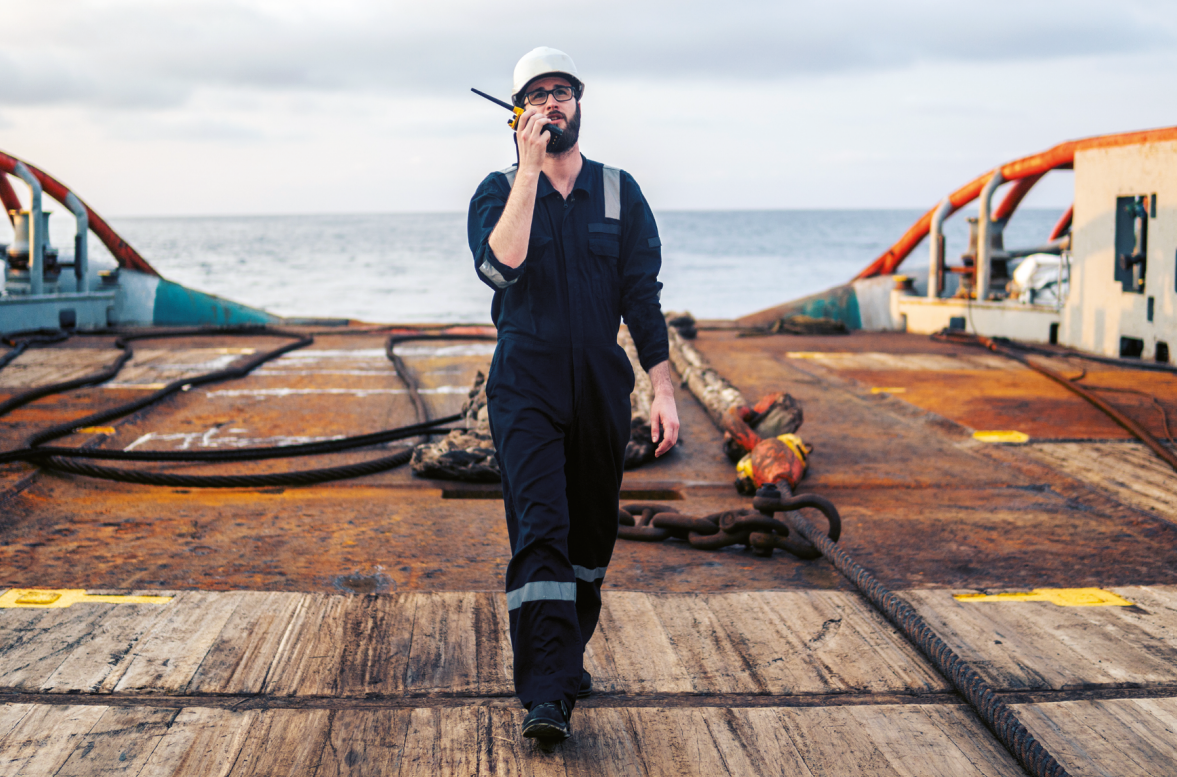
It’s good to talk!
Contents
- M2252 - Hand injury while mooring on a workboat
- M2216 - Inappropriate pressure placed on the master
- M2183 - Fire in the laundry room
- M2234 - Fingers amputated in rotating machinery
- M2254 - Fire – Resin in a container
- M2246 - Grounding
- M2255 - Shortage of provisions on board
- M2253 - Fire - Charcoal
Once again we feature a wide selection of different incidents, and we are grateful to all our reporters for sending them to us. Without them, Maritime FEEDBACK would not exist.
In this edition we have three different types of fire, two hand injuries and a variety of other unfortunate events but there are some common threads running through them. Perhaps the most obvious is the need for better communication, whether it is between crew members or with shore personnel or the vessel’s management. This is a theme we see very often in our reports, and by now it should be obvious that good communication is vital to safe operations. If you see something which is not right, you should feel empowered to speak up. And if you are discouraged from voicing your concerns then it may be wise to look for a company where safety is taken more seriously.
