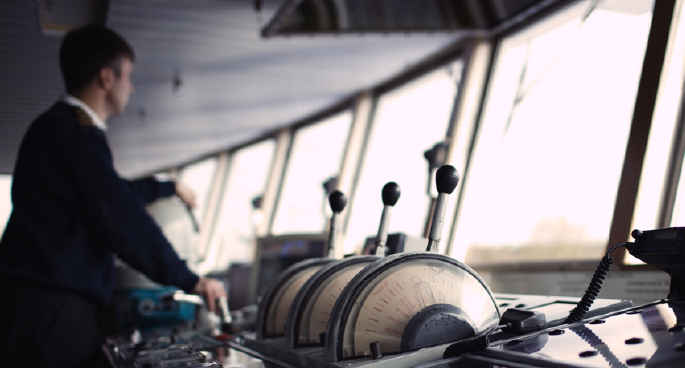
CHIRP Maritime – There For Everyone
Contents
- M2125 - No gas detection equipment carried on board
- M2124 - Lifting eyebolts failed while launching a Tender.
- M2127 - Inappropriate risk assessment
- M2128 - Permit to work checks not thoroughly completed
- M2126 - Anchoring Angst!
Welcome to the Summer edition of Superyacht FEEDBACK, the safety newsletter that explores topical safety issues based on your submitted reports.
In report M2124, CHIRP Maritime highlights the risks associated with mooring operations. The report emphasizes the importance of proper planning, communication, and coordination between the ship’s crew and the shore team to prevent accidents during mooring. Report M2125 focuses on the dangers of working aloft. It highlights the importance of adequate safety measures, such as safety harnesses and proper training for crew members, to prevent falls and injuries while working at height.
M2126 discusses the importance of proper maintenance and inspection of safety equipment, such as lifeboats and rescue boats. It stresses the need for regular inspections and maintenance to ensure the equipment is always in good condition and ready for use in an emergency. The issue of mental health in the maritime industry is addressed in report M2127. It highlights the pressures and stresses faced by seafarers and the need for support
systems to help manage these challenges. The report encourages the industry to prioritize mental health and well-being and provide access to resources such as counselling services.
Finally, report M2128 highlights the importance of effective communication between the bridge team and the engine room team. It emphasizes the need for clear and concise communication to avoid misunderstandings and prevent accidents. Don’t forget that CHIRP Maritime is there for everyone in the maritime community, at sea or ashore and we welcome reports from all roles and trades, not just deck, navigation or engineering but chefs, crew managers, housekeeping, stewards, surveyors, training staff, too!
Until the next edition – stay safe!!
Reports
M2125 - No gas detection equipment carried on board
Initial Report
Our reporter worked on a commercial yacht under 500gt where allegedly there were no enclosed spaces, even though there were compartments below decks that were not ventilated. No gas detection equipment was carried on board and it was impossible to determine whether bilge spaces, chain lockers, steering flats etc., were safe to enter or work in.
CHIRP Comment
This reporter is to be praised for raising this matter and for showing a high level of safety awareness. Enclosed spaces kill an average of 10 seafarers every year.
The definition of an enclosed space can be found in SOLAS Regulation XI-1/7 as well as The Code of Safe Working Practice (COSWP) chapter 15:
A space which is not designed for continuous worker occupancy and has either or both the following characteristics: limited openings for entry and exit and/or inadequate ventilation.
Enclosed spaces do exist on super yachts, and can include areas such as chain lockers, bunker tanks, paint lockers, battery lockers, peak tanks, cofferdams, sail lockers and void spaces. Arguably non-tank spaces are more dangerous as crews are less aware of the risks. Never assume that a space is not an enclosed space- always check!
If access to any of the above spaces is required, then proper entry procedures must be followed. These include a risk assessment (RA), a test of the atmosphere using properly calibrated portable atmosphere testing equipment and the completion of a permit to work (PtW). If the testing equipment is not on board, then entry must not be attempted. The testing equipment should be capable of testing and displaying the amounts of oxygen, carbon monoxide, hydrogen sulphide and flammable gases. Vessels which do not have properly approved and calibrated gas measuring equipment and portable gas-freeing fans should obtain them before any enclosed space entry is undertaken, and in any case the compartment should be thoroughly vented for several hours prior to entry.
Although there are some exemptions to the rules for carrying gas measuring equipment, CHIRP’s Superyacht Advisory Board were united in their belief that it should always be used, particularly as it is relatively cheap (many models cost less than $500 USD). The crew must also receive training in calibrating and using the equipment. Calibration can usually be carried out on board, although some models can only be calibrated ashore. The importance of proper recording of the maintenance of the equipment is essential and cannot be overstated.
Concerning gas-freeing fans, they should be sourced to ensure that the largest space can be thoroughly vented with enough force ventilation to ensure that no pockets of atmosphere with insufficient O2,, toxic and/or flammable gases remain. When sampling the atmosphere, always make sure that the sampling is representative of the space to be entered- several sample points must be obtained, often at different heights off the deck.
