FEEDBACK
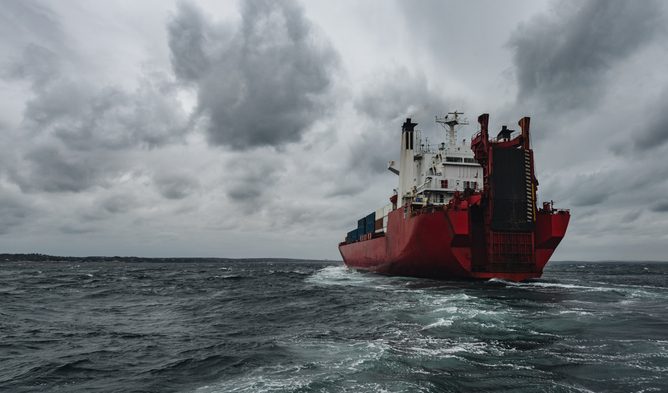
Recurring risks, missed chances
Maritime safety culture – we’re not there yet.
Once again, we’re privileged to share real-world reports that provide valuable learning insights for the entire maritime community, and our sincere thanks go to the seafarers and maritime professionals who have taken the time – and shown the courage – to submit them.
There is a report about the dangers of heavy weather and another about the proper use of voyage data recorders. We also learn about a dangerous lifting operation, an accident during a rather unconventional pilot boarding, and a fire extinguisher that could not have been readily accessed in an emergency.
As always, there are common factors across the reports despite the different subjects covered. Situational awareness and poor communication are the most common failings, followed by poor safety culture, lack of teamwork and complacency. All these factors can be eliminated through proper training and establishing a vibrant safety culture on board. Still, it is evident that many of us are a long way from achieving that ideal. We can and should be doing better.
Our regular readers will note that we have included a new section in each report, listing key takeaways for seafarers, ship managers, and regulators. These highlight simple steps to improve safety yet further, and we hope that you find them helpful – please let us know!
We always pay close attention to comments from our readers. Your insights help us improve, and your reports can help others to stay safe. If you have experienced or witnessed something worth sharing, don’t keep it to yourself – together we can improve maritime safety for all.
Until next time, stay safe and may all your voyages lead you safely home.
The CHIRP Maritime team
-
M2256
–
Fatalities during heavy weatherFatalities during heavy weatherInitial Report
The weather forecast indicated an approaching low-pressure system with strong winds and increased swell activity.
At 0500 the pilot disembarked, and the master instructed the crew to secure all lines and deck equipment. The aft station was reported secure, but the crew left the forward station unfinished, planning to return later. The master handed over the con to the third officer and left the bridge. During the passage, heavy swell caused the vessel to slam against waves, waking the master, who ordered a speed reduction and course adjustment. By midday, the second officer took over the watch, with increasing wind and three-meter waves.
After lunch, the chief officer went on deck to check that the containers were still secure. Around the same time, the bosun and deck crew returned to complete securing the forward station. A short while later, a large wave breached the forecastle, washing crew members off their feet. The chief officer found four injured crew members and raised the alarm. The master altered course towards the nearest port, and the injured crew were transferred to the ship’s hospital. A medevac request was considered, but it was not possible, and the vessel proceeded to port, where paramedics boarded that evening. Two crew members later died due to their injuries; another required emergency surgery, and one was treated onboard.
The pre-departure safety meeting addressed weather conditions and crew responsibilities. Nevertheless, access to the deck remained unrestricted. The company’s heavy weather checklist was not utilised, as it lacked clearly defined thresholds for heavy weather.
CHIRP Comment
Several key opportunities to prevent this incident were missed: crew members at the forward station should have remained until the area was secure; the master should not have proceeded to sea until they were satisfied the vessel was secure; and the handover to the third officer should have included the status of the forward station.
As the weather deteriorated, the master and OOW should have dynamically assessed whether the upper deck remained safe for personnel. The lack of guidance regarding upper deck operations in the company’s heavy-weather checklist was also an indirect causal factor.
The chief officer’s swift response to the alarm and the master’s decision to alter course toward the nearest port were appropriate actions. However, being unable to carry out a medivac underscores seafarers’ ongoing challenges in accessing timely medical support. This highlights the need for improved coordination between vessels and shore-based emergency services, especially in remote areas.
