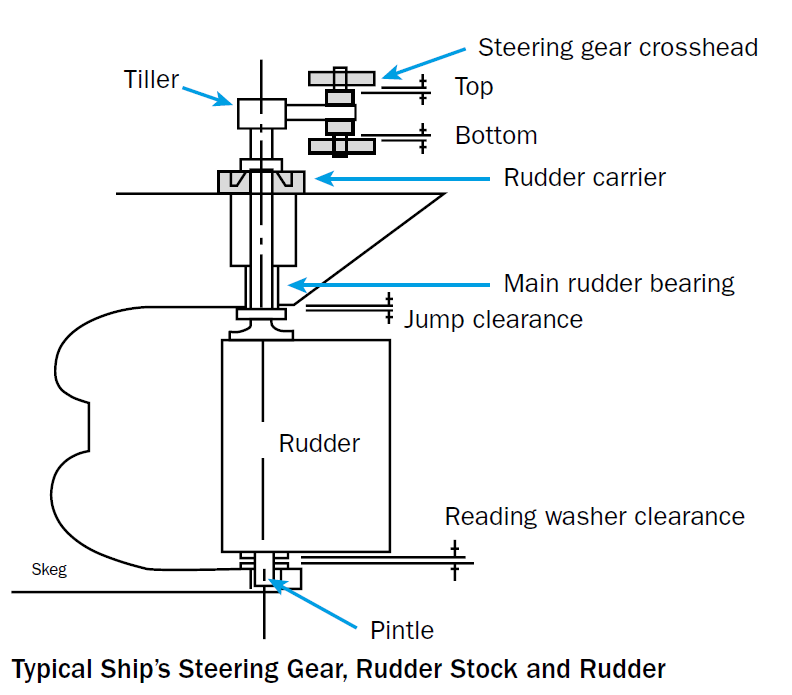
Rudder angle discrepancies - Rudder angle discrepancies
Initial Report
OUTLINE:
A report describing a vessel which was apparently experiencing excessive port helm.
What the Reporter told us:
As part of my duties as a pilot, I was required to shift a vessel from one berth to another. During the operation, I noticed that she was carrying an excessive amount of port helm, which I estimated to be in the region of 5 to 10 degrees. I pointed this out to the bridge team and on berthing, advised the master to compare the steering gear rudder angle against the corresponding rudder angle indicator display. However, when the vessel sailed outbound, the attending pilot observed that the situation had not much improved.
Recently, the same vessel returned to our port. Whilst inbound, the attending pilot again observed the same phenomenon. This made handling the vessel challenging, and as a result this discrepancy was formally reported to the local authorities.
Last night I sailed the vessel. Prior to departure, I discussed the issue with the master, and I insisted on witnessing the testing of the steering gear. An officer conducted the appropriate tests, and all was found to be in order.
However, the outward passage required a tug to be made fast on the centre-lead aft, and so I briefed the tug master that I would be conducting checks between the bridge rudder angle indicator and the actual angle of rudder observed by the tug master. Throughout the passage, about 50mm of rudder was visible above the waterline and any apparent discrepancies could be observed by the tug master.
On leaving the berth, it was immediately apparent that the vessel still carried a considerable amount of port helm. At various points during the passage, I was able to compare the vessel’s rudder angle indicator with corresponding observations from the tug master. These comparisons led me to conclude that the ship was carrying 8 to 9 degrees of port helm beyond what was indicated on the bridge.
The vessel is relatively new having been built in 2017, and there is no evidence of excessive vibration or load on the steering gear. The handling characteristics are however, outside the parameters that would be considered normal by the average ship handler and could be considered unsafe in certain circumstances. I feel the matter probably needs further investigation.
What the company told us:
CHIRP wrote to the company concerned, which conducted a full investigation. This investigation also included a detailed review of the VDR. This, along with the company analysis of the situation, did not suggest that there was any external force such as a grounding which might have caused the problem. The company requested the attendance of Class, and the following is an extract of the Class report detailing their findings and subsequent repair in drydock. This included damage to the hydraulic rams of the steering gear and the rudder stock. The company concluded that the damage to the steering system was most likely due to workmanship and/or material failure at the new building stage.
A bottom inspection of the vessel was carried out in drydock and there was no indication of any damage to the hull bottom paintwork. In addition, an inspection of the propeller blades and rudder revealed no deficiencies.
Inspection of the steering gear, rudder stock and the rudder blade were carried out in dry dock. Damage was noted as follows;
- Securing bolts for the guide bar bearing of the steering gear were found to be broken and the guide bar was found to be 20mm out of alignment.
- Cracks were found in the port side hydraulic cylinder ram, several foundation bolts were loose, and the ram was found to be slightly out of alignment.
- Several port side steering gear cylinder ram foundation bolts were loose.
- The upper rudder stock keyway was found to be slightly deformed, there was an offset of 25mm between the upper and lower bearings of the upper rudder stock when compared with the true centre line.
- A twist of the keyway amounting to approximately nine degrees was found between the upper and lower keyway when comparing this with the original centre line.
The Class report additionally gives full details of the repair that was carried out which included a thorough overhaul of the rudder carrier, repairs to the hydraulic rams and the steering gear foundations, heat treatment and straightening of the rudder stock, and machining out the deformations. The tiller keyway and carrier to the rudder stock were renewed. All of the work was carried out as per Class technical specifications.
The repairs were followed by magnetic particle testing, penetrant testing and ultrasonic testing of welding and machined repairs.
Upon completion of the repairs the rudder blade was given a swing test, and the steering gear with associated alarms were fully tested with satisfactory results. In addition, the attending surveyor witnessed sea trials of the steering gear whilst manoeuvring and these also were satisfactory.
Notes:
- The steering gear guide bar is a structure that guides the lateral movement of the hydraulic ram rods, such that the tiller movements correctly reflect the desired rudder angle of steering. The guide bar can run parallel to the steering gear crosshead or be fitted in place of the crosshead shown above. The guide bar bearing is the moving part of the mechanism that takes movement of the steering rams and transfers it to the tiller, while moving on the guide bar.
- The securing bolts for the guide bar bearing effectively connect the steering rams to the tiller.
- The rudder stock is the cylindrical steel bar (or tube) which connects the tiller to the It is of sufficient strength and moves in azimuth, to ensure that steering gear movements cause the corresponding direct movement of the rudder.
- The upper rudder stock keyway lies within the joint of the tiller to the rudder stock, with the key ensuring (if aligned correctly, and not damaged) that the tiller arm is correctly located, relative to rudder position, when the tiller arm is tightened down correctly onto the upper taper fit of the rudder stock.
- A typical steering gear has two hydraulic rams: one on the port side and one on the starboard side of the rudder stock, to provide power for the full range of rudder movement starboard to port.
CHIRP Comment
The Maritime Advisory Board agreed that this incident was a good example of a company following up and acting upon receipt of a report. Quite apart from the technicalities of the actual repair, the main focus of the Advisory Board comment, was that there was potential for a hazardous situation to develop, such as a grounding. In hindsight, it is easy to see that there was a problem even though the standard steering gear tests did not reveal any issues. It is also easy to note that for many defects (not
specifically this report but in general), if the problem is not detected immediately it can become the norm – “That’s the way it’s always been”. So the main lesson to come out of this report is: if something doesn’t feel right, then there may well be an issue – so REPORT IT! This lesson does not only apply to this vessel’s manoeuvring characteristics, but to any piece of equipment or any operation which does not appear to be functioning as you might expect it to.
Report Ends