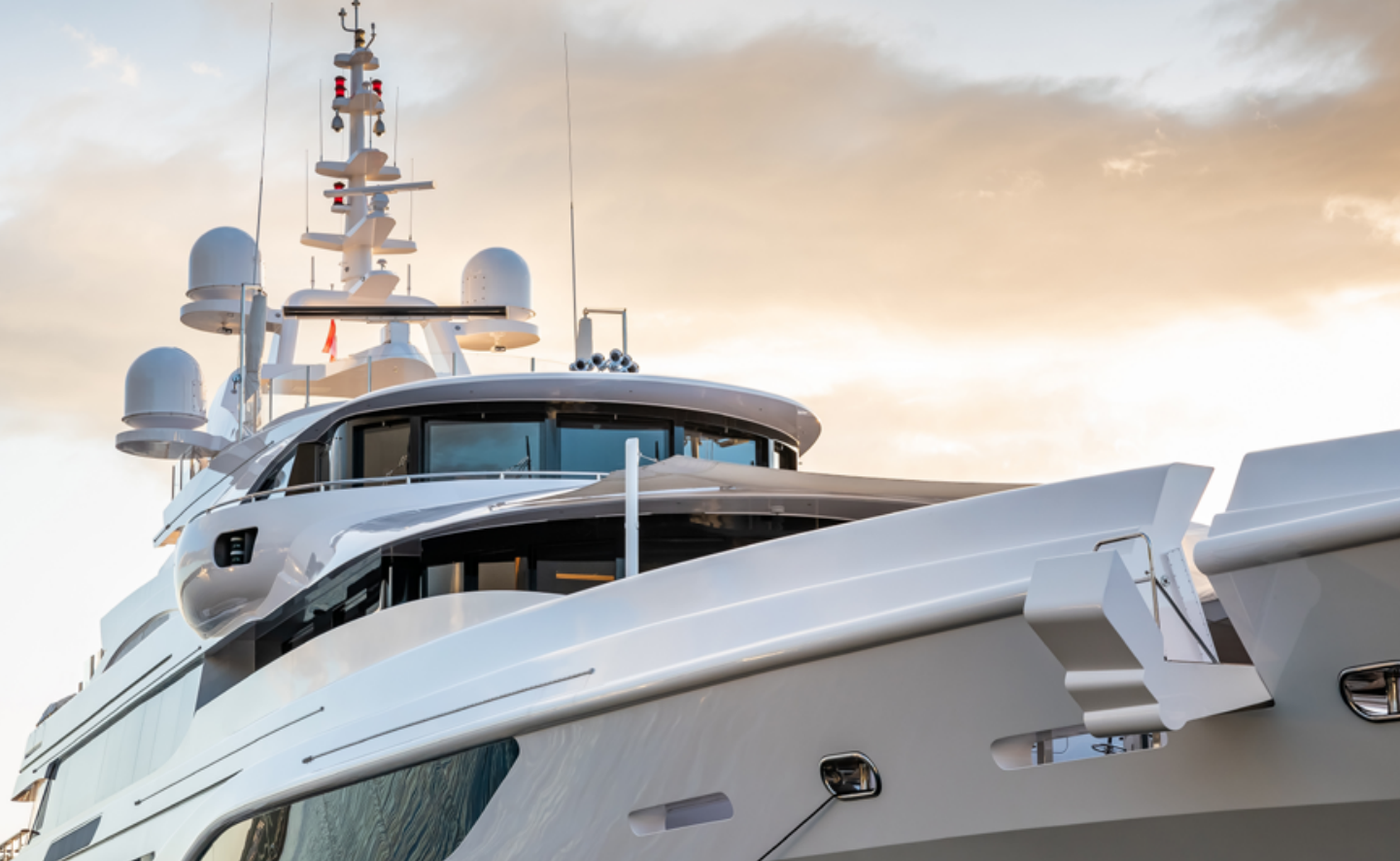
Questions of Integrity
The common theme throughout this edition is integrity!
We start with two cases where watertight integrity, or its absence, was the main contributing factor. Fortunately, in both cases the crews responded in a very professional manner and a major disaster was avoided.
