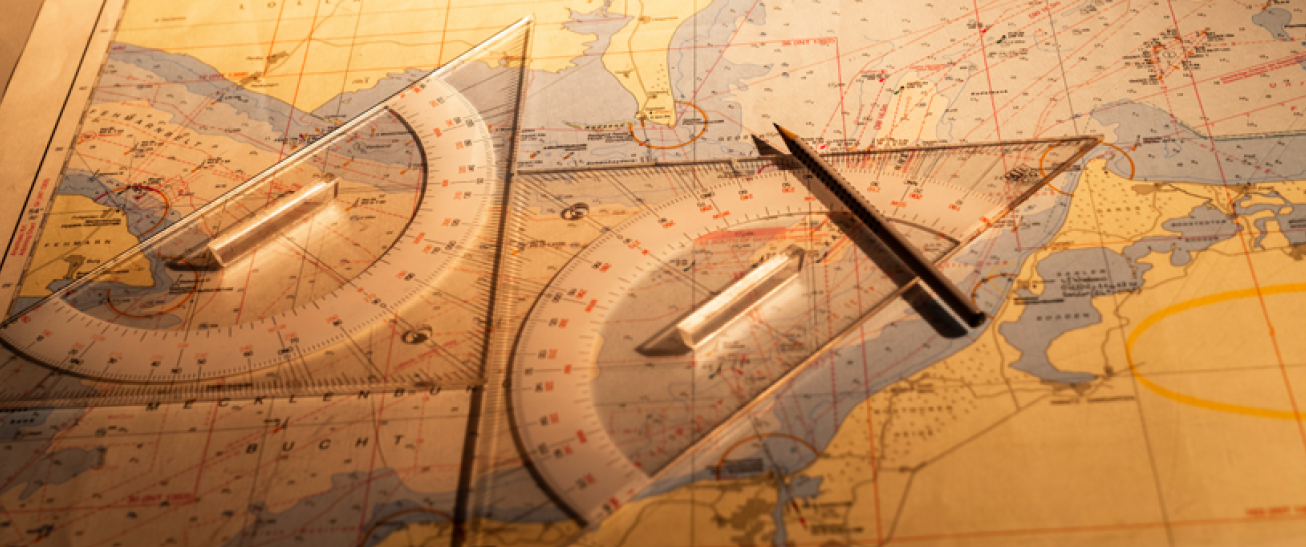
Plotting the course to safe waters
Contents
- M2140 - Allergic reactions
- M2137 - Personal Injury due to gangway malfunction
- M2136 - Capsize of a Dive Safari Vessel and Rescue of Tourists and Crew
- M2142 - Contact with ground lines while departing a repair berth
- M2138 - Personal Injury during mooring operations
- M2111 - Grounding and dismissal
The wide variety and dynamic nature of superyacht operations makes planning for every eventuality impossible, and we instead rely on the ‘guiding stars’ of a common goal, good communication, teamwork and a strong safety culture to frame our decision-making and actions. In doing so, we make certain assumptions: when we encounter deficiencies in the information available, we assume that our knowledge, experience and professionalism will compensate; every individual is suitably competent and experienced, and the equipment we use is well designed and fit-for-purpose. We may also assume that safety will be prioritised over commercial interests, and that this view is shared by owners, guests and leaders alike.
Recent incident reports received by CHIRP challenge each of these assumptions, which are addressed on the following pages. In our first report (M2111) we tackle the fallacy that ‘the boss is always right’ (they aren’t, because they’re human too!) and remind leaders that constructive questioning is not a challenge to their authority. Certainly, raising reasonable safety concerns are not grounds for dismissal!
Ensuring equipment is well designed and fit for purpose is the subject of reports M2136 and M2137, which explain why post-installation quality assurance so important, and why even non- engineers should question the lack of test certification. While it is impractical to ‘question everything’, CHIRP encourages readers to be curious about safety critical systems.
