FEEDBACK
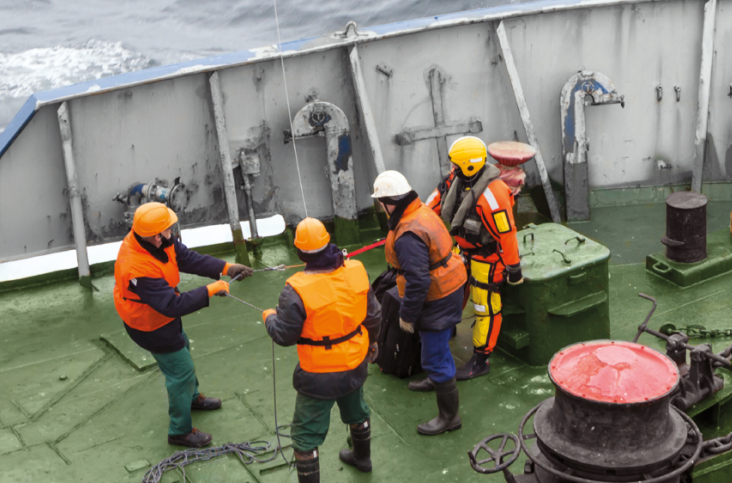
The human cost of maritime incidents
Organisations often state that they put safety first. Regrettably however, commercial and reputational realities often obstructs the realisation of this lofty ambition: rather than view incidents as an opportunity to learn from experience, some companies go to great lengths to present themselves as being 100% safe, 100% of the time. But in an industry known to be more âdangerousâ than many others, this simply canât be correct.
The sad news of Captain Oguz Kok, who recently died during a night pilot transfer in the Bosphorus reminds us of the dangers inherent in the maritime industry. And while many, including ourselves, were quick to express condolences and offer thoughts for his family and friends, the collective maritime industry needs to do more to improve safety.
According to British anthropologist Robin Dunbar, the average person maintains relationships with approximately 150 friends and family. The true cost of a safety incident therefore goes far beyond those immediately involved; the injuries and incidents that occur in our industry literally touch millions of lives.
CHIRP is aware of several cases where those reporting safety concerns through their organisationâs reporting channels have faced redundancy or reprisals. Such suppression only serves to ensure that safety issues are not addressed, and the risk of repeat incidents remains stubbornly high.
CHIRPâs independent, impartial and confidential reporting system allows individuals and companies to raise safety concerns and issues without the risk of reprisal, or loss of reputation. The following reports were sent to CHIRP to raise awareness of risks across the industry, or to share best practice, or to get an issue addressed. In many of these reports, you will read that CHIRP advocated for the reporter by raising the issues with the company or Flag State while protecting our reportersâ identities.
-
M2205
–
Asphyxiation hazardAsphyxiation hazardInitial Report
A crewmember entered a freezer compartment for routine duties where, unknown to them, dry ice was being stored. The crewmember quickly lost consciousness because of the high CO2 levels produced by the dry ice. Luckily, another crewmember quickly raised the alarm, and they were rescued and given first aid. They were then sent to the hospital for a confirmatory check-up.
CHIRP Comment
The decision to transport dry ice for culinary presentation carries significant risks, and management is responsible for them. The management team must thoroughly evaluate the associated risks at the organisational level before approving the procurement of dry ice.
Strict adherence to regulations and guidelines is essential when dealing with dry ice, considering its inherent hazards. Key considerations involve recognising dry ice as a dangerous good (UN 1845) and understanding the specific risks it poses during transportation. Compliance with regulations becomes vital for ensuring the cargo’s safety and the well-being of the individuals involved in its handling. Emphasis must be placed on proper handling, packaging, and ventilation to mitigate the risks of transporting dry ice. A thorough risk assessment must be conducted to ensure that all potential hazards are explored.
Since the dry ice is sourced from a franchisee/sub-contractor, it is imperative to communicate detailed information regarding its hazards, proper handling, and safe storage to various stakeholders, including management, the master, the chief officer, the chief engineer, and all ship’s staff. The storage compartment for dry ice immediately falls under the classification of an enclosed space, requiring an enclosed space permit for entry.
Solid dry ice must be packaged in non-airtight containers to allow the safe release of carbon dioxide gas produced during sublimation (change from a solid to a gas without becoming a liquid), thereby preventing container overpressure and the associated risk of an explosion. Adequate ventilation becomes crucial, avoiding the accumulation of carbon dioxide gas in enclosed spaces and mitigating the potential for asphyxiation for anyone working in the compartment. Entry into a fridge space containing dry ice necessitates a permit to work.