Several cases involve what we might call design integrity â inadequate alarms, poorly-positioned heating lamps, and areas where explosive vapours can build up to name a few. We strongly believe in the benefit of having senior officers present during construction. Still, even if this is not possible, the first crew to join a new vessel can carry out a thorough risk assessment by inspecting every part of the yacht and asking themselves how everything will work in practice and what potential dangers might have been introduced as a result of the design.
Then there are issues around operational integrity â are there sufficient crew numbers, is the proper PPE provided, and is it used?
Finally, we consider system integrity. Naming the master as the DPA is wrong in principle, contravenes the requirements of the ISM Code, and is also obviously a bad idea!
There are some excellent reports in this edition and much food for thought. We thank all our reporters for bringing the issues to our attention so we may all learn the safety lessons they have raised.
Yours in Safety,
The CHIRP team
-
M2242
–
Near miss – breach of watertight integrityNear miss – breach of watertight integrityInitial Report
While underway during a busy trip, the lookout performed their deck rounds. They found the shell door fully open when they entered the tender bay, which is located on the lower deck, approximately 8â above the waterline. Water entered the tender bay due to the vesselâs movement and swell.
This caused the loss of some equipment but, fortunately, the vesselâs stability was not severely affected. The issue
was quickly reported, and the door was secured safely.
Upon investigation, it was found that there was severe salt build-up inside the controls of the door, which had caused a âshortâ of the âopen doorâ button. This caused the door to operate and open without any human control.
The bridge has indicators for the door status, but they are inconspicuous and inaudible. There is also an isolation
switch, but the Standard Operating Procedure (SOP) did not include using it at sea.
Subsequently, the company installed a Deadman switch into the door system to eliminate the single point of failure,
updated the SOPs, informed the fleet (especially the sister ships), and reviewed the risk assessments for similar issues
elsewhere on the vessel.CHIRP Comment
This incident highlights a critical flaw in the design of the vesselâs tender bay doors, requiring immediate action to
prevent potential accidents. CHIRP commends the crew members for their vigilance in detecting and averting a
severe malfunction and notes that good old-fashioned safety rounds brought this to the masterâs attention before
the amount of water being taken on board seriously affected the superyacht’s stability.
The vesselâs alarm systems and reliance on a single point of failure raise concerns about the thoroughness of
consultation concerning the ergonomics of alarms and controls during construction. Alarms placed in inconspicuous
places that cannot be seen and are inaudible due to normal background sounds are useless.
Managementâs proactive steps to eliminate this single point of failure and update safety procedures in the Safety
Management System (SMS) are commendable. However, CHIRP also recommends prioritising enhancements to the
weatherproofing and sealing mechanisms of the tender bay doors, alongside measures to combat corrosion.
Maintaining watertight integrity in vessel design and operation is paramount, and CHIRP feels that implementing
these measures and enhanced crew maintenance training is necessary. This incident highlights the importance of
addressing vulnerabilities in vessel design, particularly concerning environmental factors and technical failures.Key Issues relating to this report
Design â There was a latent defect that meant the equipment was not fit for purpose either on the bridge for alerting or on the tender deck against exposure to the weather. Do critical controls for your vesselâs opening and closing appliances rely on a single point of failure? Have you checked?
Alerting â How well do your alarms alert you to a problem? Can you recognise the alarm from its sound or light function? Are you shown these alarms as part of your familiarisation?
Situational Awareness â During your motor yachtâs operational service, ask questions to identify potential single
points of failure for operational and personal safety.This data type is not supported! Please contact the author for help.
-
M2243
–
Explosion in the Engine RoomExplosion in the Engine RoomInitial Report
The incident occurred on a relatively small motor yacht (70ft) with just three crew members. After approximately six hours at anchor, the guests decided to head back to the marina. After stowing all the water sports equipment onboard and securing the aft platform, the master engaged the main engines.
With contacts on, the starboard engine exploded in the engine room, located aft, under the area where the guests were. By checking the CCTV, the master could see only misty air. None of the alarms were activated.
The master switched the contacts off, and the ventilation system was cut off automatically. The master went down and didnât know what to expect, as no alarms were raised. After looking through the viewing port, the door to the engine room was opened to ensure there was no fire, but the engine room was full of contaminated air. The door was closed immediately.