Maintaining situational awareness during maritime operations is vital to prevent accidents or personal injuries, especially when line-handling (M2138) or in tight spaces (M2142). Crews are
reminded to remain vigilant, question existing practices, and respond quickly to warning signs.
One aspect of crew well-being is the management of food allergies and intolerances. Companies must have effective policies in place for recording medical conditions, and such allergies need
to be declared to ensure the correct medicines are available and correctly administered when required.
As ever, we are thankful for the incident and near-miss reports that companies and individuals submit to us. Your reports have impact: you are helping to raise awareness of important safety issues, and by doing so, you are preventing future incidents, and keeping others safe. Thank you!
Yours in safety,
The CHIRP team
Reports
M2140 - Allergic reactions
Initial Report
A crew member experienced an allergic reaction during a recent incident while working in the catering department. They reported feeling tingling in their gums and a tightening sensation in their throat after having lunch. They promptly took antihistamines, and the Head of Department (HOD) was notified.
Although the symptoms did not worsen, the decision was made to seek further advice as a precautionary measure. Medaire was contacted, and they recommended taking the crew member to the local hospital for a thorough check-up. Another crew member accompanied them, and an EpiPen was administered as a precautionary measure. The crew member received two additional
injections at the clinic and was observed for two hours before being discharged.
The investigation revealed that the crew member had unknowingly consumed citrus fruit juice during their prepared lunch, which they were allergic to. The tingling gums, throat tightness, and difficulty breathing matched the symptoms of an allergic reaction.
CHIRP Comment
Although the company ensured that chefs were aware of the allergic effects of some foods, neither they nor the master knew that someone on board was allergic to citrus. Persons who know that they are allergic or intolerant to certain items are encouraged to declare this when they sign on. While such information is ‘medical in confidence’, it needs to be recorded somewhere so that effective first aid can be given should they be incapacitated and unable to communicate this.
To ensure your safety, your manning agents must be aware of your allergies, and your medical chest should carry sufficient medication in case of a reaction. Additionally, ensure you know your medical response contact details, especially when you are not in or near a port.
CHIRP would like to commend the officers and crew of the motor yacht for their excellent response in seeking advice and promptly getting the crew member to the local clinic for further assessment. The company’s commitment to a strong safety culture, prioritising the crew’s well-being, is highly commendable.
Key Issues relating to this report
Alerting – Ensure you alert your managers and the crew you work with about your allergies. It can save your life!
Communication – Does your company have a policy on allergy reporting? Society has more allergic reactions than ever, so we must be more mindful. Does your SMS health and safety section have a section on allergies and their response?
Teamwork – The response by the crew was excellent in ensuring the crew member’s safety- How often do you practice medivac drills using a similar scenario?
M2137 - Personal Injury due to gangway malfunction
Initial Report
While walking down the gangway to receive a package being delivered to the vessel, the gangway swung out from underneath them and the crewmember fell into the water, hitting their chin and right wrist on the quayside on the way down. They were partially submerged under the dock but kept one hand on it.
Luckily, they were swiftly rescued by a passing dock worker who pulled them out of the water, and although they had a sore head, neck, and arm, they could easily have suffered much more significant injuries.
A post-incident investigation found that the gangway had not been correctly installed and that this was due to poor supervision.
CHIRP Comment
This incident highlights the importance of proper equipment installation and safety certification for superyachts. CHIRP discovered several critical flaws.
Firstly, the design of the securing arrangement was inadequate and had likely been this way since build. The securing bolts were only screwed into the GRP fairing because the backing plate (into which they should have been affixed) was misaligned. This seriously compromised the structural safety of the gangway fixing arrangement.
Secondly, there was no Safe Working Load (SWL) plate next to the fixing point, so the crew could not know the gangway’s maximum capacity or working limitations.
