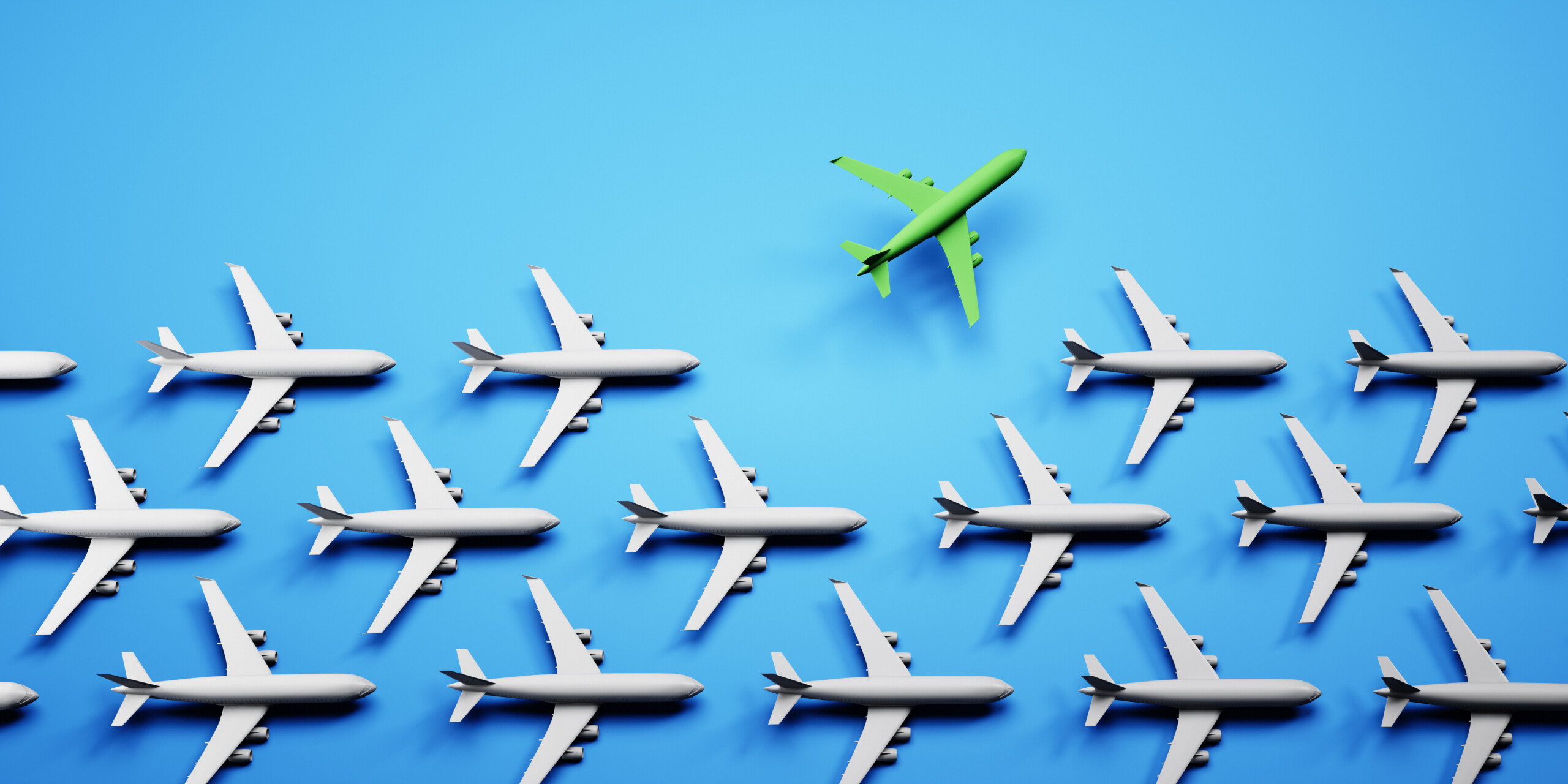
Making the difference
Contents
- Engineering Editorial
- I learnt about flying from that (ILAFFT)
- Comments on Previous FEEDBACKs
- FC5209/FC5212 - Commander’s discretion
- FC5222 - Extended FDP usage
- ENG720 - Lack of stand capacity resulting in aircraft repositioning
- FC5223/FC5229 - Punitive and unsafe sickness policy
- FC5221/FC5227/FC5228/FC5235/FC5236/FC5238 - Rostering and Duty Periods
It’s thanks to you and your reports that we can help to make change happen
In Memoriam: Peter Tait, Chief Executive of CHIRP 1995-2013.
Just prior to preparing this edition of Air Transport FEEDBACK, CHIRP learned that Peter Tait, the inaugural Chief Executive of the CHIRP Charity had sadly passed away. The CHIRP team would like to offer Peter’s family our deepest and most sincere condolences.