The guests were notified that a tow was requested to return the vessel to the marina.CHIRP Comment
A starting battery explosion is a regular occurrence on some superyachts, where the necessary knowledge of battery maintenance is lacking.
From a technical perspective, CHIRP highlights that the maintenance of the starting batteries requires a good knowledge of them to ensure that they are safe to operate
and adequately charged. Venting hydrogen during any charging operation is vital to provide a safe atmosphere. There was a lack of knowledge or a lack of knowledgeable
crew to check that the batteries were in good condition and safe to use.From a crew resource perspective, a risk assessment based on assessing the hazards and threats to the vessel should be carried out to determine the number of crew members to employ to cover maintenance and emergencies safely.
There appears to be no minimum manning level for a yacht of 21 meters, and it is based on the ownerâs financial willingness to employ the minimum number of crew for the service being provided rather than being able to respond to an emergency.
CHIRP advocates that Flag States should have a say on the minimum manning level based on the risks of the vesselâs operations and the number of guests being carried.Key Issues relating to this report
Capability â The vessel did not have adequate inspection and maintenance schedules to ensure the batteries were safe. Does your motor yacht have a maintenance schedule
for items of critical importance?
Culture â Organisational culture needs to change, and safety should be managed using a risk-based approach. How many crew members does your vessel carry compared to a similar-sized vessel?
Teamwork â With only three crew members, including the master, the feeling of teamwork can be challenging to achieve. -
M2240
–
Damage to a tender under towDamage to a tender under towInitial Report
Upon approaching an anchorage with a 38ft tender in tow, the crew noticed the tender sitting low in the water and assumed it was sinking. The master was notified by radio,
and the chief officer ran to the aft to assess. The chief officer noticed that the speed reduction (when approaching the anchorage) was causing the tender to sink, so he requested that the captain increase speed again and not enter the anchorage.
Another yachtâs tender noticed the problem and came over to offer assistance. Two crew members were transferred to the other yachtâs tender, taking fenders and a pump.
As the crew approached the towed tender, it was apparent that the side boarding door was slightly ajar. A crew member was transferred to the towed tender and was able to shut the door. With the boatâs movement through the water, the tender soon emptied via the aft scuppers and freeing ports. The tender was saved, although the engines were flooded.CHIRP Comment
The crew on the towing vessel and the response team are to be praised for their good actions, especially the officerâs quick thinking and seamanship skills, preventing a more
serious situation. As demonstrated in this case, proper training and expertise onboard are crucial for handling unforeseen incidents effectively.The failure to secure the tender for towing during pre-departure checks and procedures underscores the importance of thorough preparation and adherence to good seamanship. Implementing a checklist that cross-checks the towed vesselâs watertight integrity could prevent similar incidents in the future. Additionally, considering weather conditions and setting appropriate limits for towing operations are other essential safety measures which must be considered.
CHIRP recommends rigging a camera on the tender for visual monitoring during towing. This would enhance safety and situational awareness, allowing for timely adjustments to course and speed and interventions if necessary.Key Issues relating to this report
Capability â The crew checking the tender before towing paid insufficient attention to its watertight integrity. The flooding of the engine compartment shows the consequences of this omission, which could have been much worse. Do you have a checklist for your towing operations?
Situational Awareness â When towing, consider the bigger picture and conduct a risk assessment to ensure all hazards are considered. Is towing a tender part of your SMS? -
M2167
–
Galley FireGalley FireInitial Report
As a chef was leaving the galley area, having closed it down after the meal, they noticed smoke seeping from a door in a smaller, less frequently used section of the galley. Concerned, the chef investigated and found that several pizza boxes had caught fire. These had been stored under heating lamps, which, unknown to anyone, had been inadvertently switched on during the cleaning process. Acting promptly, the chef immediately reported the fire to the bridge using the radio communication system, then turned off the heating lamps and retreated to a safe distance near the doorway.
