FEEDBACK
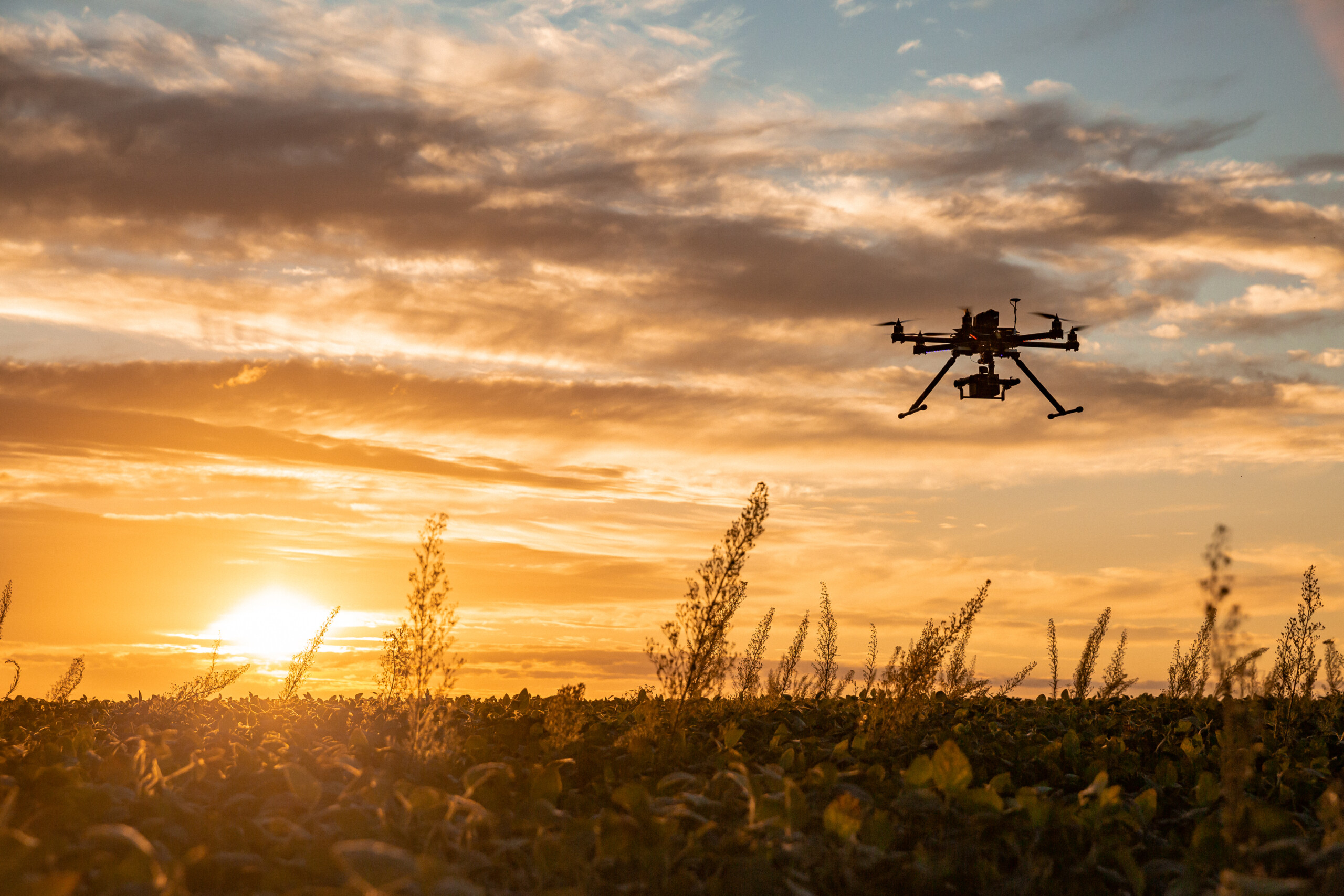
Attention to detail
Sometimes it’s easy to get absorbed in the task and lose sight of what’s around
Welcome to Drone FEEDBACK Edition 9.