Despite the pre-departure safety meeting addressing the weather conditions, access to the deck remained unrestricted. This raises concerns about how effectively safety briefings are implemented in practice. Furthermore, the company’s deck access code procedures and heavy weather checklist lacked clear thresholds to guide the crew’s decision-making, leaving room for ambiguity in assessing the risks of worsening sea conditions. This incident is a powerful reminder that risk checks, clear communication, and adherence to heavy-weather procedures must never be overlooked. Lives were lost—needlessly. If this report encourages even one crew member to stop, think, and act more safely, then something meaningful can emerge from this tragedy. Please don’t wait until it’s too late. Choose safety—every time.
Key Issues relating to this report
Local Practices- Accepting local practices which are not in accordance with best seamanship practices creates an unnecessary hazard.
 Culture— There appears to have been a laissez-faire attitude toward securing a vessel for the sea. Does your vessel have a deck access code when encountering heavy weather?
Teamwork—By working as a team, they could have secured the forecastle quickly and efficiently. There appears to have been no challenge to leaving it unsecured.
Overconfidence– Weather may be unpredictable, but poor preparation isn’t.
Overconfidence– Weather may be unpredictable, but poor preparation isn’t.
Key takeaways
Seafarers – “Your actions shape the safety culture onboard.”
Local habits that ignore best practices put everyone at risk. Speak up, challenge unsafe norms, and work together—especially in heavy weather. If something feels wrong, it probably is. You are the first and strongest line of defence.
Ship managers – “What you walk past, you accept.”
A culture of overconfidence or casual preparation starts ashore. Managers must set clear expectations for securing the ship for sea and adverse weather and ensure crews are trained and supported to follow them. Audits should not just check boxes—they should test real-world readiness.
 Regulators – “Standards mean nothing if they are not applied.”
There is a vital difference between compliance and safety. A vessel can tick all the regulatory boxes and still be unsafe. Regulators must recognise when local practices undermine global standards regarding paperwork and real-world safety outcomes. Intervention should go beyond audits, including proactive oversight, education, and follow-up. The goal is not just compliance—it is genuine safety. That cannot be left to chance.
-
M2450
–
Voyage Data Recorder (VDR) issuesVoyage Data Recorder (VDR) issuesInitial Report
During a company fleet-wide navigational audit, several discrepancies and procedural gaps were identified after comparing the passage plans, bridge logbooks, and Voyage Data Recorder (VDR) data. A significant observation was that passage plans lacked an anchor plan, which is required by the Bridge Procedures Guide (BPG). Additionally, there was no objective evidence to verify the frequency of position fixing or proof that radar was used to plot the ship’s position to ensure secure anchorage.
Although supported by radar recordings, parallel indexing was not observable during critical wheel-over manoeuvres. There was also no indication of regular checks at frequent intervals to confirm that the vessel remained securely anchored by taking bearings of fixed navigational marks. In several instances, only the X-band radar was operational during anchorage, and essential data points such as the actual date and time were absent from the passage plan.
The method of obtaining the ship’s position was not specified, and parallel indexing was not utilised while the vessel was underway in coastal waters. Although connected to the VDR, the echo sounder was not monitored, and the rudder angle indicator was absent from the VDR live player. The passage plan was not updated to reflect changes in circumstances, such as drifting, and the anemometer, despite being connected to the VDR, displayed data only on the radar screen.
The X-band radar was found to be switched off at a critical point during anchorage, and the depth indicator was not visible on the VDR live player, even though the Echo Sounder was connected. Furthermore, the ECDIS voyage log contained an incorrect year, and the master approved the standing orders and passage plan. However, despite the SMS checklist indicating that the ship’s position was verified through bearings of fixed navigational marks, the VDR data provided no supporting evidence.
During the voyage, radar playback identified nearby vessels, with the closest point of approach breaching the master’s requirement in the standing orders. Not all targets were acquired, and only radar trails were monitored throughout the passage.
CHIRP Comment
The significant discrepancies in passage planning procedures raised serious concerns about the vessel’s navigational safety. These issues were uncovered during an internal audit rather than by external authorities.
Key failures included the lack of parallel indexing, the absence of position verification, no anchor plan, and inadequate use of radar plotting during critical stages of the voyage and at anchorage. Additionally, the master who approved the passage plan did not directly oversee the planning process. This highlights a fundamental breakdown in compliance that requires immediate corrective action to maintain safety standards.
A fleet-wide audit by the company found similar issues across all vessels, suggesting that this was a systemic issue rather than isolated non-compliance.
CHIRP cautions all companies to take a closer look at their navigational procedures to ensure that they meet the requirements of the company SMS and the bridge procedures guide (BPG).