The incident raises questions about the quality assurance of the vessel’s build, and whether differences between the vessel ‘as designed’ and ‘as built’ were properly identified and documented. It is imperative that these are discovered in during the building because they can significantly alter operating limitations. Once the vessel has been handed over to a crew, it is highly likely that such deficiencies will only come to light when the equipment catastrophically fails. Readers may detect similarities with the report in our previous edition about the failure of a lifting eye when hoisting the seaboat.
Collaboration among the shipyard, classification society, and contractors is crucial. Managers for the superyacht need to work closely with all parties involved to ensure proper communication and coordination throughout the construction and installation processes. All equipment should be certified as safe according to the appropriate design specifications before being put into service.
For newly built superyachts, an experienced new-build
team should work closely with the shipyard, class, and
contractors to identify and rectify potential issues during
construction. It is noted that not all owners use a new-build
team during the construction and fitting-out phases. If this is
the case, management must be responsible for verifying the
testing and sign-off for the equipment.
Key Issues relating to this report
Capability – Always check out the capabilities of contractors employed to carry out work on safety critical or access equipment. Seek assurances that they have the experience to carry out the work and always check the result by someone experienced to sign off the job as being carried out competently. Consult with the shipyard and class society to check if they have signed off on the installation. This cannot be left to the crew to do!
Local practices – When commissioning new vessels or equipment, question and challenge everything (yes, we know this can be very tiring and time consuming, but it can save your life! Has the installation been completed according to the specification and testing requirements? A member of the management team or new build team should be responsible for ensuring that the work has been completed and tested. The fact that there was no SWL plate on the gangway indicates that proper sign-off for the installation was not carried out.
M2136 - Capsize of a Dive Safari Vessel and Rescue of Tourists and Crew
Initial Report
Two additional decks had recently been added to a large liveaboard diving vessel which was subsequently chartered by a diving group for a trip to do both wreck and reef dives.
Early in the voyage, members of the dive group noticed that the vessel had a consistent list to port of approximately 2 to 3 degrees. They raised this with the crew, who assured the divers that this was most likely due to the unbalanced filling of the freshwater tanks for the voyage.
The vessel departed in the morning, and group completed two guided dives before the vessel went to anchor overnight. It was a calm night, but the group noticed that the list had increased to 4-5 degrees. Again, the crew reassured the group that all was well.
At first light, the vessel got underway and set off to another dive site – this time with a list of 5-6 degrees. As it approached the main shipping lane at 10 knots, the vessel heeled over to starboard and over the next hour the list progressively worsened until it capsized onto its side in less than 30 seconds. One of the vessel’s life rafts was released but did not inflate as the painter was not secured to the vessel. It was later manually inflated but could not be righted. The 2nd life raft was released and inflated, and the vessel’s tender boat, despite being slightly damaged, was used to tender passengers and crew to the life raft. Flares were released, and other nearby dive vessels came to assist. The dive team on board carried out dangerous and courageous rescues within the vessel to free trapped passengers and crew.
All passengers and crew (35) were eventually accounted for and taken back to port, where further assistance from the navy was provided to the traumatised survivors. According to our reporters, escape from the vessel was hampered by missing handles on one of the emergency escape hatches, and missing handrails on the stairs between decks made it extremely difficult to get out of the vessel. The lack of securely fastened furniture, including unsecured beds, also created a hazardous environment with floating debris obstructing escape routes. None of the passengers received a safety briefing upon boarding the vessel.
CHIRP Comment
Significant structural changes invariably affect stability, and inclining tests must be conducted to update the vessel’s stability curve data. Despite the passengers raising concerns on several occasions, it is troubling that the crew neither recognised nor reacted to the obvious warning signs. At best, this indicates a lack of training and at worst, the company put commercial interest above crew and passenger safety by continuing the voyage. Although the vessel had significant safety design defects e.g., lack of handrails on the steps between decks, the crew also demonstrated a complacent attitude to safety: items were not correctly secured for sea, nor were basic safety items such as the life raft painter correctly fitted. These, and the lack of a safety briefing for the guests, all point to a poor safety culture compounded by inadequate crew training and competency,
The successful rescue of all passengers and crew is a testament to the diving guests’ exceptional bravery and quick thinking. CHIRP has maintained contact with the dive team following the traumatic rescue. Many of them, including the passengers, are now receiving trauma counselling therapy.