Comprehensive training for crew members handling dry ice is a management responsibility. It covers hazards such as explosion, suffocation, and tissue damage due to extremely low temperatures. Training programs must highlight the importance of proper ventilation and avoiding unventilated compartments. Management should establish robust mitigation strategies and emergency response procedures, including incorporating personal gas detectors and enforcing appropriate PPE to prevent skin contact damage.
Key Issues relating to this report
Capability- Dry ice, or solid CO2, demands good knowledge to mitigate the risks. Does your shore management team have the necessary skills to manage the risks for the crew? Have you been aware of the dangers if you have carried it, especially on a cruise liner or superyacht? Did you know that it is classified as a dangerous goods cargo? Have you received training in the handling of dry ice?
Communication- How well are you aware of the carriage of dry ice in the galley fridges of other compartments where it may be stored? Are these spaces labelled as enclosed spaces?
How is this communicated to everyone on board?
Alerting- A crew member nearly died because of a lack of knowledge of dry ice and its hazards. Does your company provide extra information on dry ice carriage? Have you seen dry ice’s material safety data sheets (MSDS)? Have they been explained to you?
-
M2209
–
Marpol contraventionMarpol contraventionInitial Report
Several reporters informed CHIRP that their tanker was burning Intermediate Fuel Oil (IFO) Â with a sulphur content of 2.4% even though the vessel was not fitted with an exhaust gas cleaning system (scrubber) to reduce the sulphur content to below 0.5%Â as required by Marpol VI reg 14. The ship trades worldwide and is not fitted with an exhaust gas cleaning system (scrubber) to reduce the sulphur content below 0.5%. (Marpol VI reg 14). To avoid detection, they knew the vessel switched to burning marine diesel fuel when operating in ports or emission control areas (ECA).
The reporters were highly concerned about reporting this matter because the vessel is part of the âdark fleetâ of vessels breaking international sanctions. They were fearful of potential reprisals should their identity become known.
CHIRP Comment
Following extensive communication with the reporters, CHIRP raised these concerns to the Flag State, the designated person ashore (DPA), and the Hull and Machinery Insurers.
This report illustrates the lengths to which some irresponsible vessel owners will go to circumvent regulations designed to protect the environment. This is likely because the cleaner fuel is more expensive, and the company puts profit over safety.
The incident also suggests that Flag and Port State inspections should be reviewed to ensure that such behaviours can be detected. Vessels admitting to carrying fuel exceeding the 0.5% limit should be required to demonstrate how they intend to reduce sulphur levels, either through a scrubber system or another method.
The exhaust gas cleaning system should only be considered a temporary measure, and ultimately, all ships should be converted to using low-sulphur-compliant fuel.
Key Issues relating to this report
Culture- The vessel’s organisation does not appear to be invested in environmental compliance. This is perhaps unsurprising given that the vessel is involved in âsanction bustingâ. The requirement to burn cleaner fuels or have scrubbers fitted has been in force for three years. Is your vessel following the rules?
Pressure- The company uses economic pressure to conceal the vesselâs non-compliance with Marpol, but if caught, the monetary fines will outweigh any short-term savings.
Local Practice- The practice of a company operating ships which are not fitted with an exhaust gas cleaning system must be ended. If you are operating on a vessel with a similar operation, please get in touch with CHIRP.
This data type is not supported!
-
M2206
–
Personal injury due to not following a permit to work for working aloftPersonal injury due to not following a permit to work for working aloftInitial Report
The OOW spotted a faulty navigation masthead light warning on the bridge’s navigation light control alarm system while the vessel was at sea. The issue was reported to the chief engineer and master, but due to the sea state, the decision was made to wait until the vessel was alongside before going aloft.
Immediately upon coming alongside, while the rest of the crew were busy rigging the gangway, the chief engineer climbed up the mast without completing the permit to work for working aloft or wearing a safety harness. While the CE was up the mast, the wake of a passing vessel caused the vessel to roll violently, causing the CE to fall and break their arm.
CHIRP Comment
The decision to delay attending to the light while underway at sea was correct. Once alongside, vessel motion can still be affected on both large and small ships, especially as the shipâs stability can change significantly during cargo, bunkering and ballasting operations. Contacting the port authority to check on vessel movement for the time the work is carried out is standard practice.
The fact that the Chief Engineer went aloft so swiftly indicates a self-imposed time pressure to get the task done as soon as possible. Similarly, not following safety procedures before going aloft suggests that the chief engineer succumbed to optimism bias (also known as the âIt wonât happen to meâ syndrome). More concerningly, it points to poor safety culture and safety leadership: if others see the chief engineer (who is very often the shipâs safety officer) taking safety shortcuts, how does this incentivise the more junior crewmembers to follow safety procedures?
