FEEDBACK
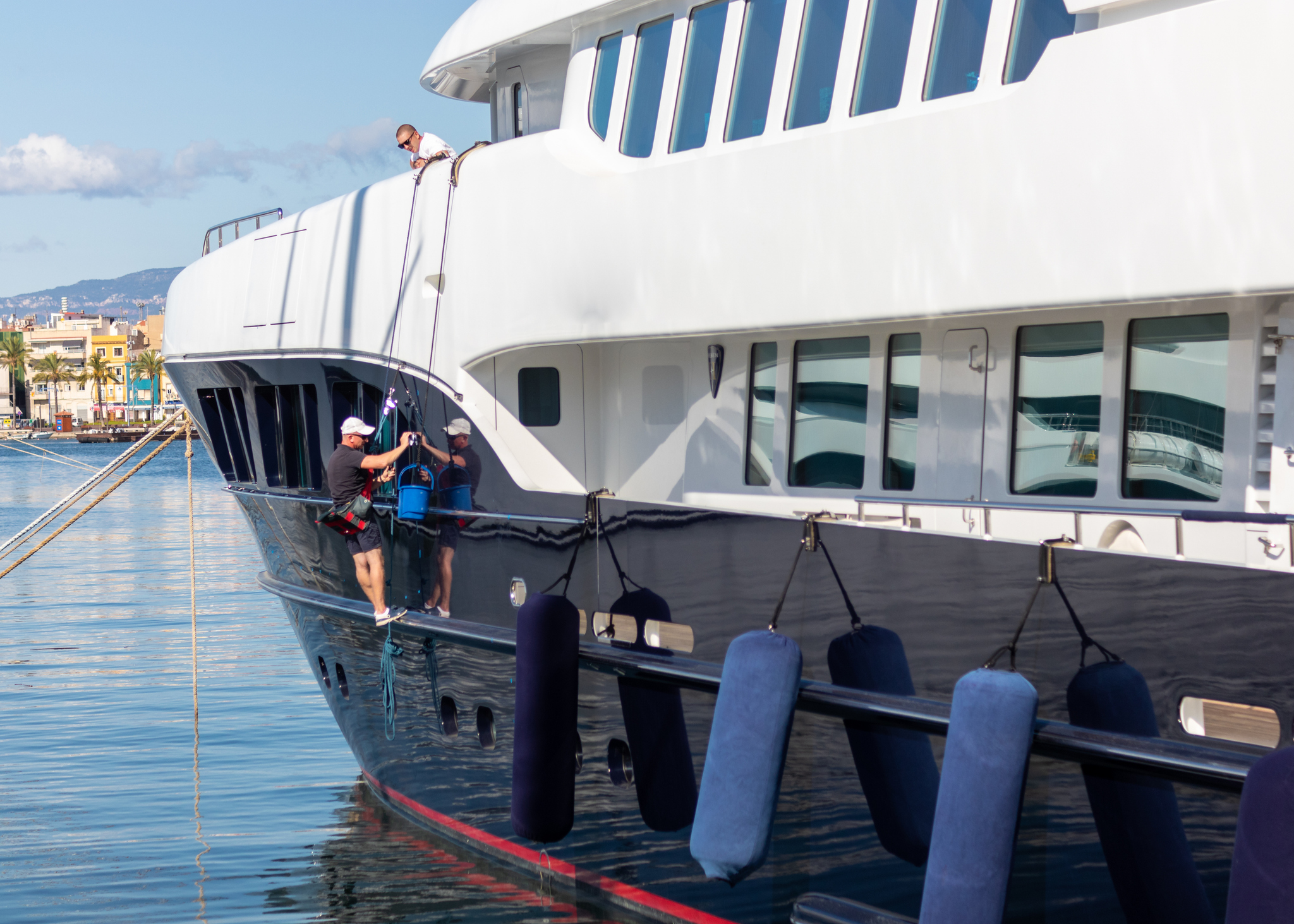
Say what you do; Do what you say!