Although CHIRP had been in existence since 1982, it was Peter who placed us on a firm footing by transitioning CHIRP to a charitable trust over the period 1995-2013 and was responsible for setting up many of the processes and structures that still survive to this day. After a distinguished career that embraced RAF pilot, test pilot, display pilot and senior positions in commercial aviation and aerospace, Peter guided CHIRP as it expanded from being solely a conduit for Flight Crew/ATCO reporting to include Cabin Crew, Engineers, General Aviation and Maritime. His leadership of the CHIRP team and its contribution to aviation safety received international recognition in 2013 from the International Federation of Airworthiness who awarded CHIRP the Whittle Safety Award “In recognition of their contribution to aviation safety, through the development of a confidential reporting programme on human performance issues and concerns. An addition to formal reporting systems within the United Kingdom, the programme covers all aviation related sectors and disciplines.“
In remembering his contribution, I looked up the January 2013 edition of Air Transport FEEDBACK (Edition 105) where we publicised the International Federation of Airworthiness Whittle Safety Award to see what was topical at the time and what might have changed since. Imagine my chagrin to see, almost 10 years ago to the day, the title of his editorial as ‘Tiredness, Fatigue and Sickness’. Within, Peter commented on the regularity of reports that had been received about fatigue, offered some insights into contributory causes of fatigue, highlighted the contemporary CAP371 and scientific research from QinetiQ in their ‘SAFE’ Work/Rest model, lamented that some operators were pushing FTL/rostering boundaries, and posed the question about why an operator’s SMS/FRMS did not seek to establish why operating flight crew required to take controlled rest as a matter of course. He went on to comment that fatiguing rosters/schedules needed to be identified through the review of flight crew reports and stated ‘For this process to be effective it is essential that the review of fatigue reports is conducted in accordance with a clear Fatigue Reporting Policy that is published, reviewed and accepted by all stakeholders’. Well, plus ça change... Here we are at CHIRP still banging on about fatigue, rostering, absence management and the need for companies to listen to their crews about fatiguing duties and act on their fatigue reports!
In this edition of FEEDBACK you’ll see that I’ve linked together a number of reports with some common themes to at least show that we are dealing with them even if we can’t print them individually due to confidentiality concerns. Use of commander’s discretion, sickness policy, and rostering & duty periods are presented in this manner, all of which have been the subject of considerable interaction with the CAA and individual airlines in the recent past. We sometimes aren’t good at publicising this aspect of our role where we conduct detailed work in the background that can’t be published but it was particularly pleasing to see that our intervention on sickness policy at one airline has resulted in a positive outcome whereby the associated company’s policy has been changed. Our thanks go to all those who reported the issue to us, it’s unlikely that the change would have been made without your contribution, and this highlights the value of reporting. Hopefully we’ll have similar success stories with other issues in the coming months.
Steve Forward, Director Aviation
Engineering Editorial
Where is our industry now and what is in store for Engineering in the future? We all know that the current staff shortages are not going to disappear any time soon, and this has come just as the last of the “Post-War, Jet-Engine Generation” are retiring and who have not been replaced by apprentices for many years in anticipation of the inevitable need. Will expansion of the Ultra-Low Emission Zone (ULEZ) to include Heathrow, kill off a massive chunk of the local airline labour market? Will other major cities and their airports follow suit?
The result of all this inevitably means the cost of air travel is likely to increase, not just for the bucket-and-spade brigade but for business travel and air freight also. Continuing with the airline industry theme, putting business and first class to one side, budget travel can be a pretty unpleasant experience. Will a price increase to return operations to what they were lead to a more discerning public? Are passengers tiring of happily pursuing an initial ticket price only to log out at the end of booking a trip with the bitter taste of the final cost? Now we all have our little foil coffee pods at home, are we going to accept being charged for below average coffee on board anymore? Considering all airline classes, will this summer lose as many bags as last year? Ten security reports have been received by CHIRP in the last twelve months where staff have experienced concerns, and this should remind us that passengers can experience the same stressors at security as staff.
How does all this affect staff and, more importantly, engineers? CHIRP has received reports of contaminated potable water, cabin panels unsecure and some even missing! Is staff shortage leading to an acceptance of poor cabin cosmetics? If cosmetics are lower down the priority, is the safety and security of the cabin slipping?
Whilst operators review and hopefully improve their tourist and budget products, what has Engineering got to look forward to? Apart from a marked increase in remuneration, will we perhaps see the end, or a decrease in bonding staff until the cost of their type training has been recovered by length of service? There now are more than a couple supersonic transport aircraft in development, globally we are into double figures, and most of you will already know that United Airlines have said they will purchase fifteen of Boom’s Overture. We already have electric fixed- and rotary-wing development aircraft flying and plans for an all-electric BAe 146! Plus an increase in aircraft burning sustainable alternate fuels. What challenges will environmentally-friendly aircraft technology introduce for maintenance and servicing?
Apprentices are coming on-stream both within operators and MROs. A quick straw poll of seven operators and MROs (including corporate jets) indicated that some employers had sophisticated relationships with training organisations with impressive facilities who expect to train apprentices into three figures next year. Apart from apprentices, existing staff in some organisations are being given a formal opportunity to obtain A & B licences. Figures for the limited sample of organisations who responded stand at over 160 current and projected apprentices this year. The next few years of projected recruitment is assumed to be a similar number. Additionally, one operator with a large apprentice intake has a vehicle for ex-military staff to enter the civil aviation B licence world. Licenced Engineers will welcome the extra manpower with open arms, and the retired old post-war, jet-engine generation will wish all these young people the very best of luck.