Key Issues relating to this report
Design – Poor design choices when installing the additional decks significantly affected the vessel’s stability. Scrutiny of the stability requirements should have occurred before the refit; and after the work had been completed, it should have undergone an Inclining test overseen by the Class society and Flag.
Pressure – Commercial pressure to return the vessel to service meant that stability tests and sea-trials were not conducted. And once it had begun its fee-earning voyage, passengers’ concerns were ignored, which ultimately led to the vessel’s capsizing and endangering the lives of all passengers and crew. Commercial considerations must never be at the expense of safety. If you are a crew member joining (or on) a vessel that has had substantial structural change, ask to see evidence that stability tests and sea trials were correctly carried out.
Situational awareness – The crew did not recognise that the unexpected list was a sign of potentially inadequate stability, nor did they react when this got worse during the voyage. This is most likely due to insufficient training.
Culture – The operating company and the owners lacked care for the passengers and crew, as reported to CHIRP. They were not offered any counselling following their traumatic ordeal and had little in the way of any compensation despite losing all their equipment and possessions. Their lives were only saved because of their professionalism as divers.
M2142 - Contact with ground lines while departing a repair berth
Initial Report
The reporter informed CHIRP of an incident during departure from the berth.
The vessel was med-moored (berthed stern-to) in a challenging location. It was positioned between another yacht on the port side and a dock of small sailing vessels approximately 50 meters ahead on the starboard bow. The departure manoeuvre required careful controlling, with only 1 meter of clearance on either side and numerous ground lines present.
During the departure, the starboard stabiliser fin snagged a ground line belonging to one of the smaller sailing vessels. This incidental contact caused a slight movement among the adjacent yachts, resulting in a slow collision between the yacht’s hull and the vessel whose ground line was entangled.
Upon realising the situation, the master held the vessel steady in an awkward position while the entangled ground line was safely removed. The shipyard was promptly contacted, and they confirmed that no evident damage was observed except for the snagged line. The stabiliser was also assessed and proved to be operational with no damage.
CHIRP Comment
The reporter informed CHIRP that a pre-departure meeting was conducted before they left the tight berth. Due to the narrowness of the berth, the proximity of the ground lines and the limited space ahead, manoeuvring took a lot of work. The reporter also mentioned that this incident marked the second time they had encountered difficulties while departing from such a tight berth.
Our Advisory Board members discussed whether additional mitigation measures might have further assisted the master and crew during the departure. These included asking the port to temporarily relocate some of the other small boats to provide more clearance or the use of mooring lines to warp the vessel until it is clear of potential hazards.
It is best practice to discuss problematic departures the port authorities, and an illustrated departure plan is very helpful in such situations. These plans must consider the vessel’s specific requirements and consider potential hazards like the presence of ground lines. Escalating the issue to the port’s management well in advance can ensure adequate attention and resources are allocated to address your (un)berthing concerns effectively.
CHIRP emphasises the significance of thorough planning, clear communication, and situational awareness when manoeuvring in and out of challenging berths. The master’s skill in positioning the vessel to allow the removal of the ground lines from the stabiliser fin played a crucial role in preventing a much worse outcome.
Key Issues relating to this report
Local Practices – Engage with port authorities: employ open communication and, when appropriate, seek assistance early. If this practice is not common, challenge the status quo.
Pressure – Avoid letting pressure drive decisions. Prioritise safety above all else and avoid making decisions solely based on external pressures or tight schedules. Conduct thorough risk assessments and carefully consider the potential consequences of not exercising caution during manoeuvring operations. If a situation feels unsafe, insist on receiving support from the port before proceeding.