Winter is upon us. Whilst the period since our last meeting in July has offered some ideal weather for Drone-based data scanning, as well as Drone transport trials, the winter months will provide some weather-related challenges. Think cloud, rain, icing, much lower temperatures that will reduce battery life, along with numb fingers that press the wrong buttons!
From a regulatory perspective, much policy development work is being undertaken on Pre-Determined Risk Assessments âPDRAâ, Airspace Modernisation and Temporary Restricted Areas or âTRAsâ. In addition, the CAAâs Safety Leadership Group or âSLGâ, which CHIRP has been asked to join, has had its first meeting. The SLG consists of a group of Drone Stakeholders that will help contribute to the continuing development of RPAS safety policy. CHIRPâs role will be to feedback Human Factors and Just Culture related recommendations into the SLG, so that they can be considered in safety policy development.
There have been a couple of notable events in the Drone ecosystem since July, including a great deal of chat about SORA 2.5, the precise wording in Operations manuals about the risks involved in the overflight of uninvolved persons and how they can be mitigated on renewal of OAs and new iterations of PDRAs. One particularly interesting Skywise Safety Notice (SN-2023/005) was published on 9th October referring to the accuracy or otherwise of Geo Fencing on some Drone systemsâ flight apps. This caught our eye because we have had reports of discrepancies between the accuracy of FRZs, prohibited areas etc marked on some Drone manufacturers Geozone Flight Apps, as distinct from where they are located according to the Aeronautical Information Publication or âAIPâ. Regular readers may remember FEEDBACK 3 dated January 2022, where this was highlighted with regards to a Prohibited area P611/2.2. The area was shown as a circle on the 1:500,000 Aeronautical chart but was delineated by a multiple sided polygon on the DJI Geo Zone Map. Â The basic message of SN-2023/005 is that Drone pilots are ultimately responsible for where they fly their Drone, and the AIP is the ultimate source they need to consult. Being aware of this point will help Drone Operators to stay safe and not fly somewhere they shouldn’t. (Data from the AIP is available in map form on the NATS UAS airspace restrictions page, link here: https://nats-uk.ead-it.com/cms-nats/opencms/en/uas-restriction-zones/ on DroneSafetyMap.com and in the Drone Assist app.).
Human Factor related errors will however continue to creep into day-to-day Operations and make life difficult. Letâs see if we can learn something from the occurrences described below.
Rupert Dent, Drone/UAS Programme Manager
Whilst not a formal DUAS report, the following has come to us via the CHIRP GA section and applies to the Drone and Modellers community. Figure 1 shows a copy of a NOTAM that was filed by a Model Club and contained an error that caused some confusion regarding the maximum height element. In one place a maximum height is quoted as being 640 ft and in another it is quoted as being 2,500ft. A correction to the report was subsequently published as shown in Figure 2.
The report to the GA Advisory Board goes on to deal with other matters, but for the Drone and Model Club Community we thought it was important to highlight that the accuracy of NOTAMS, which are filed by the relevant Operator, should be checked very carefully. In this instance we understand that the mistake was made during the manual transcription from the NOTAM form (that was completed correctly) into the NOTAM publication system. Remember also that NOTAMs are only advisory for other aviators (except the military who generally avoid all NOTAMâd areas where practical). A NOTAM does not confer any protection other than to advise of an activity, other aviators are at liberty to fly through them if they so desire (no matter how ill-advised) and so ground operators still need to keep a good lookout for other aircraft that might be in the NOTAMâd airspace.