Those of you that subscribe to CAA SkyWise will have seen that a consultation opened on the 8th March for Acceptable Means of Compliance & Guidance Material to UK Regulation (EU) No 1321/2014 SMS in Part-145 and Occurrence Reporting. This AMC & GM relates to Part-145, Part-M, Part 66, Part-CAMO and Part-CAO of UK Regulation (EU) No 1321/2014. If and when you are mentoring any of these new apprentices coming on stream, it is important to teach them the correct terminology. This AMC (in the Part 145 section), includes all the SMS phraseology that we have started to notice appearing in the last couple of years. For example, Continuation Training (Company & A/C type) and Human Factors refresher, are both part of Recurrent Safety Training. Occurrence Reporting is termed Safety Reporting. Quality Managers have gone the way of the Chief Inspectors before them. Compliance Monitoring Manager and Safety Manager are the latest concepts. They could of course be one and the same person. Lastly, any engineering staff involved in the issue of Flight Crew Authorisations should know that the AMC allows issue to Pilots, not just Commanders. That’s enough Air Leg for one day but now we should all read the Part 66 and Continuing Airworthiness sections of the NPA. So much to look forward to.
Phil Young, Engineering Programme Manager
I learnt about flying from that (ILAFFT)
This edition’s ILAFFT is taken from NASA’s Aviation Safety Reporting System (ASRS) ‘CALLBACK’ Newsletter Issue 515, December 2022. The article provides a good illustration of the importance of prioritising tasks, adhering to good CRM principles and taking time to make a Threat and Error Management (TEM) assessment of the relative inexperience and recency of the Captain that was compounded by an early morning duty where both pilots were tired. Perhaps pressures to depart on time took over but pilots need to be scrupulous in prioritising any amendment of performance data – both pilots should have stopped what they were doing to cross-check this rather than carrying on with other tasks simultaneously. Finally, although undesirable, ground handling teams may have different procedures for the same activity with different airlines and so its important to avoid any confusion by making sure that everyone understands what is required, and who’s doing what, at all times rather than assuming that everyone knows what’s going on.
“During pushback, the new ATIS stated conditions codes 5,5,5 and 100% wet for our departure runway. The performance data indicated dry conditions, so I contacted Operations during pushback to have them change the condition code to wet. I also started the Number 1 Engine, then requested new performance data through ACARS. As the ground crew stopped the pushback, the new performance data printed out, and I began inputting the data into the FMS. Simultaneously, the Captain conducted a control check as I monitored and called, “Flaps 2, taxi,” to begin movement. I looked at the EICAS and verified steering was disengaged and the flaps were set to 2. I looked up and didn’t see any ground crews. I then said, “Flaps set, steering engaged.” The Captain then began to taxi forward. That’s when I noticed the tug and ground crews directly under the airplane walking back. I immediately yelled, “STOP, STOP, STOP,” and applied brakes. The aircraft moved forward about 3 to 5 feet before coming to a complete stop with equipment and personnel directly under the aircraft. The Captain acknowledged and set the parking brake. No ground personnel or equipment contacted the airplane. We then received a salute from ground personnel as they departed the area of operations. The Captain and I discussed the situation and continued the rest of the flight without incident.
This event occurred early in the morning when both crew members were tired. Airfield conditions called for new performance data which caused a slight distraction for both crew members. The Captain has just over 80 hours as Pilot in Command (PIC) following a long break from the Company. Distraction with the performance data, inexperience, and lack of situational awareness caused the Captain to lose focus and forget to wait for ground personnel to leave the area before conducting the control check and calling for taxi. As the First Officer, I should have been more situationally aware of what the Captain was doing and of the location of ground personnel.”
We need your ILAFFT stories! The value of ILAFFT is that it provides insights from those who have been there, done it, and have lessons for all of us to learn. If you have any anecdotes or amusing ‘there I was…’ stories then please do share them with us so that we can pass on the messages and inform others (ideally in a light-hearted and engaging manner). Send any interesting tales to mail@chirp.co.uk and put ILAFFT in the subject header – we promise full confidentiality to protect the innocent (and not so innocent!).
Comments on Previous FEEDBACKs
Comment No1 – Words matter
CHIRP always welcomes feedback from readers and we strive to make necessary improvements and address issues brought to our attention. In our introductory comments in Air Transport FEEDBACK Ed 145 Report No5 (ENG723 – Differences in corporate risk taking and application of the MEL) we unintentionally inferred that trying to outwit an aircraft with work-arounds was a criticism afforded to this particular report that described a protracted fault-finding process where Company Base Engineers were attempting to guide non-Company engineers at a remote location. The CHIRP Comment was intended to be a generic caution but those involved in this incident were unhappy with this conflation and so we unreservedly apologise for giving the impression that they were being unprofessional in any way. On the contrary, CHIRP is aware of reduced staffing levels in Base Engineering at the time, and it was commendable under such circumstances that they also stepped in for Flight Operations in communicating with the flight crew.
