FEEDBACK
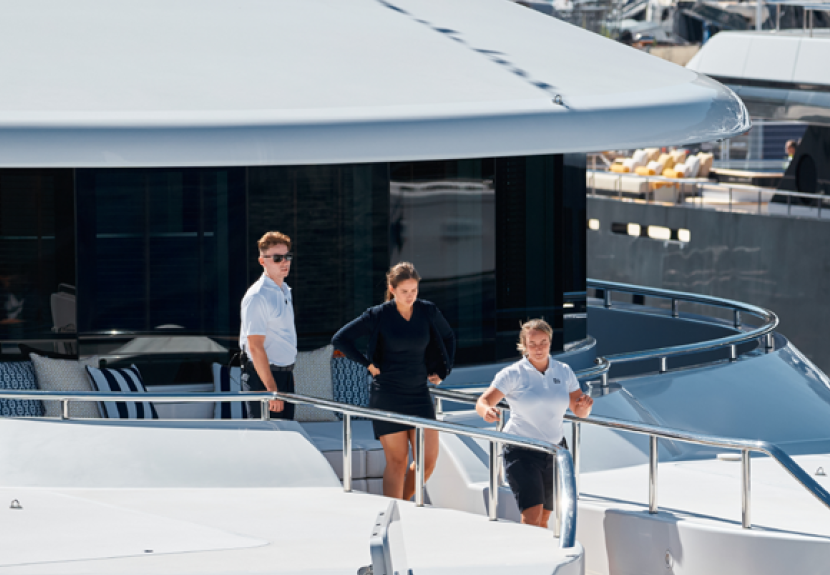
Building a Safer and More Inclusive Superyacht Sector
While challenges such as workplace harassment and equipment maintenance issues are concerning, they also serve as a reminder of the vital role every stakeholder plays in fostering a positive onboard environment. A crew member’s account of harassment by a captain sheds light on the importance of open communication and accessible reporting channels. Harassment can deeply affect one’s confidence and ability to perform, but this incident also showed the power of solidarity. Fellow crew members rallied to provide support, demonstrating how teamwork and a shared commitment to respect can make a difference. By continuing to promote training and clear policies, the industry can create safe spaces where all crew members feel valued and heard.
Similarly, safety concerns such as improperly maintained life rafts and other critical equipment reveal areas for improvement in oversight and education. These findings highlight the importance of thorough inspections, routine maintenance, and fostering a safety-first mindset at all levels. While it’s encouraging to see crew members taking the initiative to identify risks, this responsibility must be shared by companies and regulatory bodies. Working together, we can ensure that vessels remain not only operationally sound but also prepared for any emergency.
Every challenge presents an opportunity for growth. By embracing a culture of accountability, compassion, and proactive safety practices, the superyacht sector can develop a culture of safety and inclusivity for all.
-
M2293
–
Harassment on boardHarassment on boardInitial Report
The reporter told CHIRP they were in an uncomfortable situation on board while working on a temporary contract.
“Our captain has acted unprofessionally, creating a hostile work environment that makes it hard for me to do my job. This is my first role in the industry, so I reached out to a colleague, who confirmed that the captain’s behavior was not normal or professional.
The captain constantly sought me out, especially during my night shifts, to discuss personal matters, which made me feel uneasy. He stayed awake to talk even though it was not his usual habit, and it disrupted my focus.
One incident really stood out: we had an hour to go ashore, and the captain insisted on joining me. Another crew member noticed my discomfort and assured me that others found his behavior inappropriate, too. During this outing, he kept asking me to join him at a restaurant, despite my refusals. When I reminded him that I was there to work, he pushed back, asserting his authority as captain to justify taking more time. I had to set boundaries repeatedly, but he ignored them.
Back on the vessel, the night shift issues continued—he’d stay up, offer to do my tasks, and try to start personal conversations. I had to find another area to work, but he followed me, persisting with the interactions. At one point, he presented a new seasonal contract, despite my earlier refusal, and seemed upset when I declined again.
The situation escalated during another night shift. After promising to drop the subject, he returned from bed shortly after to try discussing personal matters again, disregarding my request to keep things professional. I was so uncomfortable that a crew member offered to stay with me so I wouldn’t be alone with him.
Later, at a crew gathering, he followed me back to the boat and tried engaging in more personal talk. I eventually began recording the conversation to document his behaviour. When he wouldn’t stop, I called a friend, then another crew member, to avoid being alone with him. The tension culminated in him making a derogatory remark before finally leaving.