Key Issues relating to this report
Culture- When it comes to safety culture, senior officers must lead by example and model the safety behaviours they want their team to adopt. As the saying goes, it is better to set an example than to be one!
 Alerting- Making sure that the master/safety officer and crew were aware that the light was going to be fixed would have alerted everyone to the requirement to use the permit to work for going aloft. Does your vessel operate a permit-to-work system when going aloft?
Situational awareness- Being aware that even in a port where conditions are not affected so much by environmental factors, you can sometimes overlook the dynamic action on your vessel by passing vessels.
Pressure- There appeared to be pressure to get the work done. This work should have been allocated to crew members who are more used to working aloft. The permit to work for going aloft could have been supervised by the chief engineer. How do you control your permits to work? Do you know the rank of your safety officer?
-
M2207
–
Potentially lethal near miss: elevator maintenancePotentially lethal near miss: elevator maintenanceInitial Report
Our reporter stated that they were asked to open a vesselâs elevator doors so that a cleaning crew could ride to the top of the elevator for cleaning purposes.
The reporter explained to the cleaning crew why this would not happen and how they must plan to do the work. The reporter provided a copy of a flag state incident report highlighting a severe injury to a crew member, which is produced here:
A senior engineer on a large yacht was preparing the passenger lift for a service technician to undertake remedial work on the decorative coverings in the lift shaft. The technician was not affiliated with the lift manufacturer or any lift servicing supplier and was on board solely to attend to the decorative coverings in the lift shaft.
The senior engineer called the lift car to the bridge deck and then entered the lift shaft onto the car top by manually opening the door on the Sun Deck and stepping onto the car top. When the lift doors on the sun deck closed, the lift rose to the sun deck position, crushing the engineer between the car top and the top of the lift shaft. The engineer sustained severe injuries to his legs and ankles and was off work for a considerable time.
The reporter is confident that similar practices are taking place on other ships with elevators and wanted to draw our attention to this. Although nothing happened in this case, there have been incidents where people have been crushed to death when working on the top of an elevator that wasnât properly isolated.
CHIRP Comment
Our reporter stated that they were asked to open a vesselâs elevator doors so that a cleaning crew could ride to the top of the elevator for cleaning purposes.
The reporter explained to the cleaning crew why this would not happen and how they must plan to do the work. The reporter provided a copy of a flag state incident report highlighting a severe injury to a crew member, which is produced here:
A senior engineer on a large yacht was preparing the passenger lift for a service technician to undertake remedial work on the decorative coverings in the lift shaft. The technician was not affiliated with the lift manufacturer or any lift servicing supplier and was on board solely to attend to the decorative coverings in the lift shaft.
The senior engineer called the lift car to the bridge deck and then entered the lift shaft onto the car top by manually opening the door on the Sun Deck and stepping onto the car top. When the lift doors on the sun deck closed, the lift rose to the sun deck position, crushing the engineer between the car top and the top of the lift shaft. The engineer sustained severe injuries to his legs and ankles and was off work for a considerable time.
The reporter is confident that similar practices are taking place on other ships with elevators and wanted to draw our attention to this. Although nothing happened in this case, there have been incidents where people have been crushed to death when working on the top of an elevator that wasnât properly isolated.
Key Issues relating to this report
Culture- Capability for this work could be improved, given the high risk associated with lift operations.
Complacency- A casual attitude to the work was displayed, which has probably been evident in the past and has been accepted as the norm. Does your SMS have procedures for lift maintenance? If so, are these made known to contractors working on the lifts?
Capability- Are there introductory safety training courses for the shipâs staff in lift maintenance? This is usually left to a qualified lift technician from the lift manufacturers to carry out. Do you involve your lift manufacturer?
-
M2208
–
Bunker station designBunker station designInitial Report
A reporter sent a video highlighting the poor design of the bunkering station on a very large yacht. They told us that super yachts use a variety of bunkering facilities, and it is very rare to connect with a Marpol flange.
Most bunkering hoses have cam-lock fittings, and because of poor design issues at the bunkering station and poor maintenance of the camlocks, many connections leak, creating pollution, health hazards, and fire hazards.
CHIRP Comment
Design issues with bunkering connections often need to be thoroughly thought out. Bunker connections are frequently positioned in tight spaces, making it difficult to connect the hose. Once connected, the connecting flanges can often come under much stress due to poor alignment, making a tight seal difficult to achieve.