Comment No2 – V1 callouts
I have just read the article concerning automated V1 callouts in Report No7 of Air Transport FEEDBACK Ed 145 (FC5206). While I cannot disagree with the views expressed by either the company or CHIRP, an essential element of the author’s concern regarding automated callouts was missed: if an aircraft has automated V1 callouts, should the flight crew rely on them completely or should the flight crew back them up?
A point for consideration is that flight crew awareness of V1 is essential during this critical phase of flight. Having had to reject take-off on more than one occasion, I can attest to the fact that the startle [surprise] effect is great and that an automatic ‘muscle-memory’ response is required when the aircraft is close to V1. I would therefore argue that not only should the flight crew brief V1, but one of the flight crew should also call it, regardless of the automatic call. In this way, not only is the numerical value of the V1 reinforced, but also its importance as a decision point. The risk is that, in relying on the automated call-out without any active participation, the automatic V1 call becomes just another event that happens during every normal take-off, as opposed to a point of change in flight crew response to a failure condition.
CHIRP Response: In our original comment the point was made within our penultimate sentence “…and non-handling pilots should be monitoring speeds such that they are prepared to make check-point calls if the aircraft does not for some reason…” Whether they make such calls anyway even if the aircraft does have an auto-call system as a mitigation for any potential failure is something that should be covered in company SOPs; although we recognise the value of this as a fail-safe approach, we demure from making any specific recommendations in this respect so that we don’t conflict with actual company policies and thereby potentially cause confusion.
Comment No3 – New flight planning system woes
Regarding Report No6 ‘New flight planning system woes’ (FC5203) in Air Transport FEEDBACK Ed 145. This issue [introducing new systems without comprehensive user interaction or training] is so commonplace in all areas of business it is embarrassing. Many years ago, I commenced study for a BSc Software Engineering degree. One of the first books I was advised to buy was Structured System Analysis & Design Methodology known as SSADM. Rule 1 of SSADM – when developing any new software system: TALK TO THE END USERS! Not the management, not the budget holder, not the CEO! The actual end users, i.e. the people who will be using the system on a day-to-day basis. From personal experience, how many companies allow developers to do this? ZERO! Therein lies the problem, and until developers are given free access to end users before they compile the system, the problem will not stop. We will keep being supplied what are essentially beta versions of the final product, which need patch after patch as developers fire-fight their way through problems. And one final point, just for management, it costs more doing it this way!!
CHIRP Response: Acknowledging that there will be differences in what management might see as critical (or affordable given that budgets are not limitless) and the desires and perceptions of users, the development of any such system should ideally involve end-users. This should not just be selected end-users with a vested interest or who have participated in the development, but fresh end-users exposed to the system without prior involvement so that they can give their unprejudiced experiences. This is especially important when third-party or ‘off-the-shelf’ software developers are involved in the development who, although they may well have their own experiences and a company brief to draw on, will not be steeped in the way a particular company operates or the nuances of their actual operations.
Comment No4 – Change management
I read this month’s [Air Transport FEEDBACK Ed 145] editorial about “Change? It’s a question of management” with great interest. It is interesting to understand the ICAO view about how change should be managed, and the Safety Management Manual about managing change is a great idea for best practice. However, to manage change going forward it is important we acknowledge mistakes made in the past, otherwise we keep making the same mistakes. This is the basic principle in the reporting and Just Culture that CHIRP is based upon.
CHIRP Response: As the commentator states, conducting a thorough review of circumstances, procedures and resources that were in place prior to a change is an important element of the change management process so that previous mistakes or sub-optimal elements are identified and associated lessons learned for better future structures and procedures. Within this, it can be difficult for those who are a part of the previous iteration to recognise deficiencies because they may themselves be a part of the problem or have ownership of the previous solution. As the commentator in Comment No3 states, when designing new systems or processes then talking to end users can be invaluable in understanding not just what the new system should look like but also what may have been wrong with the old system. That way, an informed view about what did or didn’t work before can inform the design of the new system or processes so that the same problems are avoided. Ultimately, change is something best done ‘with people’, not ‘to people’.
Reports
FC5209/FC5212 - Commander’s discretion
Initial Report
The CHIRP comment below refers to a number of reports about commander’s discretion.
CHIRP Comment
CHIRP has received increasing numbers of reports in recent months about the use of commander’s discretion and the perception that it is being programmed in to some rosters in order to resolve crewing problems. The majority of these reports are not publishable in isolation because the associated details make the reporters identifiable. However, CHIRP has represented these reports to the CAA in aggregate and has asked that they consider both reviewing the specific companies’ policies on discretion and the reality of actual current rosters. As a result, the CAA have focused some of their oversight activities for particular airlines in this area and have commented that there needs to be a better understanding of discretion within the industry overall. In recognising this, the CAA hope to publish an information note in the coming months to give more detailed guidance and advice to individuals on what discretion is and the rules for its use.