Teamwork and the benefits of mutual support also feature prominently, especially when people must work alone. Does anybody oversee the crew handling mooring ropes on your vessel, and does the electrician get the support he needs? Do management and local agents ensure you have the details you need to stow and carry cargoes safely? Do your officers receive the support they need from shore management when they face pressure from external sources to cut corners?
In this edition we use the word ‘escalate’, which means passing your concerns up the chain of command. If you see a potential problem, inform a senior officer who can escalate your report to the master. The master can then escalate it to the DPA if necessary. Good officers will always take you seriously and deal with your concerns.
Until next time, stay safe.
Reports
M2252 - Hand injury while mooring on a workboat
Initial Report
A reporter recently had an incident on board one of their vessels, where a deckhand injured the fingers on their right hand.
The vessel was headed to the pontoon to moor alongside her regular berth. As the vessel’s aft port quarter came alongside the pontoon, the deckhand used the boat hook to pick up the ‘in-situ’ mooring line and began feeding the spliced eye through the fairlead. They then started placing the line over the bitts; this is where the deckhand’s fingers on their right hand became trapped, and serious injuries were sustained to three fingers.
CHIRP Comment
Placing a mooring line over the bitts requires very good situational awareness of the vessel’s movement, the position of the mooring line, and the crewmember. The risk of hand entrapment is a well-known hazard, and it can be normalised during routine operations.
Once the eye of the mooring line is through the workboat’s fairlead, a sufficient length of the mooring line should be available on the workboat so that the eye can be placed over the bitts without the crew’s hand making contact with it. This would prevent any sudden snatching of the line, which could trap the crew’s fingers if they were holding the eye of the mooring line.
For heavier lines, a short, stout rope can be fastened to the mooring’s eye so that it can be hauled over the bitts without any hand contact with the mooring eye.
Vigilance from another crew member, usually the coxswain, to provide a safety cross-check should ensure that hands are always clear of the eye when securing the eye to the bits on the work boat. However, the design of a workboat does not always provide a clear line of sight to the working deck.
Hazards encountered during routine work can be normalised and create greater danger for the crew. Additional safeguards are required, including alerting, training, and changing working practices to keep hands away from the eye of the moorings.
Key Issues relating to this report
Situational awareness– Maintaining good situational awareness when doing a regular job can be demanding. Do you have someone checking on you?
Communication—It Is essential to check on your workmates whilst doing the mooring. Does your workboat have a good line of sight so everyone can see what is happening? Do you have a buddy alerting system?
Design —Is the workboat’s design adequate to ensure that mooring transfer operations are optimised for safety? Is the correct length of the in-situ mooring line appropriate? Should it be lengthened to allow less chance of finger entrapment? Or should the mooring line not have a mooring eye and be turned up on the bitts? Management should review the design of the workboats to determine whether they are fit for purpose.
M2216 - Inappropriate pressure placed on the master
Initial Report
The master of a large vessel received unusual instructions from charterers concerning pre-arrival reporting to the authorities.
The vessel had sailed with both anchors damaged, one more so than the other. A dispensation to sail was granted, and a condition of class was imposed on the vessel. New anchors would be supplied to the vessel at the next port.
The master was advised not to mention the dispensation letter to the port authorities at the next port, as revealing the state of the anchors would require a tug escort to the berth.
CHIRP Comment
A dispensation letter is usually a one-off temporary permit to sail to the next port, where spare parts or replacements for technical problems can be rectified. The authorities granting the dispensation letter, usually from the class society, do so based on a risk assessment. As such, it must be conveyed to the next port during the port pre-arrival information exchange. The dispensation letter is a lifeline, granting temporary reprieve amidst technical challenges.
The Master must exert their overriding authority to mitigate the risks. This is a legal requirement, and pressure to do anything other than act safely must be refused. CHIRP advocates that when such requests are received, the master consults them to the ship’s DPA in writing.