The essence of the ISM Code is that companies should develop procedures that describe the actions their personnel are required to follow, and then ensure that these procedures are followed. Such thinking is critical in the superyacht industry, which is increasingly in the spotlight. Recent accidents involving well-known individuals have contributed to increased scrutiny of the sector.
Although the majority of superyachts are well-run and have competent crews, but from the reports below, we can see that some still have a lot of work to do. We learn of vessels where proper safety gear was lacking, where recovering an anchor required a crew member to thrust a screwdriver into an electrical circuit board, where crew members were working aloft without proper harnesses, where unsafe pilot boarding arrangements were considered appropriate to avoid scratching the paintwork, where the requirements of MLC and SOLAS were ignored by an owner/operator, and where mooring and chemical safety were overlooked.
This is extremely disappointing.
On a more positive note, we were pleased to assist the six flag states that register the most superyachts in creating a safety flyer on working aloft, which is included with this edition of Superyacht FEEDBACK. The flyer offers sensible guidance that should be followed at all times, and we recommend it to you. As mentioned earlier, scrutiny is increasing, so we anticipate breaches of the guidance will be dealt with severely in the future.
Until next time, be careful out there and do your best to avoid becoming a statistic.
-
M2487
–
Safety Concerns DismissedSafety Concerns DismissedInitial Report
Our reporter said “I am submitting this report anonymously because I fear retaliation. Previous safety concerns raised onboard have either been ignored or dismissed, leaving me no other option.
Several serious safety issues are currently evident on the vessel. Firstly, the crew is being issued wakeboard helmets instead of certified safety helmets for working at height. These helmets are not designed for industrial use, do not provide adequate protection against falling objects or impacts, and often do not fit properly. Informal concerns have been raised about this, but no action has been taken to supply the correct personal protective equipment.
Anchor operations are being conducted under unsafe conditions. To retrieve the port anchor, the crew must force a screwdriver into the circuit board to activate the system. This hazardous and makeshift method presents a significant risk of electrical injury and potential damage to the equipment.
These are not isolated issues. They are part of a broader safety culture problem on board. There is a noticeable disregard for proper safety standards, and crew members are actively discouraged from speaking up. This can create an environment where hazardous practices become normalised, and there is little evidence of proactive safety management. I hope this report will lead to meaningful action to address these risks before someone gets hurt.”
CHIRP Comment
Working on a vessel where safety is taken seriously, and leadership is supportive makes a real difference to morale and performance. When crew members feel trusted, respected, and empowered, they are more likely to speak up, take responsibility, and work with purpose. Sadly, our reporter did not experience this.
In this case, the vessel’s on-board management reflected wider failings within the company. The crew reported feeling unsupported and unsafe. According to the report, there was little evidence of an active safety culture, and serious concerns were raised about working conditions. When safety is not prioritised, trust breaks down – and so does performance. Company leadership at all levels must recognise their role in creating a safe and positive working environment.
CHIRP encourages companies to listen to feedback, act on concerns, and support leadership behaviours that build trust and safety from the top down. Seafarers should never feel that reporting safety concerns is a last resort.
CHIRP raised the issues outlined in the report with the Flag State, which responded constructively with a plan of action. The Flag State has asked that such concerns be reported to them directly in future. However, CHIRP is mindful that not all seafarers feel confident that their identity will be protected. We remain committed to offering a trusted and confidential reporting route for those who may feel unable to raise concerns elsewhere.
Key Issues relating to this report
Culture – The dominant issue. The crew described a poor safety culture, a lack of trust, and fear of raising concerns. A culture that discourages speaking up erodes morale and increases risk.
Communication – Failures in information flow, both within the vessel and between the ship and shore, were evident. Poor communication leads to misunderstanding, confusion, and missed hazards.
Teamwork – The lack of supportive leadership undermines teamwork. A crew that does not feel united or supported is less effective and less safe.
Fatigue – While not explicitly stated, the poor working conditions likely contributed to fatigue or a high workload. Fatigue reduces alertness, reaction time, and judgment.
Alerting – the reluctance to contact the Flag State directly and the need to use CHIRP indicates a failure of systems that should enable safe, anonymous reporting. Seafarers felt they had no safe route to raise concerns internally or externally.