CHIRP requests owners reconsider their bunkering design and, during the next drydock or lay-up period, consider changing the pipework to ensure connections are positioned to allow better alignment and a tighter seal to prevent leakages while bunkering.
Persistent leakages when bunkering are unacceptable and indicate a normalisation of deviance, where this practice is accepted as the new norm.
Key Issues relating to this report
Design- The design needs to be improved for secure bunkering. The workspace for hose connections needs to provide adequate space to allow alignment for the camlock. Does your bunker station have sufficient clearance to obtain good alignment when bunkering?
Alerting- Alerting management to the fact that buckets must not be used to control leakage from a bunker connection and should not be tolerated. Management should also be advised of the remedial action required to be taken.
-
M2194
–
Unsafe tug/barge operationsUnsafe tug/barge operationsInitial Report
Our reporter was very concerned about the operational practices used in their tug and barge operations:
âAs a new employee and apprentice in the industry, my onboard experience has raised serious doubts about the overall safety culture and protocols in place. While on the tug, I observed a significant need for more familiarisation and the absence of buddy support. Instead of being paired with a qualified deckhand for essential on-the-job learning, I was left to navigate tasks independently. This absence of mentorship has resulted in a notable gap in my understanding of crucial safety procedures.
More alarmingly, I suffered a severe injury due to exposure to an unlabelled chemical referred to as “carbon remover.” The lack of proper labelling and informed usage resulted in severe eye burns. This incident raises concerns about the company’s safety protocols for handling hazardous substances.
 I also observed unsatisfactory conditions on board, particularly regarding cleanliness. Coupled with the lack of training, this paints a concerning picture of the overall working environment.â
CHIRP Comment
CHIRP raised the reporter’s concerns with the Flag State Authority, who are investigating the claims. The ISM Code implicitly requires familiarisation and training (6.3, 6.5).
This must be done to identify all hazards and reduce the associated risks to avoid significant safety incidents on board the vessel.
Key Issues relating to this report
Capability- The company’s management appears to lack the necessary resource capability to ensure that the crew employed is provided with basic safety familiarisation. Does this situation, as described, apply to you? If so, please get in touch with CHIRP.
Teamwork- According to the reporter, more cooperation is needed to help new joiners in the industry. Does your company operate a mentoring system for new joiners or have aâ buddyâ system?
Culture- The company’s management needs to demonstrate a safety culture. Taking on a contract to tow a damaged barge, which is not fit to be on the water, is a clear example of safety being given a very low priority.
-
M2211
–
Open hatches at seaOpen hatches at seaInitial Report
CHIRP received a report from a vessel at sea. They passed a handy-sized bulk carrier and observed a light within one of the cargo cranes, with two of its six hatches open. Â At the time, the observed vessel was proceeding at 7 knots in a busy shipping area.
The vessel’s AIS gave the vesselâs port of destination nearby.  While observing the action of the handy-size bulk carrier, the reporter noted that the vessel had changed course to seek shelter in the lee of a nearby island. It was nighttime, and the weather conditions were Beaufort 3, with a significant swell of 1.0 m and a chance of precipitation.
CHIRP Comment
It is crucial to underscore the high-risk nature of certain maritime operations. Opening hatch lids and operating cranes in a seaway present significant dangers and should be strongly discouraged. Additionally, working at night while the vessel is underway is unnecessary and should be avoided.
The decision to seek shelter in the lee of an island, as reported, indicates that the vessel may have taken this action due to an emergency.
Operating cranes and fully opening cargo hatch lids at sea can subject crane components, such as heel pins, slewing bearings, and sheaves and wires, to additional forces. Even under low swell conditions, the potential for synchronised motion with the sea and swell can lead to uncontrollable swinging movements of the grab, pose a severe threat, and risk damage to the hold, crane, and associated wires.
Cargo hatch lids are designed for operation in port or at sheltered anchorages. Attempting to open them at sea can result in substantial damage to the hydraulic rams controlling the hatch covers and potential misalignment issues.
Regarding navigation, the vessel must adhere to Collision Regulations while underway. Taking appropriate action to avoid collisions, such as altering course, can impact the dynamic forces acting on the vessel’s hull, cargo, cranes, and hatch lids. Ensuring strict compliance with safety guidelines and regulations is essential for mitigating risks and ensuring the crew’s well-being and the vessel’s integrity.
Key Issues relating to this report
Situational Awareness- The consequences of carrying out operations at sea must be understood. This is a last resort and requires managers’ input to mitigate the risks.
Alerting- If cargo is shifting, affecting the shipâs stability, then help is required from the nearest coastguard station, and a port of refuge must be sought. Management must be informed.