The use of commander’s discretion is not a safety issue in itself provided it is managed properly. Importantly, it should not be used on a planned basis but is intended to be employed for those unplanned and unforeseen circumstances and delays that occur during a duty and which would take the crew beyond the normal FDP limit. Crews should not be arriving at the report point to find the operator relying on the Commander’s use of discretion to conduct the duty – if unforeseen circumstances arise prior to ‘report’ then the reporting time should have been delayed instead when feasible. ORO.FTL.205 Flight Duty Period (FDP) (f) states the rules for the use of commander’s discretion in relation to FDP (extract shown) but, in stating that its use is for unforeseen circumstances which start at or after the reporting time, the problem is that there’s no real definition of what an unforeseen circumstance might be and so this is potentially a grey area.
ORO.FTL.205 Flight Duty Period (FDP)
(f) Unforeseen circumstances in flight operations — commander’s discretion
(1) The conditions to modify the limits on flight duty, duty and rest periods by the commander in the case of unforeseen circumstances in flight operations, which start at or after the reporting time, shall comply with the following:
(i) the maximum daily FDP which results after applying points (b) and (e) of point ORO.FTL.205 or point ORO.FTL.220 may not be increased by more than 2 hours unless the flight crew has been augmented, in which case the maximum flight duty period may be increased by not more than 3 hours;
(ii) if on the final sector within an FDP the allowed increase is exceeded because of unforeseen circumstances after take-off, the flight may continue to the planned destination or alternate aerodrome; and
(iii) the rest period following the FDP may be reduced but can never be less than 10 hours.
(2) In case of unforeseen circumstances which could lead to severe fatigue, the commander shall reduce the actual flight duty period and/or increase the rest period in order to eliminate any detrimental effect on flight safety.
(3) The commander shall consult all crew members on their alertness levels before deciding the modifications under subparagraphs 1 and 2.
(4) The commander shall submit a report to the operator when an FDP is increased or a rest period is reduced at his or her discretion.
(5) Where the increase of an FDP or reduction of a rest period exceeds 1 hour, a copy of the report, to which the operator shall add its comments, shall be sent by the operator to the CAA not later than 28 days after the event.
(6) The operator shall implement a non-punitive process for the use of the discretion described under this provision and shall describe it in the operations manual.
AMC1 ORO.FTL.205(f) Flight Duty Period (FDP) gives some further guidance by recognising the shared responsibility of management, flight and cabin crew in managing ‘unforeseen circumstances’, and noting that the use of commander’s discretion should be exceptional and should be avoided at home base and/or company hubs:
UNFORESEEN CIRCUMSTANCES IN ACTUAL FLIGHT OPERATIONS — COMMANDER’S DISCRETION
(a) As general guidance when developing a commander’s discretion policy, the operator should take into consideration the shared responsibility of management, flight and cabin crew in the case of unforeseen circumstances. The exercise of commander’s discretion should be considered exceptional and should be avoided at home base and/or company hubs where standby or reserve crew members should be available. Operators should asses on a regular basis the series of pairings where commander’s discretion has been exercised in order to be aware of possible inconsistencies in their rostering.
Overall then, the management of unforeseen circumstances during flight operations is a shared responsibility between operations management, flight and cabin crew, with the Commander – exercising his/her overall responsibility for the safety of the flight – as the final arbiter of any decisions. Therefore, in the case of unforeseen circumstances, and at his/her sole discretion, the Commander may extend the Flight Duty Period providing he/she considers that the safety of the flight will not be adversely affected by that extension. The Commander may also use his/her discretion to reduce a rest period (the rest period following an FDP may be reduced, but never below 10 hours). In exercising discretion, the Commander must ensure that, at all times prior to take-off, there is a realistic plan to remain within the Maximum Allowable FDP (including commander’s discretion). It is recognised that after take-off there may be unforeseen circumstances that could cause a minor exceedance of the Maximum Allowable FDP and, in such circumstances, the Commander must ensure that continued safe operation is prioritised over the need to stay within the Maximum Allowable FDP. Finally, although the crew must be consulted as to their alertness levels before commander’s discretion is employed, discretion is the commander’s to use or not and it is for them alone to decide on whether or not to invoke it rather than being a collective agreement by the entire crew.
Key Issues relating to this report
FC5222 - Extended FDP usage
Initial Report
Compared to previous years, the latter half of this summer has seen a dramatic increase in [Airline] of the number of extended FDP sectors which are being rostered for destinations that have always been well within normal FDP range. Given the disruption experienced earlier in the summer, with a number of night stops and discretion reports, the cynic in me says that the use of extended FDP is simply to mask the real issues and prevent reporting of discretion to the CAA. Anecdotally, I’ve heard that the reason for the increased use of extended FDP is because the CAA has concerns of the number of discretion reports being produced over this summer by the company!
CHIRP Comment
CHIRP passed on our concerns about the use of extended FDP in this way to the CAA and they engaged with the company. However, due to commercial considerations, the CAA do not pass on to CHIRP explicit details of follow-on associated discussions or data about specific concerns such as this other than to confirm that oversight activity has been conducted.