Given the complete loss of anchoring efficiency for one of the anchors, employing an escort tug is the correct mitigation measure in a higher-risk port area to ensure safe passage to the berth.
Additionally, failure to follow the dispensation requirements can invalidate the vessel’s insurance cover in the event of an incident. Cutting corners has severe consequences—a single misstep can unravel insurance coverage, leaving the vessel vulnerable to legal issues.
Ultimately, in an incident where the anchors are required but they cannot function, and the port has not been informed, the company can be prosecuted for failure to notify.
When in doubt, escalate. The master’s duty is not just to navigate the vessel; it is to navigate through a maze of regulations, ensuring every decision is a commitment to safety. Commercial costs for providing an escort tug must never interfere with the vessel’s safety.
There is no compromise in maritime operations: safety must always come first.
Key Issues relating to this report
Pressure- Excess pressure to ensure that commercial costs and operational deadlines are met is a dangerous human factor that creates unnecessary doubt and can cloud the judgement of those making critical safety decisions.
Culture—The chartering team’s connection with safety was poor, and the ship management team did not support the master’s openness in reporting the dispensation with the port authorities and sharing the risks outlined by the dispensation letter.
Teamwork- The organisation is pulling in different directions, compromising safety. Reading this report, do you feel that this sometimes happens to you?
Local Practices—Follow the correct legal requirements as Master and put in writing your concerns. Contact the DPA. The financial consequences of using an anchor that cannot function and then discovering that the situation has not been disclosed in the port arrival information will be many times higher than the tug escort fees. The reputational damage to the company will be even higher.
M2183 - Fire in the laundry room
Initial Report
Directly after some tea towels had been in the tumble dryer, they were put in a plastic garbage bag and placed on top of it. After some time, the fire/smoke detector in the laundry room was activated, and the crew was alerted. When entering the laundry room, they noticed smoke from the plastic bag. They managed to put out the smouldering fire with an extinguisher.
CHIRP Comment
Placing hot towels or boiler suits that have not cooled down sufficiently and may still contain oil /grease residues in the fabric in a plastic bag on top of a tumble dryer creates the conditions for spontaneous combustion, which is a common cause of shipboard laundry fires.
Spontaneous combustion occurs when a combustible material with traces of oil/grease in the fibre heats up and reaches its ignition temperature, involving oxygen in the air (oxidation). The oxidation of the flammable material creates the heat.
It is essential to ensure that the tea towels are properly hot washed to remove the grease and oily residues on the cloth before drying them in a tumble dryer. The appropriate type of detergent should be used to ensure they are clean of oily residues.
The tumble dryer should be set appropriately to ensure that the towels go through a proper cycle, including the cooling cycle, so they are not hot when the cycle is completed. The filters in the tumble dryers should be cleaned before each cycle. Blocked filters prevent good airflow and prevent drying of the clothes during the cycle. They should then be separated, placed in the drying room on completion, and never placed on top of the drying machines.
Laundry rooms are particularly high-risk environments for fire, and the cleanliness of the machinery is essential to prevent fires. Detector heads, ventilation fans, fire-fighting appliances (FFA), and suitable door-closing arrangements must be adequately maintained to mitigate the fire risk. Regular fire drills should be carried out in this area to train the crew to be alert to the potential for fire.
Given their high use, the equipment should be considered for replacement every five years during a docking period.
Key Issues relating to this report
Local practices: Follow well-established laundry cleaning procedures and do not adhere to unsafe practices. If you see practices that differ from what you have been trained to do, speak up.
Alerting—Alert those responsible when you see something that is not safe. How often have you visited the laundry room and seen unsafe conditions? Did you report them?