Key Takeaways
 Seafarers – Speak up, even when it is difficult. Your voice matters. If you are working in unsafe or unsupportive conditions, reporting through trusted channels like CHIRP can help drive change. A strong safety culture begins with individuals who care enough to raise concerns, even when the system appears not to listen.
Managers – Culture is built, or broken, by leadership. Poor on-board culture and weak leadership directly harm safety, trust, and performance. Create conditions where the crew feel respected, heard, and supported. Empower teams to report concerns without fear. Safety is not just compliance — it is behaviour, values, and consistency.
Regulators – Confidential reporting needs absolute protection. Seafarers will not report concerns if they fear being exposed. Confidentiality and follow-up action are critical. Regulators must ensure that reporting systems are genuinely safe and trusted and that companies are held accountable when systemic issues are raised.
-
M2488
–
Working aloft without proper fall protectionWorking aloft without proper fall protectionInitial Report
The reporter saw three people working aloft on a neighbouring superyacht. One wore a full harness, one appeared to be wearing a waist belt, and one had no fall protection at all.
CHIRP Comment
CHIRP thanked the reporter and informed them that CHIRP had contacted the Flag State concerning this incident.
 There are several issues with the reporter’s observations regarding this report. Firstly, one of the crew was wearing a harness; why were the other two crew members not wearing the same harness for the same work activity? Was this because there were insufficient harnesses on board? Or did one crew member decide it was safe for them and not insist that the others needed protection?
The reporter saw that one of the crew members was wearing a waist belt, which is not clear in the photograph. Nevertheless, waist belt-type harnesses should not be worn as fall protection due to their lack of support during a fall, which would most likely result in permanent back injury—they are not designed for fall protection.
CHIRP would like to add that, following collaboration with the six leading Flag States which register the most superyachts, an inaugural safety flyer on working aloft has been produced. The flyer can be seen on the back page of this feedback edition. CHIRP would like to thank the Cayman Islands Registry for making the first one, along with other leading flag states and CHIRP Maritime.
Key Issues relating to this report
Culture – Inconsistent use of safety harnesses suggests either a weak safety culture or poor enforcement of safety procedures. If some crew members do not feel obliged or expected to follow basic safety practices, the culture is not functioning correctly.
Capability – The use of an inappropriate waist belt instead of proper fall protection indicates a lack of knowledge or training about the appropriate equipment for working aloft. Correct practices would be better highlighted if a Permit to Work were used.
Teamwork – If one crew member is correctly equipped but does not intervene when others are not, it suggests a lack of shared responsibility and poor team cohesion. Good teams look out for each other.
Fit for Duty – Safety covers not only the physical but also the psychological aspects.
Key Takeaways
Seafarers – If one person needs a harness, all do. Inconsistent use of safety gear puts everyone at risk. If a task requires fall protection, ensure that every crew member is adequately equipped. Don’t assume someone else’s risk is different from yours — safety must be a standard, not an option.
Managers – Supply the gear and set the standard. Ensure there are enough adequately certified fall protection systems on board, and make it clear that unsafe alternatives, such as waist belts, are not acceptable. A transparent, enforced safety standard prevents improvisation and protects your crew.
Regulators – Support safety with visibility and clarity. CHIRP welcomes collaboration with Flag States to raise awareness and promote consistent safety standards. Sharing best practices through initiatives like the ‘Working Aloft Safety Flyer’ helps turn guidance into action on board.
-
M2392
–
Look After Your Pilot – They’re Looking After You!Look After Your Pilot – They’re Looking After You!Initial Report
CHIRP received a report from a pilot concerning a non-compliant boarding arrangement and an apparent lack of care from the vessel’s crew.
The pilot ladder was suspended from the deckhead and failed to rest flush against the ship’s side due to hull belting—a setup that did not meet safe boarding standards. Although a small shell door was available for safer access, large fenders had been rigged on either side. When the pilot requested that these be removed to facilitate safe boarding, the master refused, citing concerns about damage to the paintwork.