Teamwork – Embrace teamwork and encourage challenges: foster a culture of teamwork and collaboration among all involved personnel. Encourage team members to continuously question existing practices and propose improvements to enhance safety and efficiency. Even seemingly minor contact damage can escalate into more severe incidents, making teamwork and cooperation crucial.
M2138 - Personal Injury during mooring operations
Initial Report
During mooring operations, and while a 25’ tender was simultaneously being secured alongside the superyacht, the yacht’s aft spring line unexpectedly came under pressure.
The Chief Officer’s fingers were caught between the mooring line and the deck cleats, resulting in three broken fingers and nail and skin lacerations. The chief officer was working alone.
The incident prompted the company to introduce safety improvements during mooring operations to prevent such accidents in the future.
According to the incident report, the company should consider sourcing smaller diameter custom length mooring lines to secure the line’s working end aboard the tender. This change would leave only the spliced loop to be secured aboard the super yacht, eliminating the risk of two bitter ends being secured over each other on the yacht’s deck cleat. They should also consider switching to a more flexible line and installing snubbers to absorb stress on the deck cleats. These measures will help reduce the likelihood of accidents and injuries during mooring procedures.
Additionally, the company proposed additional training for all crew members working with lines on deck, highlighting the dangers of working alone during mooring operations.
CHIRP Comment
This is very much a seamanship matter concerning securing the tender and other vessels alongside, and the suggestion proposed is reasonable and seamanlike.
The company should consult the master on how the tender may be released in an emergency. CHIRP also suggests that preventing injuries to crew must be part of the design specification. The sleek-looking arrangement is in keeping with the aesthetics of the motor yacht, but it needs to be safe for the crew operating the moorings.
Key Issues relating to this report
Situational Awareness – Mooring operations demand good situational awareness and physical coordination, given the risks of lines under tension. Carrying out mooring operations without having the necessary support to keep you advised of changing line tensions is very dangerous. Always have someone supporting you during mooring operations.
Teamwork – Mooring operations demand collaboration where one person monitors the operation for safety, and everyone else looks out for each other. At the Toolbox meeting, emphasise to everyone taking part to challenge if something needs to be corrected or is potentially unsafe.
Pressure – Never rush mooring operations due to pressure, perceived or otherwise.
M2111 - Grounding and dismissal
Initial Report
Our reporter, a watchkeeper on a yacht, informed CHIRP that their vessel ran aground while navigating in an area of shallow water at over 9 knots. It was approximately 3 hours after sunrise when the grounding occurred.
Screenshots of ECDIS (Electronic Chart Display and Information System) show that the planned track – shown as a dotted line – went over the top of a 1.9m shoal depth even though the vessel’s draft was 2.3m. The vessel’s course – shown as a solid line – was starboard of the planned track buts still grounded because of a combination of shallow water, speed and squat. This resulted in the vessel dry-docking for several weeks for significant repairs.
The reporter explained that the master created all passage plans, but none were recorded in the vessel’s navigation management system and that watchkeepers frequently had to deviate from the planned routes to avoid charted hazards. Our reporter was concerned that the master’s proficiency in planning navigationally safe routes was lacking and that they sometimes struggled to interpret RADAR and ECDIS information. The reporter’s employment was terminated when they raised these concerns through the company’s safety reporting system.
Subsequent correspondence with the reporter revealed that to satisfy the owner or guests’ requests to visit certain locations, the vessel often navigated to areas ‘by eye,’ i.e., visually detecting shallow areas because even large-scale charts lacked sufficient sounding data.
CHIRP Comment
This report raises several issues. Firstly, although certificated, the master’s navigational skills appear inadequate. It is vital that company managers validate the skill of masters and other senior officers and do not rely solely on the possession of a certificate as a measurement of competency. Secondly, route plans should always be cross-checked by another watchkeeper because even the best navigators can make mistakes.