Figure 1
Q) EGTT/QWUXX/IV/NBO/W/000/007/5138N00053W001
A) EGTT B) FROM: 23/10/09 12:19 C) PERM
E) CADMORE END, BUCKINGHAMSHIRE
LOCATION: 513811N 0005319W
UPPER LIMIT: 2500FT AGL
LOWER LIMIT: SFC
CONTACT: XXXXXXX MODEL AIRCRAFT CLUB XXXXXXX
SITE ELEVATION: 640FT
HOURS: HJ
UK AIP ENR 5.5 REFERS
F) SFC G)Â 640FT AMSL
Figure 2
Q)EGTT/QWUXX/IV/NBO/W/000/022/5138N00053W001 H7411/23
A) EGTT B) 2310171358 C)PERM
E) ADD NEW MODEL AIRCRAFT FLYING SITE CADMORE END, BUCKINGHAMSHIRE
LOCATION: 513811N 0005319W
UPPER LIMIT: 1500FT AGL
LOWER LIMIT: SFC
CONTACT: XXXXXXX MODEL AIRCRAFT CLUB XXXXXXX
SITE ELEVATION: 640FT
HOURS: HJ
UK AIP ENR 5.5 REFERS
F) SFC G) 2140FT AMSL
Rupert Dent
Drone/UAS Programme Manager
-
DUAS24
–
Minor collision with window catchMinor collision with window catchInitial Report
Minor collision with window catch resulting in no injuries and no damage to UAS/Drone.  During an FPV Indoor flight, when attempting to finish a transition to an open window, the UAS clipped the window catch causing it to lose control and fall to the ground outside from a height of 5m. The UAS fell vertically as designed and shut off power to the motors. The battery detached as designed on contact with the ground. Upon inspection no visual damage to the drone and no error messages received on power up. Test flight flown and normal operations resumed. Security have logged a near miss in accordance with their procedures, incident report form filed in accordance with OA and OM.
Upon Investigation the following conclusions were drawn:
- Whilst having an open window allows completion of a filming transition, best practice would be to keep the window closed and worst-case scenario accept a low-speed impact with the window by the UAS/Drone as opposed to moving between regulatory regimes from inside to outside filming.
- When flying in FPV (First Person View) it is accepted that there is a small increase in risk of collision due to the binocular view given by the goggles.Whilst this can be mitigated with experience, protruding obstacles such as the window catches may interfere with the Field of Vision in question and additional considerations should be made when planning the UAS FPV flight.
- Considering the potential risk of an impact with an uninvolved person when operating outside, a marshal or visual observer should have been present within what could be described as the cone of impact.Whilst the flight was never planned to fly externally, this consideration should have been made.
- Upon reviewing the footage, it appears the UAS was carrying out a braking motion (Nose Pitching Up) and in an almost stationary hover with minimal forward speed, it appears the collision happened as a result of the braking pitch manoeuvre, causing the impact with the window catch.
- One safety factor when using a quadcopter is that during a failure or impact the UAS spirals in a vertical path, which means that in this instance it fell extremely close to the building. However, in an event where the UAS had greater forward motion the cone of impact is increased.
- The controller used to operate the UAS in this instance does not allow the full range of motion (backwards flight) which may otherwise have prevented the incident after the collision.Consideration of flight path needs closer analysis to ensure any inability to fly backwards is mitigated adequately, or alternatively a standard controller allowing full freedom of motion should be used.
Lessons learned.
In summary it is important to consider the additional risks of FPV flight where a transition from indoor to outdoor flight is planned or a possibility. The Remote Pilot has been briefed on this and will ensure these additional risks are mitigated in future.
CHIRP Comment
Well, this is an excellent report for the FPV community. These days there are an increasing number of YouTube videos that have been taken by an FPV Drone flying indoors and oudoors, frequently transitioning from one environment to the other, several times. To my mind they create some remarkable cinematic effects and are likely to be used more often in the future. What is worth thinking about, however, is the transition from the indoors regulatory environment (essentially one governed by Health and Safety) to the outdoors regulatory environment (regulated by the Civil Aviation Authority) and, as pointed out in this report, the associated different risk mitigations that need to be considered.