The pilot assessed the situation and stated that boarding would not proceed unless the obstructions were cleared. Eventually, the fenders were removed, and boarding took place via the shell door.
The event was filmed from the bridge wing and by crew members, which contributed to the pressure and unease felt by the pilot. During boarding, the duty pilot struck his head, sustaining a minor injury (see attached image). The crew did not inquire about the pilot’s welfare or offer first aid. Instead, he was handed a pair of overshoes to protect the deck from being dirtied.
CHIRP Comment
Safety regulations around pilot boarding exist because failure to follow them can and does result in injury or worse.
Here again is a common design problem often reported to CHIRP. There appears to be a lack of integrated thinking when designing superyachts. Crews should not be placed in unsafe situations due to poor design decisions made remotely by those who will operate the vessels. There must be collaboration during the design phase for new builds, with input from all stakeholders such as designers, owners, flag authorities, class societies, crew, contractors, and pilots.
This report clearly reminds us that pilots are contractors and guests, yet they remain vital maritime professionals. The safe transfer of the pilot is not optional; it is compulsory, and their physical safety and well-being must be taken seriously.
Key Issues relating to this report
Culture – The dismissive attitude toward the pilot’s safety — prioritising paintwork over people — reflects a poor on board safety culture. A culture that does not respect external personnel or reporting lines weakens trust and increases risk.
Communication – The Master’s refusal to remove the fenders and the failure to explain or resolve the issue collaboratively suggest a lack of effective communication between the ship and the pilot. Effective communication is crucial for achieving shared situational awareness and making informed, coordinated decisions.
Alerting – The pilot raised a safety concern, which was initially ignored; this constitutes a failure to act on an alert. Ignoring or dismissing raised concerns discourages others from speaking up and undermines the effectiveness of safety systems.
Teamwork – Boarding a vessel is a collaborative effort between the ship and the pilot. Filming the event and failing to help shows a breakdown in cooperative behaviour and mutual respect, key elements of effective teamwork.
Situational Awareness – The lack of recognition that the pilot had been injured, and the absence of any first aid or welfare check indicate poor situational awareness. The crew was not entirely focused on what was happening around them or the seriousness of the event.
Key Takeaways
Seafarers – Every visitor is your responsibility. Pilots and contractors are part of your extended team. They deserve the same duty of care as your crew. Ensure safe boarding arrangements, treat visitors with respect, and help without hesitation. A clean deck is no excuse for a dirty attitude.
Managers – Safe access is not optional – it’s the law. Boarding arrangements must meet SOLAS requirements — every time. Pressure to protect paintwork cannot outweigh the safety of personnel. Set clear expectations with your crews: all visitors, especially pilots, must be welcomed safely and professionally.
Regulators – Standards must protect people, not paint. Incidents like this show how operational decisions can put reputations — and lives — at risk. Regulators must reinforce the message that duty of care extends to all personnel boarding a vessel and that non-compliant setups or dismissive behaviour are unacceptable.
-
M2491
–
Crew AbandonmentCrew AbandonmentInitial Report
CHIRP received a report from several crew members who were abruptly dismissed from a 24m vessel after raising repeated concerns about living conditions and on board safety. The captain, who was also the vessel’s owner, terminated their contracts without notice, support, or provision for repatriation. It was only after intervention from an ITF Inspector that assistance was provided. This incident appears to meet the criteria for abandonment under the Maritime Labour Convention (MLC).
The crew had previously reported a persistent spider infestation in the accommodation spaces. One crew member required hospital treatment as a result. Alongside this, there were ongoing concerns about black mould, poor ventilation, and unsanitary accommodation. A heavily stained and damaged mattress was only replaced following a formal request. A missing toilet seat was replaced only after a complaint was lodged. There was no privacy in cabins due to the absence of curtains, and bathrooms were described as damp and poorly ventilated. These conditions made the crew quarters uninhabitable. The crew were relocated multiple times, including to a hotel, student dormitories without hot water, the captain’s private home, and other guest spaces.