More generally, extended FDP allows the maximum basic Flight Duty Period for acclimatised crew members to be increased without the use of in-flight rest – this equates to an additional hour being applied to the basic FDP. Basic FDP may be extended not more than twice in any 7 consecutive days and must include either a pre- and post-flight rest extension of 2 hours, or a post-flight rest increase of 4 hours. Extended FDP must be planned in advance. If commander’s discretion is then applied to an extended FDP, then the maximum FDP from the basic FDP table is used to calculate the limits of discretion as shown in ORO.FTL.205 Flight Duty Period (FDP) (d) & (e)shown below.
ORO.FTL.205 Flight Duty Period (FDP)
(d) Maximum daily FDP for acclimatised crew members with the use of extensions without in-flight rest.
(1) The maximum daily FDP may be extended by up to 1 hour not more than twice in any 7 consecutive days. In that case:
(i) the minimum pre-flight and post-flight rest periods shall be increased by 2 hours; or
(ii) the post-flight rest period shall be increased by 4 hours.
(2) When extensions are used for consecutive FDPs, the additional pre- and post-flight rest between the two extended FDPs required under subparagraph 1 shall be provided consecutively.
(3) The use of the extension shall be planned in advance, and shall be limited to a maximum of:
(i) 5 sectors when the WOCL is not encroached; or
(ii) 4 sectors, when the WOCL is encroached by 2 hours or less; or
(iii) 2 sectors, when the WOCL is encroached by more than 2 hours.
(4) Extension of the maximum basic daily FDP without in-flight rest shall not be combined with extensions due to in-flight rest or split duty in the same duty period.
(5) Flight time specification schemes shall specify the limits for extensions of the maximum basic daily FDP in accordance with the certification specifications applicable to the type of operation, taking into account:
(i) the number of sectors flown; and
(ii) WOCL encroachment.
(e) Maximum daily FDP with the use of extensions due to in-flight rest Flight time specification schemes shall specify the conditions for extensions of the maximum basic daily FDP with in-flight rest in accordance with the certification specifications applicable to the type of operation, taking into account:
(i) the number of sectors flown;
(ii) the minimum in-flight rest allocated to each crew member;
(iii) the type of in-flight rest facilities; and
(iv) the augmentation of the basic flight crew.
But there are penalties to a company for using extended FDP rather than commander’s discretion due to the additional rest periods required. The reporter’s comments that this particular company were using extended FDPs to avoid having to report discretion (which is a mandatory reporting requirement to the CAA for periods exceeding 1 hour) was therefore of interest. Asked what the CAA does with discretion reports, the CAA commented that if the actual operation of a route exceeds the maximum FTL for 33% of the times that a route is flown in a scheduled season then they require the operator to make changes to the route structure (ORO.FTL.110 (j) refers).
Key Issues relating to this report
ENG720 - Lack of stand capacity resulting in aircraft repositioning
Initial Report
At [Airport] stand allocation constraints require the movement of aircraft from stands adjacent to the terminal to remote stands to facilitate a smooth operation. These capacity constraints regularly require the movement of 30 plus aircraft at some point during the night. The usual challenges faced by engineers and mechanics to achieve the workload with the typical late arrivals and early departure that typifies summer operations is exacerbated by these movements. Whilst everybody at [Airport] has their part to play to achieve the airport’s smooth running, and I appreciate that the movements play a vital part in this, I would like to highlight the issues that this can cause on the line as an engineer.
This morning [Registration] landed at 0450, it was not on the pre-published tow-list that is sent ahead of time. As a consequence, we started a work-pack around 0500, with the intention to finish at 0700 when the shift ends. Our workload consisted of some routine tasks, a crew oxygen bottle change, and two small inbound defects. Our work was definitely achievable with the number of engineers assigned and the time available, so we began straight away. With the oxygen bottle removed, and CB’s pulled in the flight deck, at around 0530, the [Handling Agent] tow-team arrived and informed us that they had to tow this aircraft. I spoke with the team leader and informed him that we were midway through maintenance and would be around 45 minutes, I asked if it would be possible to return in an hour when we were done. The tow-team said they would speak to the airport and advise if this was possible. Unfortunately, after the phone call the tow-team informed us that the airport required that stand immediately and that the aircraft had to be made towable immediately. The tow-team went onboard, fitted MLG locks and removed the airbridge without consultation and stood in position with the tug at the nose gear right next to us whilst we hurriedly fitted the new bottle. This action compounded the pressure we felt to complete maintenance quickly, and we opted to leave the O2 bottle secured with unions connected, but to leak-check, test and complete paperwork after the tow had been completed. We could not get onboard to test as the airbridge had already been removed.
This situation was far from ideal, as I am acutely aware that being pressurised to complete a job quickly coupled with the distraction of the aircraft being towed with maintenance incomplete makes maintenance errors more likely but it was my preferred option. The alternative was to have a visit from airside operations with a reprimand for rendering the stand unusable without first notifying the airport and with the threat of having my airside pass being taken away (which in the past invariably happens to engineers who insist that they finish maintenance before the aircraft is towed). This is equally distracting and I did not want such a confrontation to happen. I therefore stopped midway through maintenance to facilitate the capacity request tow.