Key Issues relating to this report
Culture: Unsafe norms have developed, making non-compliance routine and accepted. Complacency, norms, and lack of knowledge create a dangerous environment. Training, leadership, and culture play critical roles, indicating systemic issues beyond individual lapses.
Communication: Insufficient communication between the bridge team members and the master led to gaps in the execution and understanding of the approved passage plan.
Complacency: Repeated non-compliance across the fleet suggests unsafe norms have become accepted, such as not updating the VDR or omitting radar plotting. This indicates a dangerous level of complacency.
Capability: Deck officers lacked the training and knowledge to properly maintain the VDR and conduct thorough passage planning, including anchor plans and radar usage.
Alerting: Junior officers may not feel empowered to question inadequate plans or voice concerns, perpetuating unsafe practices due to a culture of silence.
Situational Awareness: Poor understanding of critical navigational steps, from radar use to anchoring procedures, indicates a broader issue of a lack of situational awareness and risk appreciation.
Teamwork: The bridge team’s lack of coordination, proper monitoring, verification, and shared responsibility in navigation and data logging points to systemic failures in internal communication and a culture discouraging speaking up.
Key Takeaways
Seafarers, “Feeling normal doesn’t mean it is safe.”
Just because something feels routine, like skipping radar checks or not updating the VDR, does not mean it is safe. Speak up. You are the eyes and ears of safety onboard. Do not stay silent. Raise concerns, look out for each other, and practice solid seamanship. Your voice matters and can save lives.
Ship managers, “Same problem, many ships? That is a management issue.”
If crews repeatedly cut corners, look at the training, leadership, and support they are getting. Make sure crews know what is expected and feel confident speaking up. Safety culture starts ashore, and it is your responsibility to build it.
Regulators, “Administrative compliance cannot mask operational risk.”
When critical tasks like radar plotting or passage plan checks are skipped across a fleet, it is a sign that the system, not the sailor, may be broken. Regulators must look beyond paperwork and into practice. Targeted SMS audits, anonymous crew feedback, and follow-up visits can reveal where safety culture fails. -
M2257
–
Entanglement and fall from height during lifting operationsEntanglement and fall from height during lifting operationsInitial Report
A crew transfer vessel was performing lifting operations at an offshore wind turbine. A deckhand and a trainee deckhand were assigned to receive four lifting bags attached to a three-legged wire sling. The trainee lowered the load, detached it from the slings, and signalled the crane operator to raise the hook.
As the hook and wire sling were raised, they became entangled with the trainee’s work restraint lanyard. The trainee immediately signalled an emergency stop, but the crane operator neither saw nor heard the signal. As a result, the trainee was lifted off the deck. While suspended, the trainee’s weight caused the entanglement to release, leading to a fall of approximately one to two metres onto a pile of bags on the deck.
The trainee’s lanyard was worn loosely, increasing the risk of snagging. Additionally, the trainee was too close to the lifting equipment and did not use a tagline or maintain control of the equipment to prevent entanglement. The crane operator’s failure to respond to the emergency stop signal further exacerbated the situation.
CHIRP Comment
While lifting operations can be undertaken by only two people, ideally, three people should be involved: a crane operator, a rigger, and a banksman/supervisor. In this incident, the trainee deckhand was acting as the rigger, and the more experienced deckhand was the banksman, who should have ensured that the trainee was correctly dressed (with no snagging hazards) before the work commenced.
To be safe, all persons should remain in sight of one another, and operations should stop automatically if line of sight is lost.
Key Issues relating to this report
 Situational Awareness—Before starting any lifting operation, assess your position and that of the other crew members. Never begin the lift if you are uncertain.
Capability—Rigorous and reinforcement training should be given to the crew working in these high-pressure environments. How often do you carry out lifting operations training?
 Communications—Clear verbal and visual communication is essential for safe lifting operations. Crane operators should not start lifting until they communicate with the deckhand.
Alerting- The crane operator and the deckhand were not alone, and other crew could have assisted by advising that safe lifting operations had not been established. If you saw this situation, would you step in to stop the job if you saw this happening?
Pressure- There can be pressure when there is a deadline to meet. Even if no one says it out loud, you feel it. But pressure should never override your training. The job is important, but so are you.
Key Takeaways
Seafarers, “If you are unsure, stop the lift.”
Before any lift, check your position and where your crewmates are. If something does not feel right, speak up. You are not alone—support each other and stop the job if needed. No task is worth a life.