The Advisory Board lso recommended that the 2-monthly entry and rescue drills required by SOLAS should not only focus on the physical drill and the rescue but raise awareness during the drill of what constitutes an enclosed space. It is best practice to identify these spaces eg with signage or similar (We recommend “Enclosed space – no entry allowed until all entry RA and PtW requirements are met”)
Key Issues relating to this report
Culture- Underestimating or ignoring hazards are signs of a poor safety culture. In this incident there appears to have been no thought given to ensuring that enclosed spaces on the super yacht can be ventilated and tested for safe entry. The reporter has challenged this culture by raising this report, which is commendable.
Capability- Identifying enclosed spaces is not always easy; are you confident in your ability to do so?
Local practices– Owners are recommended to commission an external safety audit to ensure that hazards are correctly identified and that minimum safety management standards are being applied.
M2124 - Lifting eyebolts failed while launching a Tender.
Initial Report
Our reporter was part of a team launching the tender from the shell door opening in calm weather conditions. After checking the hoist arrangement and securing the forward and aft lifting arms, the tender was lifted off the chocks. Another crew member went around to lower the outboard side of the tender chocks. Once they were back inboard, the crane arms were extended, but when the tender was halfway out, the bow suddenly dropped to the deck and slid into the water. Meanwhile, the aft end of the tender hit the deckhead, sending ceiling panels flying.
The cause was a sheared eye bolt thread. No additional loading was introduced while lifting the tender until the point of failure. The eyebolt conditions appeared to be in good condition, although there was some uncertainty about when they were replaced last.
CHIRP Comment
Such incidents are not uncommon; and failure under load is often caused by inappropriate eyebolt design or weight-carrying capacity. When lifting, we naturally focus on the type and rating of the lifting strops used, but often the fixed lifting points are overlooked. Lifting eyebolts should have their capacity and test-date stamped on them or on a metal test certificate affixed immediately adjacent to them. Be sure to check your lifting arrangement for the tenders and work boats on your vessel!
This information will be available in the new building spec for the tender. The tender’s crane and lifting equipment should also have been subjected to a proof test, like commercial vessel lifeboats.
When eyebolts are replaced, it is important to replace them with the same specification as the original, and properly fixed back in position. Another contributing factor can be the angle that the eyebolts make with the lifting shackles. If the lifting eyebolt and lifting strops are not in alignment, a shear force is produced which can cause failure of the eyebolt/s.
This cautionary report reminds us all never to stand or pass under any suspended load, as failure can occur unexpectedly either with inadequate or poorly maintained lifting equipment.
Key Issues relating to this report
Overconfidence- Often there is an expectancy that the eyebolts will ‘just work’. Be aware of such single points of failure in a lifting rig and pay particular attention to these areas, such as deformation, pitting or wear and tear.
Capability– During our investigation we heard anecdotes from yacht crews that eyebolts were sometimes changed locally, with a different design e.g. to be less obtrusive. Given the criticality of the eyebolts for safe lifting, maintainers must ensure that the eyebolt specification is safe and meets the original design specification, which will have an additional safety margin for shock-loading lifting forces. If you’re not certain that the eyebolts on your vessel are ‘as originally designed’ then seek expert advice!
Local Practices– As the eyebolts were replaced, it is essential that the original equipment parts were replaced with the same specification eyebolts. Thoroughness in the procurement process is critical to ensure that the tender can be lifted each time safely. How thoroughly do you procure original spare parts? Does your management have a procurement policy?
M2127 - Inappropriate risk assessment
Initial Report
During a passage through a busy straight at night, the vessel started to vibrate heavily. Weather conditions were uncomfortable, with two-meter swells and high winds. The general alarm was sounded and the vessel stopped. The position was checked, with no apparent signs of grounding, as the vessel was in the deepest part of the straits. There was minimal traffic in the area.
When the engines were reengaged, significant vibrations were felt on the port side, indicating an object around the prop. While investigations were carried out in the engine room and the rest of the vessel, the engines could not be used to keep the vessel pointed into the weather, and she began rolling heavily.
The captain asked the deckhand/dive instructor if they could dive under the hull to carry out an external inspection. Despite the conditions, the deckhand- who was the only qualified diver- agreed. Preparations were made and all aft machinery was isolated. The bow thruster was used to keep the vessel head to wind. Lots of lighting gear was used, and a safety line with a quick release was attached to the solo diver who entered the water.
The pitching hull struck the diver several times and they quickly aborted the dive for safety reasons, but it took 10-15 minutes to recover the diver onto the swim platform because the vessel was moving so violently. Once onboard, the vessel continued its passage to harbour using the starboard engine only, where a large tree trunk was found stuck between the port shaft and the vessel’s hull.
CHIRP Comment
Many aspects of this report are disturbing. An objective risk assessment would have identified that the sea and weather conditions were out of limits to carry out diving operations safely. The safest option was to head back to port on a single engine, where an inspection could safely be carried out in daylight.
Although the deckhand held a recreational diving instructors’ licence, they were not a qualified commercial diver. Commercial diving requires a diving team in attendance so that a diver can be rescued if they get into difficulty. There was no back-up here; this was a clear demonstration of the ‘overconfidence effect’.
The ‘overconfidence effect’: where a person’s subjective judgement is greater than the objective accuracy of those judgements.
