Our syndicate aircraft had been in and out of action for a few months over the summer as a consequence of some engineering work, following permit expiry. On resuming flying, two members of the group observed that the fuel tank was not venting correctly and that a vacuum was forming during flights, leading to a pronounced ‘whooshing’ sound of the air rushing in once the fuel cap was opened. I was asked to investigate, with my assumption being that the filler cap vent had somehow become blocked, or got some debris in it.
The filler cap is one of those components that everyone handles on a regular basis â and knows roughly what it looks like â but when asked to recall the object in detail, chances are you haven’t paid it sufficient attention to be able to recall all of its intricacies. On many permit-aircraft like ours it’s round, relatively flat and unremarkable in feature: you couldn’t get a more unexceptional part on many aircraft, I’m sure.
On inspecting the aircraft, I removed the filler cap and couldn’t see any indication that it was capable of venting, leaving both myself and other group members perplexed as to whether there was an alternative vent for the tank. What were we missing?
It was only after further examination â and asking the distributor for the aircraft kit whether there is an alternative venting arrangement for the tank â that we found the issue was staring us in the face. Can you guess what it was?
On removal of the engine cowling came the proof: somehow, someone had managed to replace the oil filler cap with the vented fuel filler capâŠand placed the (unvented) oil filler cap onto the fuel tank. In plain sight, it was so obvious: the oil filler cap has a symbol of an oil can on it. But it looks, feels and FITS exactly as the fuel tank filler cap does.
Not only did it catch us out, but further investigation â including going back through old photos â suggested it had been like that for over 8 previous hours of flight.
Had this not been picked up, any of our members might have experienced fuel starvation and an undesirable flight outcome, particularly had their flights been slightly longer and more fuel consumed.
There are lots of things to learn here as well as some old lessons that could be re-iterated.
First, the importance of conducting pre-flight checks sequentially. We cannot establish how it came to be that the oil filler cap AND the fuel filler cap were both off the aircraft at the same time. Had the fuel levels been checked and the cap replaced BEFORE moving on to check the oil, the first hole of the Swiss cheese wouldn’t have existed.
Second, it’s useful â albeit very difficult (as an ‘unknown unknown’) to pre-identify and highlight components that might be subject to confusion or mix-up. I would think it’s highly unlikely that two components of an aircraft would be capable of fitting so perfectly in different locations â it is both a questionable design feature as well as a stroke of poor luck that both the oil filler cap and fuel filler cap are of identical dimensions. Then again, perhaps it is more common than we thought? It would be a useful exercise to query whether the same mix-up is possible in other aircraft types.
Third, it’s amazing just how much confirmation bias came into the equation here. Even though we were looking directly at the oil filler cap, 5 different pilots failed to notice that it was the wrong cap. It is very easy with the benefit of hindsight to say that ‘it has an oil can symbol on it’, but it’s quite faded, not very noticeable, and easily overlooked when you’re focussing more on the underside of the cap to check it’s the venting type. How many people lift off the oil filler cap without looking at it also?
Fourth, it would be prudent to improve the marking or labelling of the filler caps. One option in our case might have been to have a fuel filler cap of the same colour as the fuselage, which would then have looked completely incongruous against the oil reservoir had it been put there.