Ship managers, “Good training keeps crews safe under pressure.”
High-pressure operations need high-quality, regular training. Focus on real-life scenarios, not just checklists. Reinforce what good looks like—and give crews the confidence to act when things feel wrong.
Regulators, “Look beyond the paperwork—watch how people work.”
Safe lifting depends on clear communication, awareness, and confidence to speak up. Check if procedures work in practice. Support systems where stopping a job is seen as good seamanship, not failure. -
M2262
–
Pilot falls into the water while boardingPilot falls into the water while boardingInitial Report
While boarding a small tanker moored in port, a trainee pilot fell into the water when the bulwark ladder tipped over. The pilot boarded from the stern of the pilot boat onto the bulwark ladder platform without using a pilot ladder. This occurred because the tanker was fully loaded and had very little freeboard, and the shape of the hull made it difficult for the pilot boat to come alongside parallel.
To climb onto the ship, the pilot held onto one of the ladder’s stanchions. The ladder was not fixed to the deck, something that only became clear after the fall. As the pilot pulled on the stanchion, the ladder swung out over the side, unbalancing him and causing him to fall backwards into the water. The ship’s crew reacted quickly, helping the pilot back onto the deck. From there, he could return to the pilot boat sitting higher in the water than the loaded tanker.
CHIRP Comment
This report highlights the risks of using non-standard or non-compliant pilot boarding arrangements. Unless this was a training evolution for the trainee pilot, one wonders why they did not board from ashore using the ship’s gangway since the tanker was alongside.
In this case, the pilot stepped from the stern of the pilot boat onto a bulwark ladder platform, which was not secured to the deck. This suggests a lack of supervision when the platform was rigged. The ladder moved as the pilot grabbed a stanchion, causing him to lose balance and fall.
Fortunately, the crew responded quickly and helped the pilot recover safely.
Key Issues relating to this report
Communication—The pilot was not informed that the bulwark ladder was unsecured. This is a systemic issue that operators and owners should address.
Situational Awareness– The pilot did not visually identify the unsecured ladder. The simplicity of the arrangement may have led to a false sense of safety.
Complacency– The absence of a pilot ladder may have led to underestimating the risk. Any deviation from standard practice should warrant a dynamic risk assessment before boarding the vessel.
Teamwork—The ship’s crew and pilot coordination was limited. Shared mental models and clear roles are essential, particularly during high-risk transfers.
Key Takeaways
Seafarers, “If it is not secured, it is not safe.”
Always check that pilot ladders and transfer gear are correctly rigged and secure—every time. Unusual arrangements or last-minute changes must be clearly explained. When in doubt, pause and verify. Shared safety starts with shared understanding.
Ship managers, “Non-standard should not mean unsafe.”
If a vessel routinely uses non-standard pilot arrangements, you must ensure that proper equipment and procedures are in place. Do not rely on workarounds. High-risk transfers need leadership, training, and the right gear, not assumptions.
Regulators, “Pilot transfer safety is a systemic issue.”
Recurring failures in pilot transfer arrangements show a gap between regulation and reality. Strengthen oversight on compliance and equipment. Encourage audits that include transfer observations and act where unsafe norms have developed. -
M2280
–
Safety equipment obstructed by cargo gearSafety equipment obstructed by cargo gearInitial Report
As the reporter prepared to disembark a Ro-Ro, they noticed that a heavy-duty ratchet strap impeded access to a fire extinguisher. The strap secured a wheeled dolly supporting drop trailers on the car deck. The ratchet strap was pulled taut over the extinguisher, meaning it would have to be released before it could be used.
The reporter could not investigate further because they were about to drive off in their vehicle. They did notice that other frames were available to secure the dolly.
CHIRP Comment
Obstructing access to essential safety equipment, such as fire extinguishers, poses a significant risk during emergencies. Due to the fuel in the vehicles, the fire hazards on Ro-Ro ferries are exceptionally high. SOLAS clearly states that fire safety equipment must remain unobstructed and ready for use.
While securing cargo equipment is critical, the wheeled dolly support arrangements should have been incorporated into the ship’s design. If the supports were an additional item of cargo gear used by the company, their securing should have been planned to make alternative securing points available. This highlights the importance of regular deck inspections to ensure safety equipment remains unobstructed and accessible.
Fortunately, within 24 hours of CHIRP bringing this incident to the management company, they audited their entire fleet and confirmed that the issue had been resolved. The company’s speed of response was impressive, and CHIRP wants to thank them for their proactive stance on safety.