Whilst I appreciate the airport are under pressure to run a smooth operation, and that aircraft moves need to happen to facilitate that, the scale of the movements required due to capacity constraints (some aircraft even being towed twice in one night), coupled with the short downtime and poor relationship between engineers and airside operations adds to the likelihood of maintenance errors. I appreciate everyone is just trying to do their jobs the best they can, and I do understand that it must be frustrating if engineers are preventing aircraft movements happening when the airport would like, but ultimately safety must come before smooth operations. I personally do not think asking to be left undistracted for an hour to complete maintenance to be an unreasonable request.
I know that these issues have been escalated to management level and discussed between [Operator] and [Airport Ops]. Unfortunately, I believe there is a bit of a disagreement, and the position of [Airport Ops] to be very unhelpful. In their view engineers should not be disabling any aircraft by doing maintenance before they are towed. Unfortunately, this does not work for engineers, because the tow-lists are provisional, may not include all the required tows, and times are very unreliable. I cannot justify waiting for a tow that could be in a few hours before commencing my work, aircraft downtime is too limited. The aircraft I reported was not on the tow-list, and as such there was no easy way of knowing if and when the aircraft would require a tow. I am aware that some of my colleagues have started maintenance on an aircraft, returned to the office to pick up tooling and a bite to eat and returned to find a different aircraft on stand. Had they not been so observant it is quite feasible they could continue work on the wrong aircraft.
Comments
Operators Comment (Precis)
CHIRP Comment
It’s a fine balance between the prioritisation of stand use versus maintenance activities, and there are undesirable consequences from both disrupted maintenance activities and stands backing up for aircraft landing. We are all very aware of the hazards involved with interruptions to the continuity of work in progress, and the prospect of returning to a stand and not realising a different registration had replaced your task aircraft could unleash a catalogue of perilous safety issues for both aircraft.
The operator carried out a comprehensive internal investigation and met with (and conference-called) both the Airport and Handling Agents who were also proactive and sympathetic to the problems reported and the dangers of interruptions to aircraft maintenance. It is disappointing that the operator’s Safety Management System had not identified this problem previously, and perhaps there is a case for mitigation within Maintenance Planning. Improved communications will hopefully correct this situation, and continued reporting by engineering staff will hopefully assist the operator in ensuring this issue will improve.
It is all too easy to commence a shift and enter into battle with any party that stands in one’s way but if this becomes commonplace then the big picture of Human Factors issues can fall by the wayside; an interruption that could have been mitigated against becomes a stressor increasing the chances of further error. Ultimately, the solution revolves around planning and communication between teams. This can be made more difficult depending on how many agencies are involved in an activity and so effective communications at the seams between organisations needs to be consciously addressed as part of task planning and execution in such situations.
Key Issues relating to this report
FC5223/FC5229 - Punitive and unsafe sickness policy
Initial Report
The CHIRP Comments below refer to a number of reports about sickness policy.
CHIRP Comment
An airline recently changed its sickness policy for both flight and cabin crew such that if they reported sick even for one day their salary was reduced by salary/260 for each day of sickness (there being 260 days reckoned available for work in any 12-month period). This was compounded by the fact that the salary represented approximately 50% of their pay for the lost day with the other element (variable pay) also being lost completely. As a result, crews were being induced to fly when they were unfit to do so due to financial pressures despite legally being required not to operate. For periods of sickness up to 3 days, no pay was received; Statutory Sick Pay (£19.87 per day) was then being paid from the 4th day onwards.
CHIRP received a number of reports about this issue which we could not publish due to problems disidentifying the reporters. As a result, we engaged with the CAA to ask them to review the company’s absence policies and their suitability in respect of sickness payments. We’re pleased to report that, following this engagement with the company, the Airline have since changed these financial arrangements within their absence management policy. The safety implications of the previous financial measures were obvious and we are grateful to the CAA for taking up the case on our behalf, and for the company in subsequently understanding the dilemma to which it was placing its workforce. This absolutely highlights the value of reporting; without having done so it is unlikely that anything would have changed until circumstances conspired to bring about a serious incident involving someone who was unfit to operate.
Key Issues relating to this report
FC5221/FC5227/FC5228/FC5235/FC5236/FC5238 - Rostering and Duty Periods
Initial Report
The CHIRP Comments below refer to a number of reports about rostering and duty periods.
CHIRP Comment
In a similar manner to the reporting of absence management and use of discretion, reports that CHIRP receives about rostering and duty periods necessarily contain route and personal information that mean we are unable to approach companies directly about specifics due to the fact that reporters would be easily identifiable. Our only recourse is to engage with companies where possible with aggregated information from a number of reports, and to ask the CAA for their perspective on a company’s operations. Post-COVID resourcing pressures have resulted in a number of changes to rostering practices wherein it is clear to CHIRP that some companies are approaching FTL maximums much more frequently than hitherto. CHIRP’s view on FTL maxima has consistently been that they should be approached only infrequently and in a managed manner – as with any system, running resources at the red line for prolonged periods is a sure way of increasing risks that should not be contemplated without considerable caution; the response of ‘it’s legal’ is not a mature way of managing fatigue and FTLs.