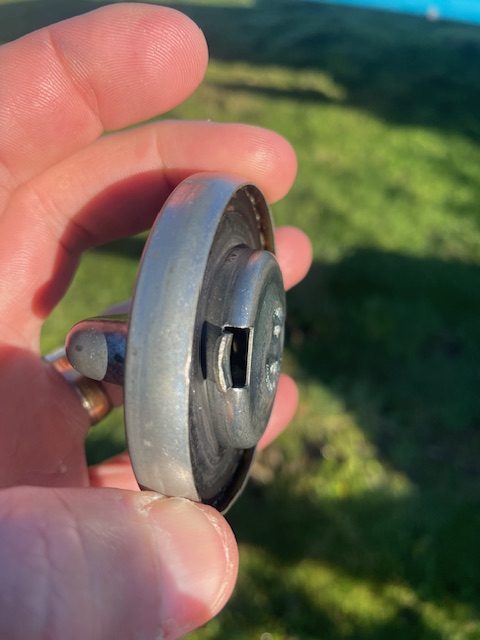
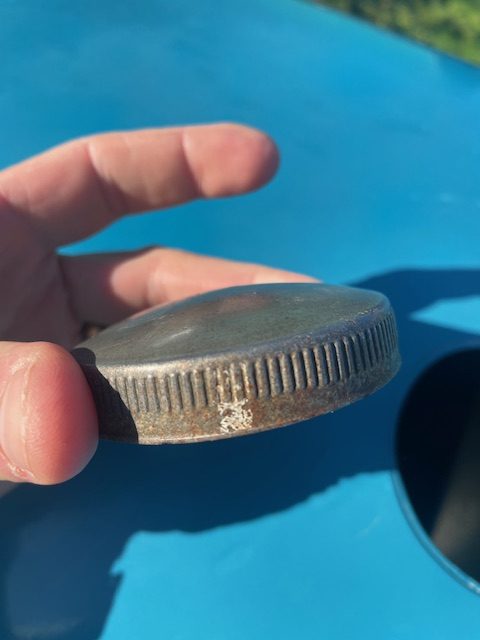
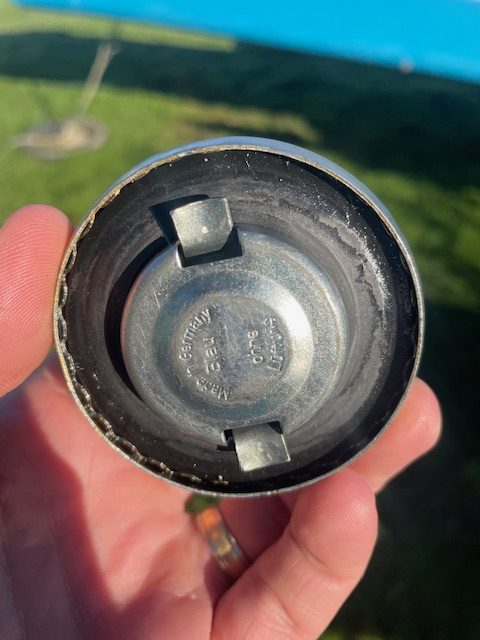
CHIRP Comments: Notwithstanding the authorâs comments about confirmation bias, habituation, assumption and perhaps complacency, this tale is a classic Human Factors trap where Murphy strikes again. These days, great efforts are made in aviation design and manufacturing to avoid situations where components can be installed in the wrong locations or the wrong way around, but sometimes things slip through.
During in-depth hangar maintenance there are a number of reasons where both the oil and fuel caps might be off at the same time if both systems are being worked on for some reason, but careful storage and labelling of disassembled parts is one way of preventing mix-ups. Thereâs little reason for both to be off during routine line-maintenance or replenishment tasks, but itâs easy to see how it might happen if people are trying to be organised in preparing the aircraft for top-ups.The idea of differing the colour of the 2 caps is a good one because that means that the caps are not being physically altered but can easily be differentiated from each other â yellow for oil caps is a fairly common colour, and that would stand out if placed on the fuel filler pipe. Another option, if feasible, is to have one or both caps attached to their respective filler pipes by a suitable chain or lanyard of some description so that they canât be moved away from their intended location. Many such caps are secured this way, so perhaps thereâs scope for looking at doing that on at least one of the caps if appropriate, or fixing/replacing an existing chain if thereâs one intended to be there thatâs broken or missing.
We currently receive CANP requests via email; the tool used by users inputs their data on their application and generates the request to us in the form of an email. We then promulgate an H-series NOTAM for the request. But we would only do this for drones/models etc operating visual line of sight and up to a max altitude of 400ft AGL. Anything beyond 400ft AGL is processed by AR Ops at the CAA. Their procedure for Airspace Co-ordination and Obstacle Management (of drones above 400ft and other activity categories) is at link https://applications.caa.co.uk/CAAPortal/servlet/SmartForm.html?formCode=BAL).
We do refer members to use CANP and include some guidance in our Membersâ Handbook at https://handbook.bmfa.uk/9-the-bmfa-guidelines-and-safety-codes-for-model-flying (see section 9.5). It is also set out within UK Regulation (EU) 2019/947 âUAS Regulationâ (https://regulatorylibrary.caa.co.uk/2019-947-pdf/PDF.pdf). We could very easily create a portal (similar to the BHPAâs) which would fire off a notification to MAMC (we created a similar system for Occurrence Reports which automatically sends them to AAIB, CAA and CHIRP). Weâd like to make these additional points though:
We agree that NOTAMs are less than ideal for our purposes, but at present it seems to be what weâre stuck with as itâs something that all airspace communities utilise. A system similar to the BHPA CANP process but which notifies all airspace users would certainly be of interest to us.