One item that springs to mind from this report is the use of vision protection systems. If the FPV Drone in question had any in the first place, they must have been switched off in order to allow the transition. With them on, unless their activation distance had been reduced to a very low number indeed, they would have made it impossible to fly out of the narrow window, so we imagine they were switched off. If flying a pre-determined scenario using FPV equipment, the general issue of flying in close proximity to anything needs careful risk mitigation. Perhaps it would have been a good idea to fix some red tape to the window catch in order to have made it more visible to the pilot? If vision systems are switched off or are  just not available and there is no reverse functionality, these are two particular risk areas that need specific risk mitigation.
-
DUAS25
–
Lost sight of droneLost sight of droneInitial Report
Having searched the banks of the river I spotted a feature that required closer investigation. I attempted to circumnavigate the feature whilst keeping the drone’s camera facing toward the centre point. With eyes flicking up and down between screen and sky, at some point during this manoeuvre I lost sight of the drone. As per training, the safest way out of such situation is to fly straight upward; however, the drone must have been too close to a tree and the branches claimed it on ascending.
The drone’s position on the smart controller was clear, so I waded through the river and its boggy banks to find the drone wedged high up in the tree branches. I climbed the tree and was able to retrieve the drone. Â No visible damage to the aircraft or propellers. Test flights carried out and all okay. Proceeded with training exercise.
Additional answers to a number of questions that we put to the reporter:
1) How far away from the tree do you think you were, when you lost sight of it?
âAirData shows it as 145m from the home point (14 minutes into the flight)â
2) What sort of Drone was it?
âMavic 2 Zoomâ
3) Does the Drone have a Point of Interest function that would have enabled you to circle what you were looking at autonomously with a pre-determined radius?
âYes, I believe it does, however I cannot say that I have ever used it; but more to the point, in a search and rescue scenario it is highly unlikely that it would be used. However, in this instance, I was consolidating my flying practice, after passing my A2 CofC theory exam, and I was attempting to stretch my inner boundaries and increase my confidence.â
4) Does the Drone you used have a vision system that prevents it from encountering obstacles and if it does was it switched on?
âYes, it does, and yes it was active; but the overhead collision avoidance is done by dead reckoning (not by proximity sensors), and as it was only just underneath the overhanging branches, I think it would be unreasonable to expect it to work in this circumstance.â
Lessons learned.
This was too complex a manoeuvre to carry out without having a sensor operator, and too far away to have accurate understanding of the position of the aircraft relative to its surroundings.
CHIRP Comment
We agree with the idea of a pilot practising their skills at judging distance. Determining the relative distance between two far away objects is difficult at the best of times. But practising it alone is the most difficult way of learning. A pilot accompanied by an Airspace Observer (AO) is a better way of developing oneâs skills and learning how to do this. In this instance, it would have resulted in one set of eyes focussing on the controller and a second set of eyes staying focussed on the aircraft. If the AO had lost sight of the aircraft, they could have asked the pilot to hover and then approached where they had last seen the aircraft to improve the likelihood of locating it again. The perception of relative distance is dependent on several different variables such as visibility, background colour, light, distance and so on. Managing these variables as a team of two rather than one is advisable!
A point worth mentioning that is specific to rotary Drones is that if you lose sight of the aircraft at any point, it is always worth considering initiating a stationary hover, so the AO or the RP if it is being flown single crew, can then move towards where the aircraft was last seen, looking at the controller screen first, for general direction and to ensure there are no system failures. This might help to establish visual contact with the aircraft, before moving it any further.
With regards to the answers we received to our clarification questions, we feel it is worth noting two aspects:
- Whilst the Mavic 2 Zoom does have a vision system to warn of proximity to other objects, in our experience it does find it hard to identify the tips of tree branches. Later models have an improved dual system of sonar combined with an infrared system. However, caution when flying near trees is still recommended.
- The 145m visibility distance mentioned is roughly consistent with other estimates of the distance away from an observer when seeing an object of that size starts becoming difficult. Later models have strobes fitted both underneath and on top of the aircraft. Strobes might have made a difference in this case.