In addition to the living conditions, serious safety concerns were raised. The vessel was reportedly operating in violation of SOLAS and Flag State safety requirements. All fire extinguishers were either expired, corroded, or inoperable. No flares were carried on board, and there were no life jackets available in the crew or guest cabins or anywhere within the vessel’s interior. Despite these critical deficiencies, the vessel continued to operate at sea, placing both crew and passengers at risk.
CHIRP Comment
This case highlights a broader concern regarding vessels operated solely by their owners, where the usual checks and balances provided by an independent management structure may be absent. When command and ownership are combined, especially on vessels under 30 metres, external oversight is often limited and accountability difficult to enforce.
CHIRP shares this report to encourage greater scrutiny of crew welfare and vessel safety on owner-operated yachts. It is essential that crew members feel able to raise concerns without fear of retaliation, and that enforcement mechanisms are strong enough to prevent recurrence of such incidents. Safeguards must also be in place to ensure that new crew are not recruited under false pretences, and that international standards such as MLC and SOLAS are consistently upheld.
CHIRP advocates extending MLC protections to all yachts, regardless of size or tonnage, because working conditions can vary significantly between MLC-compliant vessels and those that are not. The same applies to SOLAS: vessels not obligated to comply may operate under lower safety standards, and seafarers should be aware of these differences when seeking employment.
CHIRP encourages prospective crew to ask clear questions during recruitment and urges owners and management companies to take greater responsibility for ensuring compliance, transparency, and fair treatment across all vessels under their remit
Key Issues relating to this report
Communications – Crew concerns were often ignored or dismissed, and formal complaints were needed to prompt basic responses (e.g., mattress and toilet seat replacement). Are your concerns truly heard when you raise them?
Pressure – The crew were placed under pressure to remain in unsafe and unfit conditions without repatriation or protection of their welfare.
Complacency – The continued operation of the vessel despite expired fire extinguishers, the absence of lifejackets, and the lack of flares indicates a command that does not appreciate the risks regarding practical safety and compliance with safety regulations.
Local Practices – Unacceptable standards appear to have become normalised (e.g., operating with no lifejackets or uninhabitable cabins).
Key Takeaways
Seafarers – Know your rights, speak up and retain supporting documents.
Seafarers should document unsafe conditions and report them through formal channels. Understanding your rights under MLC is vital, especially regarding health, safety, and repatriation. If internal reporting fails, seek help from unions or ITF inspectors without delay.Managers – Safety concerns are not insubordination.
Dismissing a crew member for raising valid concerns undermines the safety culture and breaches international obligations. Managers must ensure compliant living conditions, maintain safety equipment, and respond constructively to crew feedback.Regulators – Where there is smoke, act fast.
This case highlights serious SOLAS and MLC violations. Regulators should prioritise oversight of vessels with combined owner-captain roles and act swiftly on signs of abandonment, poor habitability, or safety equipment failure. -
M2498
–
Crew Injury while MooringCrew Injury while MooringInitial Report
During routine mooring operations, while a crew member was in the process of heaving up the ground line, it appeared to be short. An attempt was made to use a messenger line, connect it to the ground line, and secure the ground line sufficiently on deck using the capstan before transferring it to the bollard. During the heaving operation, the crew member in charge at the mooring station repeatedly requested shore personnel to provide a better arrangement. Whilst they were attempting to solve this issue, the crew member operating the capstan continued to heave in the line until, unfortunately, the messenger line parted, causing the ground line to strike the crew member who was near the capstan at the time.
CHIRP Comment
CHIRP has contacted the reporter to find out how the injured crew member fared, and thankfully, they have recovered, but it was very fortunate that the injury was not more serious.
All the signs indicated that the ground line was too short, and while negotiating for a better arrangement, the operation continued, resulting in the messenger being over-tensioned and parting.
The Advisory Board commented that marina ground lines are often found in poor condition, increasing the risks to the crew during their use. Marinas should take greater responsibility for their condition and increase the frequency of their inspections and maintenance.
A risk assessment related to mooring in port should include ground lines as part of that assessment. The fact that the line was still being heaved on board despite concerns over its suitability was an excellent case for a “stop-work authority” to be enacted.