M2234 - Fingers amputated in rotating machinery
Initial Report
At about 14:50 hrs LT, the electrician left the engine control room, went to the electrician’s workshop to leave his tools, and then went for his work break. While passing the refrigerant provision plant, he saw dust in the idle No. 2 electric motor compressor. The ETO used a rag to clean the motor’s axis and turn the belt.
Dust was also seen on the No. 1 electric-motor compressor. The No. 1 unit was in “auto” mode, but the motor was not running. The ETO used the rag again to clean the axis, and at that time, the motor started to operate. The rag got tangled between the motor and the compressor.
In an effort to pull out the rag, the electrician’s right hand became caught in the motor’s belts. The electrician felt great pain as three last fingers were partially amputated. The vessel was in port, so the electrician was taken to hospital, where the last three fingers ( middle, ring, little) were amputated, about 1/3 of each finger. The injury caused permanent incapacity for employment at sea.
CHIRP Comment
The report highlights the importance of maintaining mindfulness in our actions and surroundings, especially when individuals work independently. Despite being aware of the risks involved, the electrician’s decision to conduct unscheduled cleaning resulted in a tragic oversight of essential safety measures. It emphasises the need for a systematic approach, such as Stop, Look, Think, Assess, and Look Again, to ensure thorough assessment and awareness before undertaking tasks.
Operating autonomously, ships’ electricians may only sometimes have direct oversight, potentially leading to neglect of vital safety procedures. Therefore, it is crucial to regularly remind the ship’s Electro-Technical Officers (ETOs) to seek assistance if they deviate from planned work, typically assessed at daily work planning meetings.
The incident underscores the dangers of machinery operating in automatic mode, which may remain inactive until triggered by specific signals. Implementing robust safety measures like the Tag Out-Lock Out-Try Out (TOLOTO) system is essential to address such risks. This system ensures equipment is adequately secured against unintended operation during maintenance or cleaning activities. Additionally, installing protective guards on equipment adds another layer of defence against lapses in attention or mindfulness.
Key Issues relating to this report
Teamwork- Considering your last ship, how well did you communicate with the electrician? Were they provided the necessary support, and did they feel they were part of the team?
Distractions- How often do you become distracted from your current intentions to go to a place or do a job of work? Would you alert someone if you were going to make a change of plan and do something different?
Situational Awareness—The refrigeration provision plant runs continually throughout the ship’s working life. Its machinery operates periodically in an idle state and can start without notice. Working in this area demands a high level of awareness, and work should not be undertaken unless signed off by another supervising senior officer.
M2254 - Fire – Resin in a container
Initial Report
The fire was discovered as the vessel lay anchored off a port. Following the activation of the vessel’s fire alarm, assistance from the shore authorities was sought. Fireboats from the maritime authorities were dispatched. Water cannons were employed to engulf the burning deck container stacks. After several hours, the fire was reported to be under control.
The operation involved firefighting in a restricted space and resulted in damage to the containers on fire and to adjacent containers.
CHIRP Comment
CHIRP commends the crew and shore authorities for their swift action in containing the fire, which posed a significant threat to the vessel. The incident underscores the difficulty of combating fires in confined spaces like those found on ships.
Understanding the contents of containers is crucial for crew safety and vessel integrity. Mis-declared containers, a common issue, can significantly endanger crew lives. In this case, the containers involved contained resin, which can be transported in various forms, such as bags, drums, containers, or bulk, and may fall under IMDG Class 3 or 4, depending on their state.
Liquid resins, classified as IMDG Class 3, are highly flammable and can form explosive vapours in the air. Some resins may polymerise explosively when exposed to heat or fire.
Both liquid and solid resin spillages can trigger exothermic reactions when they come into contact with other substances in the container. It is essential to exercise due diligence with shippers to ensure proper packaging, stowing, and labelling of goods.
CHIRP recommends providing a photograph of the stowed dangerous goods (DG) container before sealing the doors. This allows the crew to understand the cargo behind the doors, enhancing their awareness of the challenges in combating fires involving such cargoes.