-
DUAS26
–
Broken propellor flangesBroken propellor flangesInitial Report
Upon completing a flight, the UAS was landed, and the battery changed. When starting the rotors for a subsequent flight the left rear propellor did not spin up as expected and a grinding sound was heard. The UAS and Controller were switched off and inspection of motor assembly was made assuming motor failure. Motor was resistant to rotation and assumed failed. On removing the propellor it was noted that two of the three flanges that secure the propellor to the propellor hub had failed and entered the motor housing (see pictures) There was no suggestion of this impact or damage prior to carrying out the previous flight. Total Estimated Flight time on the propellor set is in the region of 27 hours. The failed parts were removed from the motor housing and motor freedom was tested. The propellor was replaced and the UAS restarted. Ground running test completed satisfactory, and short flight test completed satisfactorily and UAS returned to service.
The UAS is checked both prior to flight and post flight before being packed away. It is noted that this is the required check in the Operations Manual and complies with the requirements of the OM and Flight Reference Cards. It is important here to recognise that there is currently no requirement to perform a transit check upon each take-off and landing or after each battery change.
From a Risk Assessment point of view, it may be the path of least resistance would be to incorporate a transit check after each take-off and landing; however, this could potentially quickly become arduous to the point Remote Pilots will not carry it out.
A reasonable compromise is that, in line with carrying out a repeat control check, the Motors and Propellors are inspected as part of a transit check during each battery change. This provides the best compromise I believe, between checking every flight and only checking pre and post flight therefore reducing risk to an acceptable level and is in line with the Operating Practices for a Normal Take-off with this Operator. A “normal take-off” being (Lookout; Announce “Take Off”; Start UAS motors manually using controller; Increase height to above head level, perform a control check in Pitch, Roll, and Yaw).
One possible failure mode that was considered after the event was observed is the way that the UAS is unfolded and folded. If Remote Pilots were to continually use the propellor to extend and unfold the arms this could put excessive stress on the propellor hub flanges over a period of time and eventually weaken the structure to the point of failure.
Below are pictures of the broken propellor flanges and the motor with the two flanges that had broken off stuck in the housing.
Lessons learned:
Consider adding an interim hardware check after each take-off and landing or each battery change.
Review of Propellor loading and replacement requirement (currently 100 hours).
Inspection of all other propellor hubs.
CHIRP Comment
This is an excellent example of Human Factors with a positive outcome. The fact that a check was undertaken between flights enabled the issue with one of the propellers to be identified before it caused an accident. The aircraft in question was a DJI Mavic 3. This is in fact a relatively new model from DJI. The DJI Phantom 4 had several issues with its propellors, and it is disappointing to see a possible recurrence of a propellor weakness on the Mavic 3. Whilst this is not necessarily an operator-related HF issue, it is perhaps a manufacturing related HF issue, in quality control. The reporterâs suggestion of checking propellers between each flight would be a sensible mitigation, particularly in a world where if one comes off in flight, the ground risk is substantial. After all, a variety of basic checks is very much something that happens between flights in the crewed aviation world. You should always for example check full and free movement of the controls between flights. The reporter interestingly mentions that folding and unfolding the rotor arms by holding the propellors themselves rather than the arms may have been an underlying cause of stress on the flanges. We think that if this was indeed the way the arms were being unfolded, it may well be a root cause of the flanges being sheared off.
CHIRP recommends that folding and unfolding propeller arms is always done by pulling the arm itself rather than the propellor blades.
Collectively, we need to monitor whether other occurrences like this are reported in the future. The Mavic is a widely used aircraft and quality related issues associated with manufacturing the propellor attachment need to be identified as early as possible. It is worth noting that on some DJI models with folding rotor arms, the design has been changed and the propellers are now permanently attached using screws. Whilst it is uncertain whether this is a mitigation against previous problems associated with propellors being detached from the hub, it is worth keeping an eye on the new arrangement to see if it leads to separate issues.