This morning, the captain created a group chat and called for a meeting today. He also sent me contract termination rules, saying I need to give seven days’ notice. Right now, I’m in my cabin, unsure how to proceed. I feel very uncomfortable here and cannot continue in this environment.
While I am unharmed, I am deeply upset that this situation has disrupted my work, my contract, and my learning experience. I’ve stayed professional, but I’m at a loss on how to handle this. Any advice on how to proceed today would be greatly appreciated. Thank you.”
CHIRP Comment
No crew member should endure this harassment. Companies employing masters must provide firm guidance that any form of harassment is unacceptable and will not be tolerated. Such guidance should apply to all superyacht crew and contractors.
CHIRP understands that the master was dismissed by the company, but nothing prevents them from being rehired by another company. The reporter has also left this company and found safer and more rewarding work elsewhere.
Key Issues relating to this report
Culture- Unbeknownst to the company, the master used their position of authority to behave unacceptably. A safety culture cannot exist if people feel unsafe.
Communications: The crew rallied around the reporter to shield and protect them. Reporting your concerns is one of the most powerful tools you have—do not suffer in silence.
Alerting: Many organisations in the maritime domain are very willing to assist anyone going through such harassment, including CHIRP Maritime, which will escalate the matter to the DPA and Flag State if the company cannot resolve it. You are not alone. Please spread the word.
If you are facing harassment or discrimination on board, here are some practical steps that you can take:
- If you feel safe doing so, tell someone or contact one of the organisations below.
- Keep a record. This will be useful evidence if you decide to make a formal complaint or report.
YachtCrewHelp +44 2037 133273 (call) +44 7514 500152 (WhatsApp)
Provides emotional, wellbeing and practical support 24/7/365 – free and confidential Safer Waves support@saferwaves.org Befrienders Worldwide Support For Seafarers Have call centres in Spain, Gibraltar, China/HK and Philippines. CHIRP +44 20 3876 8588 Report your safety concerns 24/7/365 -
M2296
–
Unsafe pilot transfer arrangementsUnsafe pilot transfer arrangementsInitial Report
A pilot informed CHIRP that during embarkation onto a super yacht, the pilot ladder rungs were not horizontal, and the ladder was not shackled to the deck. There were no fixed stanchions, and oversized fenders obstructed the ladder. There was no cut-out in the deck-level belting, so the ladder hung away from the ship’s side.
CHIRP Comment
The overhanging superstructure makes it impossible to meet SOLAS regulations for boarding arrangements, which require the ladder and spreader bar to rest firmly against the hull. This is a fundamental design flaw. Note that boarding arrangements have to be SOLAS compliant irrespective of whether or not the vessel itself has to be SOLAS compliant.
The International Maritime Pilots’ Association (IMPA) poster Pilot Ladder Poster.pdf is free to download and provides guidance on rigging compliant boarding arrangements. Surveyors for Flag states and classification societies must ensure boarding arrangements meet safety standards. CHIRP will raise this issue with the Flag State concerned.
In consultation with pilots, CHIRP has suggested that the following guidance be provided for all visiting super yachts to ensure compliance with the pilot transfer arrangements (PTA) regulations.
- Specific super yacht pilot ladder guidance will be issued to visiting yachts during their visits.
- Specific super yacht pilot ladder guidance is to be issued to pilots.
- Vessels that do not comply with the requirements must receive a letter stating that they must rectify this before their next call.
- The Harbour Master is to be contacted when booking vessels for their next visit for early engagement to ensure that past issues have been rectified.
Key Issues relating to this report
Design– Designed for aesthetics and not for operational requirements.
Local practices- Check that your boarding arrangements comply with the regulations – use the poster referred to above for guidance.
-
M2301
–
Battery explosion on superyachtBattery explosion on superyachtInitial Report
During a shift of anchorage positions, the vessel experienced an incident in the lower engine room when the power management system (PMS) initiated the startup of a third generator. This action was necessitated by the increased load on the switchboard and the use of the bow thruster. Shortly after the generator was brought online, a loud, short-duration bang was heard and felt throughout the lower engine room. Following this noise, the generator’s battery alarm was triggered, prompting immediate concern. The engine room crew quickly reported the situation to the bridge, and as a precaution, the yacht was anchored as safely and swiftly as possible.