Key Issues relating to this report
Situational Awareness– The individual securing the dolly did not recognise the potential danger of blocking the fire extinguisher, highlighting a failure to consider safety equipment accessibility during a fire response.
Local Practices- The dolly could have been secured using alternative frames, suggesting a lack of adherence to best practices or established procedures to ensure safety equipment remains unobstructed.
Over-confidence. There is a degree of overconfidence in securing cargo equipment without considering the potential consequences of accessing safety equipment in an emergency.
Communication— Are the crew approachable and welcoming or intimidating to passengers?
Key Takeaways
Seafarers: “If it is blocked, it is as good as broken.”
Always ensure fire extinguishers and emergency gear are easy to see and reach—no exceptions. A few seconds lost in a fire can cost lives. Think before you secure anything: Will the lashing arrangements get in the way when it matters most?
Ship managers: “Securing cargo gear should never compromise use of safety equipment.”
Local shortcuts can creep in over time. Reinforce clear guidelines: emergency equipment must always stay visible and accessible. Encourage crews to double-check, not just tie down and move on.
Regulators: “Passengers see things inspections can miss.”
Blocked safety gear during regular sailings suggests a cultural lapse. Unannounced checks in real-world conditions could reveal issues that do not appear during formal inspections. Passenger feedback can be a valuable safety signal. -
M2454
–
Chemical exposure in the engine roomChemical exposure in the engine roomInitial Report
While tidying up the engine room, an engineer placed several empty chemical drums in the workshop for disposal. The engineer used blue tape across the drums to indicate they were empty and wrote “Empty” on them. However, one drum still contained a small amount of residual acid.
Later that afternoon, a motorman entered the workshop to dispose of the drums. Unsure of the contents since the safety data sheet was covered in blue tape, he opened the cap and attempted to identify the contents by smell. The fumes caused severe inhalation exposure, leading to his hospitalisation for the remainder of the day.
The vessel had purchased several chemicals from the same supplier, including engine room detergents, acids, bases, and defoamers, all stored in identical containers. These were typically distinguished by safety data sheets attached to each drum. However, the labelling was obscured, creating a hazardous situation.
CHIRP Comment
Proper labelling of chemical drums is essential. Original labels must remain visible until containers are thoroughly cleaned and decontaminated. Never cover or remove safety data sheets. Use standardised “Empty” labels that don’t obscure critical information. Even small residues can pose serious risks. Drums must be drained, cleaned, and vented before being marked as empty. A designated “chemical residue area” can help manage partially emptied containers safely.
Safe handling is vital. Never try to identify chemicals by smell. If in doubt, check the safety data sheet or ask a senior officer. A “Stop and Check” policy should verify contents before handling or disposal. Always wear appropriate PPE—gloves, eye protection, and respirators—and use portable gas detectors when necessary, especially around unknown substances.
Suppliers should simplify identification with colour-coded drums or clear hazard markings. Drums for disposal should include decontamination instructions. To improve safety, review procedures regularly, enhance crew training on hazard awareness and PPE, and consider improved labelling systems. Work with your supplier to ensure better identification.
Key Issues relating to this report
Complacency—The label marked “empty” led to assumptions that it was safe without verifying its contents. The operator could not confirm the chemical type or contents but proceeded regardless.
Communication—There may have been no clear briefing or shared understanding of what was in the drum. There may have been a reluctance to question or challenge due to rank.
Situational Awareness—The leader did not foresee the impact of leaving chemical residues in “empty” drums. No thought was given to downstream risk (throughout the disposal process), showing a lack of hazard anticipation.
Culture—The need for better chemical handling procedures and awareness training points to systemic issues in how safety is embedded. In this case, the processes allowed hazardous residues to be overlooked or poorly identified.
Key Takeaways
Seafarers: “Do not trust the makeshift label—know what is inside.”
Just because a drum says “empty” does not mean it is safe. Never use smell to guess what is in a container—check and confirm. If something does not feel right, speak up.
Ship managers: “A chemical near-miss is a system failure.”
Training and procedures fail if the crew relies on labels or their noses. Reinforce clear communication about hazardous substances. Regardless of rank, ensure everyone feels confident raising a hand before risk becomes harm.Regulators: “Risk doesn’t stop at the worksite—it travels downstream.”
Chemical residues left in so-called “empty” drums pose serious disposal risks. Review how hazardous waste is labelled, handled, and signed off. Operational spot checks should test actual practices.