-
DUAS27
–
Information not diseminatedInformation not diseminatedInitial Report
Whilst flying over a section of railway for the purpose of undertaking an inspection, we had informed ATC at a particular aerodrome of our requirement to fly in their FRZ. The permission to do so had involved completing a template form and emailing it along with a copy of our OSC approval, insurance certificate and Flyer IDs of the flight crew. This had been done several weeks before the date we were aiming to fly our DJI M300 over the stretch of railway that was within the FRZ.
On finally receiving a verbal approval, but no email to evidence it, we took the precaution of visiting the aerodrome on the day and heading up the tower we obtained approval from the duty controller. Satisfied we had done all that was necessary, we returned to our TOAL site to fly our missions. We were flying at 55m above ground level and were directly under the active runwayâs climb out route, but around 500m from the departing runwayâs threshold. Fortunately, we were between two flights, so were on the ground at the time, but a departing flight school aircraft cut its power on climb-out and just before it reached the railway line. It descended rapidly towards where we were going to be flying our next mission before power on the aircraft was restored and it resumed its climb out before turning crosswind. We were relieved that we had chosen that moment to return home for a battery change.
Once we had finished on site and curious to understand why the departing aircraft had chosen to practise an Engine Failure After Take-Off (EFATO) manoeuvre at exactly the spot where we had told ATC we would be flying, we returned to the aerodrome to chat to the duty controller. After some discussion it transpired that even though the controller knew where we were, the information was not being passed on to departing pilots. We all agreed that it would have been wiser to inform departing traffic of the possible sighting of a Drone on climb out, not only for general awareness but also to avoid practising EFATO manoeuvres on departure.
CHIRP Comment
This is a âfirstâ occurrence of this type, because it involves safety information not being passed on to pilots in circumstances where it might have made a real difference. The Drone pilot had clearly done everything necessary to request approval from ATC to fly in their FRZ, and had received approval, but that is where the information flow then stopped. It isnât clear why the information was not passed on to pilots, but it seems to CHIRP that there should be a process whereby it is considered relevant information that should be passed on to pilots operating in the zone, even if ATC service being provided was classified as Air to Ground. Â FRZâs exist amongst other things to make sure that air risk associated with Drone flights is controlled in an area where there is likely to be crewed aircraft flying as well. The information flow does however need to be two way. Crewed aircraft need to be informed about Drones and vice versa. We would be keen to hear from ANSPs what their current practice is with regards to informing crewed aircraft pilots about Drone activities they know about and have authorised in their respective FRZs. In this instance the instructor would presumably have radioed after takeoff that he was about to perform an EFATO, which would have presented an ideal opportunity for the ground controller to respond with information about the presence of a Drone in the extended centreline if that information had not already been passed to the aircraft before its take-off.
-
DUAS28
–
Propellor icingPropellor icingInitial Report
I was on a live deployment. I conducted a short test flight to check for icing on props as the temperature was close to zero. After a short time, I recognised a change to the drone’s handling characteristics so landed. On inspection, the drone had icing on propellers (see picture). No further flights were conducted.
Lessons learned.
It was a reminder of the importance of checking local environmental conditions when flying the drone. A thorough risk assessment led me to conduct a test flight and take extra precautions.
CHIRP Comment
A concise report that serves as an excellent example of what to do prior to a deployment, urgent or otherwise, in the winter season. We can only congratulate the pilot for a very sensible approach to safe flying. Looking at the photographs of the propeller, the aircraft would have very quickly lost any available lift if the flight had continued. A point to highlight is that the temperature was âclose to zeroâ without being either zero or minus. It is important to remember that icing can occur at temperatures above zero and, although the nominal freezing point of water is 0°C, water in the atmosphere does not always freeze at that temperature and often exists as a “supercooled” liquid. If the surface temperature of an aircraft structure (such as a propellor) is below zero, then moisture within the atmosphere may turn to ice as an immediate or secondary consequence of contact in such conditions. Ice may form on propellers just as on any aerofoil. It reduces propeller efficiency and may induce severe vibrations.