Responding swiftly, the duty deckhand arrived at the scene without delay. Their initial attempt to suppress the fire using the high fog system was met with challenges due to the fireâs growing intensity. Meanwhile, another chef joined the effort, moving the burning pizza boxes away from other items to contain the fireâs spread. With the escalating situation, the duty deckhand used a foam extinguisher to effectively put out the flames on the pizza boxes and the area surrounding the heating lamps.
Additional crewmembers quickly arrived and took decisive emergency measures, shutting down all electrical systems and ventilation in the galley to prevent the heat from the fire from spreading. Simultaneously, nearby doors were promptly closed to curtail the spread of smoke to other parts of the ship.
The shipâs engineers discussed the manual operation of the ventilation system from the engine control room (ECR), aiming to extract the lingering smoke from the galley area efficiently.
From the moment the fire was reported to the bridge, the containment and control of the fire took approximately six minutes.
CHIRP Comment
CHIRP praises the crew and the management for having a well-trained crew which handled a potentially dangerous situation swiftly. However, there are a couple of points worth highlighting. The bridge was notified by radio and responded to the incident. Anyone discovering a fire should always raise a loud vocal alarm (eg shouting âFire, Fire, Fireâ), and the fire alarm, if fitted, should always be sounded. Both of these alert everyone in the vicinity that there is a fire so that they can assist in tackling it. The ventilation should be stopped if not done automatically. The use of high-fog as an extinguishing medium was ineffective and, in this case, raises the question of whether it is the right application for a fire that has taken hold.
Heat energy transference from an energy light source can be extremely high, and direct contact is not necessary to start a fire. Materials such as cardboard and plastic coverings will quickly smoulder or melt, even in close contact with normal shipboard lighting sources. A minimum distance warning sign should be positioned near any heat lamp so that flammable material cannot be heated to combustion, or a suitable guard should be placed around the lamp to provide a physical barrier that meets the minimum safe distance if applicable.
Light switches should be properly labelled and positioned in sensible locations close to the storerooms they serve. They should also be clearly labelled. If in doubt, ask the electrical officer to check the function of the switch in question.
Storage of any material should always be considered from the point of view of fire risk and how to control that risk. Eliminating the hazard is the best way to reduce risk. If, after the debrief for this incident, the heating lamps are found to serve no operational function, consideration should be given to isolating the circuit. Hence, they become non-operational and labelled as such.
The incident underscores the importance of crew membersâ vigilance and highlights effective teamwork and everyoneâs critical role in ensuring the shipâs and its occupantsâ safety and security. Different crew membersâ collaborative and swift actions – from the chefâs initial discovery to the coordinated response efforts – ultimately contained and extinguished the fire.
The ISM Code Section 8, Emergency Preparedness, mandates regular exercises and drills for emergencies. This concise response highlights its value, and whilst there were areas for improvement, the crew contained and extinguished the fire. It is a valuable lesson for maritime safety and emphasises the importance of continuous training and preparedness.
Key Issues relating to this report
Situational awareness â The crewâs response to the emergency was swift and appropriate. There needed to be more awareness of the switchâs function (controlling the heat lamp) by the crew. It was very likely that the heat lamps had been switched on before with no consequence. However, this time, pizza boxes were stored near the lamps and combusted due to radiated heat from the lamps.
Communication â This switching arrangement was likely similar in other ships of the same class. Communicating the possible hazards to other ships of the same type by labelling the switch and providing safeguards for preventing contact with flammable materials is required. How does your company communicate design hazards?
Design â Better design at the new building stages, providing built-in safeguards for heat contact and switches in the same room, as the lamps would help prevent accidental use.
This data type is not supported! Please contact the author for help.
-
M2236
–
Working at height without any PPEWorking at height without any PPEInitial Report
Our reporter sent a photograph of a crewmember working at height outboard of the vessel, engaged in window cleaning. They were not wearing any fall arrest equipment, and if they had slipped, they would have fallen approximately 10m to the concrete quayside below and been seriously injured or killed.
They were contacted by a nearby crew on another yacht to wear protection, but they refused to take any action.CHIRP Comment
CHIRP has raised concerns about the incident with the appropriate Flag State for the vessel and received a very positive response. An investigation was carried out, and the
DPA investigated the incident.