Key Issues relating to this report
Local Practices (Deviation) – The use of a short ground line and messenger workaround indicates a normalised departure from the standard procedure—a workaround that became routine under operational pressure.
Situational Awareness – There was a failure to maintain an accurate awareness of line tension and the risk of the ground line parting while negotiating with the shore.
Communication – Although concerns were raised, there was no effective closed-loop communication between the person in charge and the capstan operator.
Alerting – Repeated requests by the mooring station went unheeded, indicating a breakdown in the system of alerting and assertive challenge.
Teamwork – Lack of a shared mental model and coordination between shore personnel, the mooring leader, and the capstan operator.
Pressure – implicit in the fact that they continued the operations, potentially from schedule or routine expectations, and this overrode safety concerns.
Key Takeaways
Seafarers – If it doesn’t feel safe, stop.
Don’t continue unsafe work—stop and speak up clearly. Know the risks, don’t normalise shortcuts, and act on warning signs.Managers – Unsafe workarounds reveal unsafe systems.
Workarounds mean something’s wrong. Fix procedures, empower crews to halt unsafe tasks, and learn from close calls.Regulators – Deviations are symptoms, not root causes.
Focus on systems, not just actions. Promote human factors reporting and ensure procedures align with real-world demands. -
M2496
–
Chemical injury to the crewChemical injury to the crewInitial Report
An engineer was changing the chemical additive for the sewage treatment plant. While completing the operation, the chemical spilt, causing chemical burns to the crewmember. The crew member was not wearing any protective clothing and had not considered the risks involved in this operation. The crewmember immediately left the area and went to their cabin to remove the contaminated clothes and take a shower to wash off any chemicals.
A procedure was in place for handling hazardous substances and conducting a risk assessment.
The procedure required PPE, including a face visor, gloves, overalls and a chemical apron. Material Data Sheets need to be consulted before commencing the task, including briefing the crew on their contents and which instructions to follow. The engineer did not follow the procedure. They received refresher training following the event.
CHIRP Comment
This report highlights a breakdown in procedural compliance during a task involving hazardous chemicals. Although procedures and a risk assessment were in place, the crew member failed to wear the required personal protective equipment (PPE) or consult the relevant safety data before commencing the task. This underscores a critical point: safety documentation alone does not prevent harm—it must be understood and actively applied.
The engineer’s prompt and appropriate response following the exposure likely mitigated the severity of the injury.
Familiarity with routine tasks can lead to an underestimation of risks, particularly when hazardous substances are involved. Complacency in such cases can have serious consequences. This report serves as a clear reminder that safety procedures are not optional.
Familiarisation training must fully address the risks associated with chemical handling, including the personal, physical, and psychological safety aspects. The correct use of PPE is not a procedural formality—it is a critical safeguard. It must be consistently applied with the same seriousness as any other essential safety measure.
It is encouraging that refresher training was conducted after the event. However, further reflection is warranted to understand why the procedures were not followed in the first place. Was there time pressure? Were the instructions unclear? Did assumptions override caution? Effective learning from this incident should go beyond retraining and seek to identify and address the underlying conditions that contributed to the lapse. Doing so will help strengthen a proactive and resilient safety culture.
Key Issues relating to this report
Local practices – unless cases like this are highlighted, they can become the norm.
Complacency – the risk of underestimating liquid chemicals is potentially very hazardous.
Capability – training in the safe use of chemicals should be part of all crew familiarisation. Until familiarised, the crew should not be handling them.
Key Takeaways
For Seafarers, Shortcuts hurt; safety is part of the job.
Follow the procedures, wear the PPE, and don’t guess with chemicals. If in doubt, ask. Reporting protects everyone, including you.For Managers, What gets supervised gets done safely.
Embed procedures into daily practice, not just paperwork. Reinforce safety behaviour through presence, guidance, and learning from incidents.For Regulators, Policy is potential, practice is protection.
Focus on how rules work onboard, not just in manuals. Support training, reporting, and visible follow-through to keep learning alive.