The third issue is that guests’ wishes to visit a particular destination need to be balanced against the navigational risks of getting there. In Superyacht FEEDBACK edition 01, we strongly encouraged masters to get agreement from the owner or guests at the outset that they will respect the master’s professional judgement and the need to say ‘no’ when a request compromises the vessel’s safety. Navigating ‘by eye’ is not sound practice and is unlikely to be accepted as such by an accident investigation board!
CHIRP discussed with the relevant hydrographic office (HO) the issues experienced concerning navigating in the area related to the report. Crucially, a compliant ECDIS system must be used, and the charts must be updated to the latest edition and corrections. It was noted that an official ECDIS system with ENC was not used for the navigation of the vessel.
The HO placed great weight on using the sailing directions for the area as a pre-requisite before planning the passage. They contain valuable navigational information, including the nature of the seabed and the likelihood of shifting sandbanks, which in this case were prone to shifting. The vessel’s speed must be set according to the under-keel clearance to avoid significant squat. Most fine-lined superyachts will trim by the stern when experiencing squat effect, and damage to the propellers and rudder can be expected if the vessel touches the seabed.
Source data (Zones of confidence)
The source data for the charts used should be considered part of the navigation passage plan (risk assessment). Again, the area under consideration in the report shows sparse-sounding data, with some of the best data shown by occasional lines of miscellaneous soundings. Risk for groundings must be considered high given the lack of data, and routes that have been proven safe in the past should be considered in the passage planning.
Many hydrographic offices (HO) operate a system for navigators and other watchkeepers to report areas where they believe the chart data is insufficient to support safe navigation. Often, they have limited resources and necessarily prioritise known areas of high traffic (e.g., commercial routes), but they are also keen to understand the needs of other users. When CHIRP contacted the appropriate HO about this report, they immediately added it to their list of areas to be reviewed, and readers are encouraged to do likewise.
Most hydrographic offices have good reporting apps or reporting forms to allow data to be sent so that paper and electronic charts can be updated. CHIRP encourages all superyacht owners and managers to provide the relevant hydrographic offices with the latest sounding data by using the various reporting apps that are available. This will provide reliable data for other users to consider in their passage plans.
The final issue is that of the reporter being sacked for raising safety concerns. This demonstrates a very poor safety culture within the company and does absolutely nothing to reduce safety risks. CHIRP encourages Flag States to introduce employment protections for those who are sacked for raising valid concerns.
Key Issues relating to this report
Capability – Those responsible for appointing senior officers (e.g., masters or first mates) should satisfy themselves that the appointees can demonstrate practice competence and evidence that they have maintained their skills since qualification, which in some cases might have taken place years or even decades beforehand. This mitigates against skill-fade and any bad habits picked up along the way.
Alerting
(1) Navigation plans and other critical work should always be cross-checked. This helps with the early detection of errors, prevents ‘group-think’, and can be a powerful learning/teaching opportunity for everyone involved. No one is too senior to learn from others, and rank does not confer infallibility!
(2) Being unafraid to challenge constructively is vital to safety. Sacking someone for raising a safety concern sends a clear signal that your company is not interested in safety.
(3) Navigating in areas which need to be adequately sounded requires those that can record accurate data to do so. Sounding information, passed on to the relevant hydrographic
office, is very valuable and helpful for all mariners.
Local Practices – Navigating ‘by eye’ and similar practices may be accepted unofficial practice in some vessels, but it doesn’t mean that it’s safe – and “But it’s what others do” is not a valid defence. If the correct process (e.g., using charted data) isn’t adequate, report it to the relevant authority or to CHIRP.
Culture – Dismissing a person from the company’s employment for reporting an incident does not demonstrate a just culture. It should be the aim of every organisation to strive for continual improvement and sharing the learning outcomes from any incident can only help in improving safety. Can you share with CHIRP similar incidents that you have experienced?