CHIRP was notified that equipment was available and that training had been provided to all the crew. However, safety gear was not worn, and no permit to work or operational supervision was evident. The crew member in question was dismissed from the vessel because of not adhering to the requirements. There is never any comfort in learning that a crew member was dismissed from the vessel, as it usually implies a failure in the management system on board.
The investigation revealed that the DPA was, in fact, the Master of the vessel, which is entirely wrong in terms of defining the DPAâs role according to the ISM Code.
The DPA serves as a crucial link between the ship and shore management. Their primary responsibilities include ensuring that the safety management system is implemented and maintained effectively, providing support and guidance to the shipâs management, conducting audits and reviews of the system, and serving as the liaison with external parties, including flag states and classification societies.
In this case, the revelation that the DPA was also serving as the vesselâs Master represents a conflict of interest and a violation of the ISM Code. The DPAâs role is to be independent of operational duties aboard the vessel to maintain impartiality and oversight.Key Issues relating to this report
Not actual event. For illustration only Culture â This incident highlights a poor safety culture where senior management does not drive safety. There was a lack of operational supervision. The work being undertaken by the crew falls under the category of working at height and necessitates a Permit to Work.
Alerting â When third parties warn you about how unsafely you are operating and nobody from your vessel raises any concern, there is something clearly wrong with your shipboard safety management.
Complacency â No matter how many times you have carried out such an unsafe act, at some time, you will not be so fortunate and will slip and fall.
Local Practices â Follow local good practices. You are ultimately responsible for your safety. Do you know your DPA and their contact details for your vessel? Is the DPA of your vessel the master? -
M2244
–
Lack of crew in an emergencyLack of crew in an emergencyInitial Report
A private motor yacht of approximately 40m LOA experienced steering loss due to a loss of pressure on the hydraulic system. The hydraulic system solenoid had broken, and there was no spare solenoid onboard or competent engineer to repair the existing solenoid. The failure resulted in the loss of function for the steering, anchor winch, and hydraulic transom door hatch, all operated by the same hydraulic pack. Due to stormy weather conditions, the vessel nearly ran aground before it reached the nearest safe haven.
Only three crew members were on board, and the owner of this private boat refused the masterâs request to employ additional crew for a vessel of this size, which, according to industry practice, should be approximately seven people. As a result, the three crew members (captain, motorman, and stewardess) ended up in a near-miss situation, which could have been much worse. Fortunately, using good seamanship, they brought the vessel into the marina using only engines and the emergency steering system.
CHIRP Comment
Itâs concerning to hear about the unsafe situation onboard the vessel due to the design and redundancy issues with critical equipment. Relying on one hydraulic power pack for multiple critical functions such as steering, transom door hatch, and anchor winch creates significant risk, especially concerning equipment redundancy, crew size and knowledge.
The crewâs skilful averting of a grounding and safe return home demonstrate their competence and good seamanship. However, the inability to repair the solenoid due to the lack of technical knowledge and spare parts highlights a severe deficiency of preparedness.
The recommendation from CHIRP to conduct a thorough risk assessment to determine the appropriate manning levels for a vessel of this size is crucial. Adequate staffing is essential for ensuring the safety and effectiveness of operations, particularly in emergencies.
While the 3-person crewâs good fortune and decision-making may have helped avert a grounding this time, this is
not a reliable resource level for future voyages. The owners should take proactive steps to address the underlying
issues and implement necessary changes to prevent similar incidents in the future. This includes investing in equipment redundancy, carrying essential spare parts onboard, and providing sufficient crew training. Failure to do so could lead to potentially catastrophic consequences for the vessel and its crew.Key Issues relating to this report
Design â Large superyachts should always have redundant critical spare parts to repair or replace essential equipment. This should be part of the vesselâs design and requested by the flag and insurers.
Capability â Ensure the motor yacht crew has the right skills and knowledge to handle an emergency. The current crew level, with their combined knowledge, which managed the emergency, was not a safe number.
Culture/Complacency â Just getting by is not good enough. Safety management must be a proactive approach to assessing potential risks. Just because nothing has happened before is no reason not to take all precautions. Prudent overreaction is always the safest way and should be part of the companyâs vision for the crew and passengers.