Although we cannot claim any specific successes ourselves in resolving these issues, CHIRP regularly engages with the CAA and they have conducted specific oversight activities based at least partially on our inputs in association with their own intelligence about what is going on. There have been changes made to some rostering practices as a result, but we continue to engage about other aspects of rostering that appear to be ‘legal’ in pure FTL terms but not sensible from a Human Factors perspective as far as we are concerned. Part of CHIRP’s concerns lie within the sometimes black-and-white outcomes and temptations to rely on the certitudes of ‘sleep science’. There has to be some structured and systematic basis for constructing rosters but, whereas concepts such as WOCL and circadian rhythms provide a good basis for understanding the background factors affecting sleep, we’re not yet convinced that ‘sleep science’ is robustly able to deal with the multiple idiosyncrasies of individual people, circumstances or route structures to predict specific outcomes.
Example comments received by CHIRP are:
“Pre-covid as a pilot I rarely felt the need to nap whilst at the controls. Now I feel it’s a necessity to do it on every night sector to minimise micro-napping and falling asleep at the controls at critical stages of flight.”
“No matter what studies these so proclaimed sleep specialists and scientists claim to have done and what monitoring devices they use in their studies, they have not done the job first hand. And if they have, it has not been for a prolonged period of months, or years. Yet airlines seem to think it’s ok to roster to the limits. There is a complete lack of understanding. They are called Flight Time Limitations. They are not called Flight Time Targets.”
“Fatiguing flight outbound. More time spent in the aircraft than resting down route. When I arrived at the hotel I needed to rest for a few hours as already exhausted. This then impacts quality of sleep before 5am body clock wakeup for return sector.”
“High levels of fatigue experienced in cruise needing attempts at multiple periods of controlled recovery rest. Too fatigued on landing to travel away from the airport without a proper full rest so booked hotel, at my own expense, as a self-imposed fatigue mitigation.”
“Fatigue is clearly an issue at [Airline], but the company discourage fatigue forms, penalise absence and crewing are clearly manipulating rest periods/duty times to make things legal. There is definitely a safety issue here. Last night I had to get the First Officer to fly both sectors because I was so drunk on tiredness.”
It’s vital that crews continue to submit fatigue reports when appropriate, even if they suspect they are not being sufficiently acted upon, so that actual data can be used to modify theoretical scientific assumptions. Thankfully, many companies are receptive to such reports as they evolve their rosters, and the development of associated fatigue risk management regimes hinges on an understanding gained from these about the stresses and rest opportunities pertaining to each duty and individual. Regulations for rostering/scheduling are many and complex, not least in respect of FTL requirements. Overarching requirements for operators to “…allocate duty patterns which avoid practices that cause a serious disruption of an established sleep/work pattern, such as alternating day/night duties” are stated within ORO.FTL.110(e) Operator responsibilities, whilst the associated AMC1 ORO.FTL.110 Operator responsibilities defines the underpinning scheduling requirements that state:
SCHEDULING
(a) Scheduling has an important impact on a crew member’s ability to sleep and to maintain a proper level of alertness. When developing a workable roster, the operator should strike a fair balance between the commercial needs and the capacity of individual crew members to work effectively. Rosters should be developed in such a way that they distribute the amount of work evenly among those that are involved.
(b) Schedules should allow for flights to be completed within the maximum permitted flight duty period and flight rosters should take into account the time needed for pre-flight duties, taxiing, the flight- and turnaround times. Other factors to be considered when planning duty periods should include:
(1) the allocation of work patterns which avoid undesirable practices such as alternating day/night duties, alternating eastward-westward or westward-eastward time zone transitions, positioning of crew members so that a serious disruption of established sleep/work patterns occurs;
(2) scheduling sufficient rest periods especially after long flights crossing many time zones; and
(3) preparation of duty rosters sufficiently in advance with planning of recurrent extended recovery rest periods and notification of the crew members well in advance to plan adequate pre-duty rest.
Alternating day/night duties, alternating eastward-westward or westward-eastward time zone transitions and the scheduling of sufficient rest periods especially after long flights crossing many time zones get specific mentions in ORO.FTL.110, but there are many more other factors that affect the quality of in-flight rest and the ability to sleep both down route and when home. Humans are not machines that can be turned off at the flick of a switch, the ability to fall asleep is something that varies from individual to individual, and even for a specific individual depending on the context of their duties, pressures and stresses, personal circumstances and activity profile in the hours immediately prior to attempting to fall asleep. In our discussions with the CAA, they have indicated that they also recognise the limitations of some of the current fatigue management regulations. Now that UK is no longer tied to EU requirements, and subject to resources being allocated, they have a medium-term aspiration to look again at the fatigue regulations inherited from EASA and to tailor the UK FTL//FRMS document set to reflect better our specific perspectives and circumstances.