Finally, the captain should have recognised that the authority gradient between themselves and the deckhand placed unspoken pressure on the deckhand to agree to the task. No crew should feel pressured to carry out a task which is clearly unsafe and dangerous.
Key Issues relating to this report
Situational awareness (SA)- Intentionally isolating propulsion machinery and making the vessel ‘not under command’ in a busy strait at night and in poor weather demonstrates poor SA by the captain
Overconfidence- In seeking to employ a recreational diver on a commercial diving task outside of safe weather limits, the captain should have recognised their own overconfidence bias. This was poor judgement.
Pressure- The authority gradient pressurised the deckhand to dive in obviously dangerous conditions.
Teamwork- Did the crew feel empowered to challenge to the decision to undertake the dive, or was “group think” involved?
Capability– The diver was not qualified to undertake this task, nor were the crew capable of mounting an effective rescue operation.
M2128 - Permit to work checks not thoroughly completed
Initial Report
While at anchor, the chief officer went outboard to inspect the windows as part of a routine maintenance check. He wore the appropriate PPE in accordance with the requirements of the Permit to Work (PtW), a harness with an attached safety line, a lifejacket, and a helmet. After doing his buddy checks, he went outboard to inspect the windows.
He realised he was missing one carabiner and grabbed a quick-release shackle, which was used as the primary point for connecting to the vessel. A little while later, a deckhand found the chief officer swimming behind the boat. The chief officer reported that during the inspection, he had accidentally knocked the quick-release shackle, which released the safety line causing him to fall into the water.
CHIRP Comment
The chief officer was following the permit-to-work requirements and used a crew member (buddy) to ensure that the gear was being worn correctly in accordance with the PtW, which is commendable. However, picking up a quick-release shackle instead of a carabiner and using it as the main securing point created a single point of failure which inevitably led to the fall from height.
CHIRP stresses that working at height PPE should be kept separate from other lifting or securing gear. This gear should be stored in clean, secure compartments and regularly scrutinised for damaged.
The PtW requirements were not followed properly because anyone working at height must be fully supervised during the work. No other work activity should be undertaken which takes away that essential duty. It’s important to ensure that the crew are trained on the full requirements of the PtW system so that the full process is followed. In previous FEEDBACK editions, CHIRP has emphasised that when crew are working aloft a rescue plan must always be prepared as part of the risk assessment. Crew members who fall and are suspended by their safety harness must be rescued within 15 minutes to avoid serious injury or even death due to blood circulation being constricted.
Key Issues relating to this report
Communications– Clear communications must be provided to the crew who is spotting the person working aloft. When your crew work aloft, do you have crew spotters who know what to do if a person is suspended by the safety harness?
Distractions– Nothing should distract the person attending to the crew working aloft. Use additional crew who have been briefed about the work and the PtW if the spotter can only sometimes be there.
Teamwork- Work as a team and share what will happen with those assigned to the work. Making sure that the equipment that is going to be used for the job is correct and in good condition.
Pressure- the chief officer placed pressure on themselves to carry out the task with inappropriate equipment – a quick-release shackle is not a suitable replacement for a carabiner!
M2126 - Anchoring Angst!
Initial Report
The owner was unhappy with the anchorage location and wanted to move. The anchor was weighed, and the deckhand went into the chain locker to stow the cable. They wore ear defenders due to the noise of the cable in the chain locker.
The anchor was weighed to the water line and the vessel was relocated to the new anchorage position where the order was given to drop the anchor again.
The deckhand was still in the chain locker and was either not informed or did not hear that the anchor was about to be let go, and still had their hands on/near the chain as it dropped. Had they become entrapped, the consequences of this near-miss would most likely have been fatal.
CHIRP Comment
Poor communications were a significant factor in this incident, and situational awareness was lacking in the executive team: no crew member should ever be inside the chain locker when a cable is about to be lowered or dropped.
A chain hook or other wooden device must be used to flake out the cable to prevent it from piling up and stowing in the chain locker, and the crew member attending to this task must leave the locker once it is complete.
There appears to be a design issue with the chain locker: either the locker is too small to accommodate the cable pile when the anchor is stowed, or the spurling pipes are not adequately designed to allow the cable to self-stow. Design modifications should be considered to eliminate this unnecessary risk before the next docking.
Crew training should be provided on anchoring procedures and the risks outlined. The wearing of ear defenders is questionable when clear audible communications for anchoring operations are required, and a clear means of communications must be found.
Key Issues relating to this report
Design- The poor design of the anchor system created an unnecessary risk which required a crew member to manually flake the cable to prevent it from piling up. Redesigning the spurling pipe in the chain locker to allow the cable to self-stow and not pile up is highly recommended.
Communications- Communications failed, which created this potentially severe near miss.
Good operational safety relies on everyone knowing what is going on so that everyone can contribute to a safe operation. Before any anchoring operation, do you hold a toolbox meeting to discuss what will happen?
Situational Awareness- Nobody thought to check if the crew member was clear from the chain locker. The anchor was at the water line, ready to be let go, but nobody challenged whether the crew was clear of the chain locker. Why?