Key Issues relating to this report
Capability—Do your ship and shore staff properly know the IMDG code to understand the risks? Have you been given a training course on transporting dangerous goods by sea? Does your ship have the necessary firefighting equipment to fight different types of fire in restricted spaces?
Communications- How diligently does your company engage with shippers who ship dangerous goods?
M2246 - Grounding
Initial Report
A reporter recounted an incident to CHIRP involving a grounding that resulted in the loss of jobs for the reporter and another officer. The incident caused minor damage to the vessel’s hull bottom but no physical injuries. Contributing factors were distractions and poor preparation.
On the day of departure, the master was preoccupied with obtaining a crew visa and addressing engineering problems. Due to the visa requirements, the vessel was already a few days late setting sail for the 10-day passage to return to its home port. Despite these challenges, the passage plan was completed by mid-afternoon. However, a critical issue arose with the primary ECDIS system, displaying incorrect charts for the planned route. Despite this, the decision was made to depart using information from other sources, including paper charts and a secondary ECDIS display, and knowing there would be a pilot onboard.
During the vessel’s unmooring, the pilot’s apparent distraction with their phone hindered communication and coordination. Despite the very brief master pilot exchange for the outbound passage, there appeared to be no overall control over the vessel’s navigation. Concerning the pilot’s action, there was a lack of appropriate response and communication to some basic navigational queries, including the buoyage, during which time the vessel strayed off course. The master’s intervention to get the vessel back on the track came too late to avert the grounding.
Following the grounding, the crew responded promptly and effectively. Efforts to refloat the vessel at the next high water were successful, with minimal damage sustained. Subsequent inspections found no significant damage to the vessel’s structure or running gear after an underwater inspection was carried out in accordance with the port authority’s requirements.
CHIRP Comment
This grounding incident stemmed from a series of human factors issues, indicating a breakdown in navigational procedures and communication on the vessel.
Upon arriving at the bridge, both the master and the pilot were distracted, compromising their ability to focus on safely navigating the vessel. This distraction likely contributed to a lack of thorough understanding and discussion of the passage plan, which had only been completed shortly before departure. As a result, there was insufficient time for the master and other officers to assess and approve the plan properly.
Responsibility on the bridge was diffuse, leading to no action or delays in decision-making and a failure to take necessary actions to correct deviations from the passage plan. Furthermore, the inability of instrumentation alarms, specifically the ECDIS and echo sounder, to activate when the vessel deviated off track and entered shallow waters suggests potential technical failures or improper setup of these systems.
Despite having alternative navigation systems, such as paper charts and another ECDIS system, there was no evidence that these were utilised to verify deviations from the passage plan. This highlights a missed opportunity to cross-reference information and mitigate the risk of navigational errors.
Overall, this incident underscores the importance of effective communication, thorough planning, crew training, and the proper functioning of onboard systems in ensuring safe navigation at sea.
Key Issues relating to this report
Distractions – Too many issues affected the master during this very hectic departure, and insufficient attention was given to the vessel’s navigation. The pilot was also distracted with phone calls and did not assist the bridge team with adequate navigational information.
Teamwork —Bridge teamwork was dysfunctional, creating an unsafe condition for navigation. The vessel was left with no overall control until the grounding. Applying for a visa should be delegated to another member of the officer complement or the ship’s agent.
Pressure—Commercial pressure to return the vessel to its home port created unnecessary stress for the master. Visa issues, engineering problems, and bridge navigation issues were compounded by a pilot who appeared detached from the job he was employed to perform.
M2255 - Shortage of provisions on board
Initial Report
The reporter informed CHIRP that a bulk carrier crew was out of food. When some crew members visited the seaman’s mission, they received expired food supplies from a local supermarket at a reduced cost to the crew. The reporter indicated that the crew was starving as no provisions were on board.
The report requested that CHIRP intervene and inform the authorities to check the food status on board. CHIRP contacted the Port State Control, and an investigation was carried out.