Upon investigation, the crew detected acrid-smelling smoke and discovered that two generator starter batteries had exploded in the engine room and were severely damaged. The force of the explosion shattered the battery’s fibreglass covers and damaged the floor plates.
A build-up of hydrogen gas, a by-product of the chemical reactions that occur when charging the batteries, was assessed as the cause of the explosion. A spark from nearby electrical equipment possibly ignited it.
A more thorough investigation revealed that the batteries were not of sufficient capacity for their intended use, which significantly increased the risk of uncontrolled failure. The previous chief engineer was aware of this issue but failed to communicate it to the incoming chief engineer during the handover process.
CHIRP Comment
Although recent focus has been on issues surrounding Lithium-Ion batteries, many other battery types remain common across the industry. This incident underscores two critical areas of concern: battery management and operational handovers.
Regular maintenance and inspection of battery systems are critical, especially regarding capacity, condition, and proper ventilation. Insufficient ventilation can lead to danger. Batteries smaller than the recommended size or lower in ampere-hour (Ah) capacity can explode when used or charged.
The outgoing engineering team demonstrated poor engineering standards in continuing to knowingly use under-capacity batteries, which should have been replaced at the earliest opportunity. At the very least, the design deficiency should have been documented, reported to management, and mentioned during the handover to a new engineering team.
Key Issues relating to this report
Alerting- The off-going engineer did not arrange for the batteries to be replaced immediately despite knowing they were unsuitable.
Overconfidence—Even though the team knew the risks of using the incorrect equipment, they continued using it. This inaction could have cost someone their life and threatened the vessel’s safety.
Communications—It is unlikely that the chief engineer was the only person who knew about the underrated batteries. Critical equipment items must be discussed so that risks can be communicated, safety concerns can be identified, and action can be prioritised.
CHIRP has received several incident reports concerning battery maintenance and use and wants to provide some key safety tips.
1. Make sure the batteries are correctly rated for the installation 2. Check for deformation, corroded terminals and blocked vents 3. Ensure that the electrolyte, where appropriate, is maintained at the correct level 4. Battery storage boxes are to be well-ventilated and capable of regular physical inspection. 5. Battery load tests to be carried out regularly 6. Voltage monitoring to ensure that overcharging is not occurring. Remember- Correct rating, preventing overcharging, and safe ventilation of hydrogen fumes are key to preventing an explosion. -
M2299
–
A ‘bitt’ of a hazard!A ‘bitt’ of a hazard!Initial Report
The mooring bitts pictured above had a D-ring attached to them, which was used as the strong point for connecting a rope stopper. When the weight of the mooring line came onto the stopper, the D-ring’s connecting screws sheared off, and the D-ring was fired into the air towards the mooring party. Luckily, no one was injured.
CHIRP Comment
Stoppers – and whatever they are connected to – must be capable of supporting the loads transmitted through the mooring lines. The small-diameter screws connecting this D-ring to the bitts were entirely inadequate for this task. A better arrangement would be to attach the standing end of the stopper around the bitt or a nearby cleat.
Key Issues relating to this report
Design—If your super yacht has a similar design, ask the manufacturers to confirm its safe working load (SWL).
Local Practices: Any equipment designed to take a load should be documented in the vessel’s SMS and inspected/tested as appropriate.
-
M2290
–
Working aloft without proper PPE (again!)Working aloft without proper PPE (again!)Initial Report
This photograph, taken from a nearby yacht, shows crew members working aloft without visible fall arrest equipment (e.g., harness, safety line) or other PPE.
CHIRP Comment
We often receive photographs of similar incidents. When we contact the vessels concerned, we are usually told that these are individual crew members who have not complied with the vessel’s SMS for working at height.
The regularity of the photos submitted to CHIRP – often several each month – suggests that such behaviour is normalised across the industry. At best, it demonstrates that many vessels do not adequately supervise their crews, and at worst, it suggests that, on some vessels at least, such behaviour is actively condoned to save time. In reality, donning a safety harness is much swifter than dealing with a severe medical emergency following a fall from a height.
CHIRP has previously highlighted the dangers of working aloft when the crew’s safety is completely disregarded. The Flag State has been notified of the matter and is investigating.
Whilst the fundamental principle is that we are all responsible for safety, many crew members will not challenge the orders of a superior officer if it means they will risk losing their employment.
Key Issues relating to this report
Culture—In an industry where reputation is paramount, it is shocking that overt signs of poor safety culture are still prevalent. This dangerous practice must not become normalised. Transforming the culture of safety is not just necessary—it is urgent.