CHIRP Comment
All Flag States mandate a minimum requirement for crew daily food provisions, which must be reflected in the company’s budget. This includes allocating a reserve allowance for essential provisions when there may be uncertainty in the vessel’s port rotation and access to good providers.
The provision of poor-quality, inexpensive food not only leads to higher wastage but also poses long-term health risks to the crew, including increased rates of diabetes, obesity, and heart problems. Running out of food for the crew is totally unacceptable and should only occur in exceptional circumstances.
The master and crew failed to give adequate attention to provisioning, a critical aspect of ensuring the vessel’s seaworthiness. The amount of food required must be assessed based on crew size, trading pattern, and the availability of suitable victualing companies. Neglecting this assessment can result in severe consequences for crew health and morale.
Purchasing expired, or reduced-price food indicates that the food budget is driven by cost-saving measures rather than prioritising the crew’s well-being. This practice is unacceptable and compromises the safety and welfare of those onboard.
Key Issues relating to this report
Capability—The master usually has the responsibility of checking the quality and quantity of food on board. This requires close attention to the requirements and working closely with the cook. How well do you manage this job? Do you feel your provision budget is too tight to order good quality food? Does the cook on your vessel hold the appropriate cooking certificates? Are there regular refresher cooking courses that can be taken? How varied are your meals?
Alerting- If you felt that your food quality and quantity were insufficient, would you contact your DPA?
Culture- Having the right type of food available creates an excellent social atmosphere and is part of good onboard social culture. Please see The Social Integration Matters (SIM) project, which was carried out by The International Seafarers Welfare Assistance Network (ISWAN).
M2253 - Fire - Charcoal
Initial Report
Smoke and a burning smell were detected during port operations. One container stowed in the hold was found emitting smoke, and the side wall of the container was bulging due to the heat and pressure. The container was discharged promptly and moved to the terminal container yard.
CHIRP Comment
Fortunately, an observant crew member or stevedore saw the signs of fire early before other containers were loaded on top.
Charcoal, categorised as UN1361 and falling under Class 4.2, presents unique risks due to its tendency to spontaneously ignite if stored improperly. Essentially, when exposed to oxygen, charcoal oxidises, generating heat. To ensure accurate understanding, shippers must precisely label the cargo as carbon/charcoal, as it goes by other names, and its hazardous nature may not be apparent otherwise.
The IMDG Code includes a special provision (SP 925) allowing exemption from Class 4.2 classification under specific conditions, permitting bulk shipment of charcoal. Accredited authorities must conduct and document tests and issue certificates to confirm compliance before transportation is permitted.
Storing warm or hot charcoal accelerates oxidation, leading to dangerous heat build-up that standard cooling methods may not counteract. This self-heating process can escalate to ignition, posing significant risks. The duration for self-heating varies by charcoal type and weathering and is typically around two weeks before loading into a container.
To address the challenge of charcoal fires, CHIRP advises storing containers on deck for easier access, facilitating swift containment and safe discharge in port, thereby reducing hazards.
The Cargo Incident Notification System (CINS) and the International Group of P&I Clubs offer valuable guidance on the stowage and handling guidelines, jointly published in their 2017 document ‘Guidelines for the Carriage of Charcoal and Carbon in Containers’.
Key Issues relating to this report
Pressure- Did undue pressure allow the charcoal container to be shipped without the proper procedures? Have you examined how your charcoal is processed before being shipped on board?
Local practices—This is a high-risk cargo, where there is always a risk of fire. Never cut corners. Ensure that proper documentation is provided and be alert to local norms at different ports.
Capability—Do your office and ship’s staff have the necessary training to appreciate the IMDG code fully? Does your regular shipper have proper processes to ensure the charcoal is safe to carry? Do you regularly check the temperatures of containers loaded with charcoal? Does your ship have an infrared heat gun?
Design- is your ship fitted with the necessary firefighting equipment to handle a fire in charcoal stowed on deck?