Teamwork—Vessels with a strong teamwork ethic can stand together and challenge unsafe work practices. Have you experienced this type of teamwork on your vessels? If not, CHIRP is here to advocate for you.
-
M2302
–
Collision at anchorCollision at anchorInitial Report
A wind shift caused the swinging circles of two superyachts anchored overnight in close proximity to overlap. One vessel noticed this and started its engines to manoeuvre away from the other, but it could not do so before they inevitably collided. The other vessel did not respond to verbal and radio calls from the first vessel until after the collision because its bridge was unmanned. Luckily, the damage was minimal.
CHIRP Comment
Although at anchor, a vessel is still at sea and should ideally remain on sea watches, including with a manned bridge. However, many smaller vessels do not have sufficient personnel to stay on sea watches and simultaneously meet guests’ needs.
In our first edition of Superyacht FEEDBACK (Report M2088), we noted that one of the more difficult tasks for a captain is to moderate the owner’s or guests’ expectations. This includes the uncomfortable conversation that their vessel might not be crewed to safely operate at sea overnight—even at anchor—while simultaneously running tenders ashore and supervising the use of water toys, etc.
This is one instance where a comprehensive risk assessment, which refers to scenarios like the one above, can help. And as we noted in that first edition:
“Shrewd owners will accept that the captain is looking after their interests… [and if they don’t]… this should be a ‘red flag’ to the captain that safety on board at some point will be compromised. Better to seek alternative employment.”
Key Issues relating to this report
Situational Awareness—The bridge should remain operational to identify and control reasonably foreseeable hazardous scenarios even when at anchor. This includes timely observation of changing weather conditions and the risk of collision.
Culture- Safety is always paramount, even if that means disappointing owner/guest expectations.
Local Practices: Review existing risk assessments regularly. Refer to incident reports published by CHIRP and others to identify potential safety risks.
-
M2307
–
Life raft maintenance was ignoredLife raft maintenance was ignoredInitial Report
Upon boarding a large superyacht which had been relocated between continents, the reporter prioritised safety checks. They discovered both life rafts needed to be correctly rigged and were mislabelled, with unreadable hydrostatic release units (HRUs). One life raft had a painter line incorrectly secured to the cage instead of the HRU, while the other life raft was not secured to any fixture.
Seeking immediate action, the reporter sent the rafts to a nearby manufacturer for annual servicing. The manufacturer identified serious discrepancies, including oversized strapping that could potentially hinder the life raft canister opening.
During an inflation test witnessed by the yacht manager and deck crew, both rafts exhibited alarming issues: water infiltration, mould, corrosion of some fittings, and disconnected gas cylinder firing pins. Corroded high-pressure gas lines further compromised safety, leading to one line’s failure during testing, emitting CO2 into the workshop.
These findings underscored the rafts’ unfit condition, with expired flares and unprotected safety equipment, which would have posed grave risks in an emergency.
The new management has carried out a rigorous inspection regime to ensure that the vessel’s safety has been brought to a state of operational readiness.
CHIRP Comment
Life rafts are essential life-saving appliances and must be properly maintained. The service company responsible for this maintenance should always be reputable and approved. Unfortunately, no maintenance had been conducted, and inspections—both internal and by the flag and port state—had failed to identify the problems. Additionally, crew members were unaware of the condition of the life rafts, their hydrostatic release units, or their securing points. This highlights a serious lack of safety culture within the company, leaving the crew with equipment that would not function in an emergency.
It is excellent practice, as the reporter demonstrated, to witness the inflation of the life rafts during servicing by the appointed company. Doing so ensures that maintenance standards are upheld and reassures the crew that the life rafts will function correctly when needed. The reporter deserves commendation for prioritizing safety upon joining the vessel. The flag state were altered to the poor quality inspections.
Key Issues relating to this report
Capability: The failure to recognize an unsafe situation with the life rafts highlights a lack of knowledge and experience among the crew at all levels. During safety inspections on your vessel, do you participate in the inspection process? During safety drills, are life-saving appliances (LSA) explained to you? Do you know the correct method for securing the life raft hydrostatic release units?
Culture: Do you feel that the company employing you as crew on board your vessel genuinely cares about your safety?
Alerting: The reporter has gone the extra mile to highlight how poor the safety conditions on the vessel are. These actions have led to a positive change in safety practices.