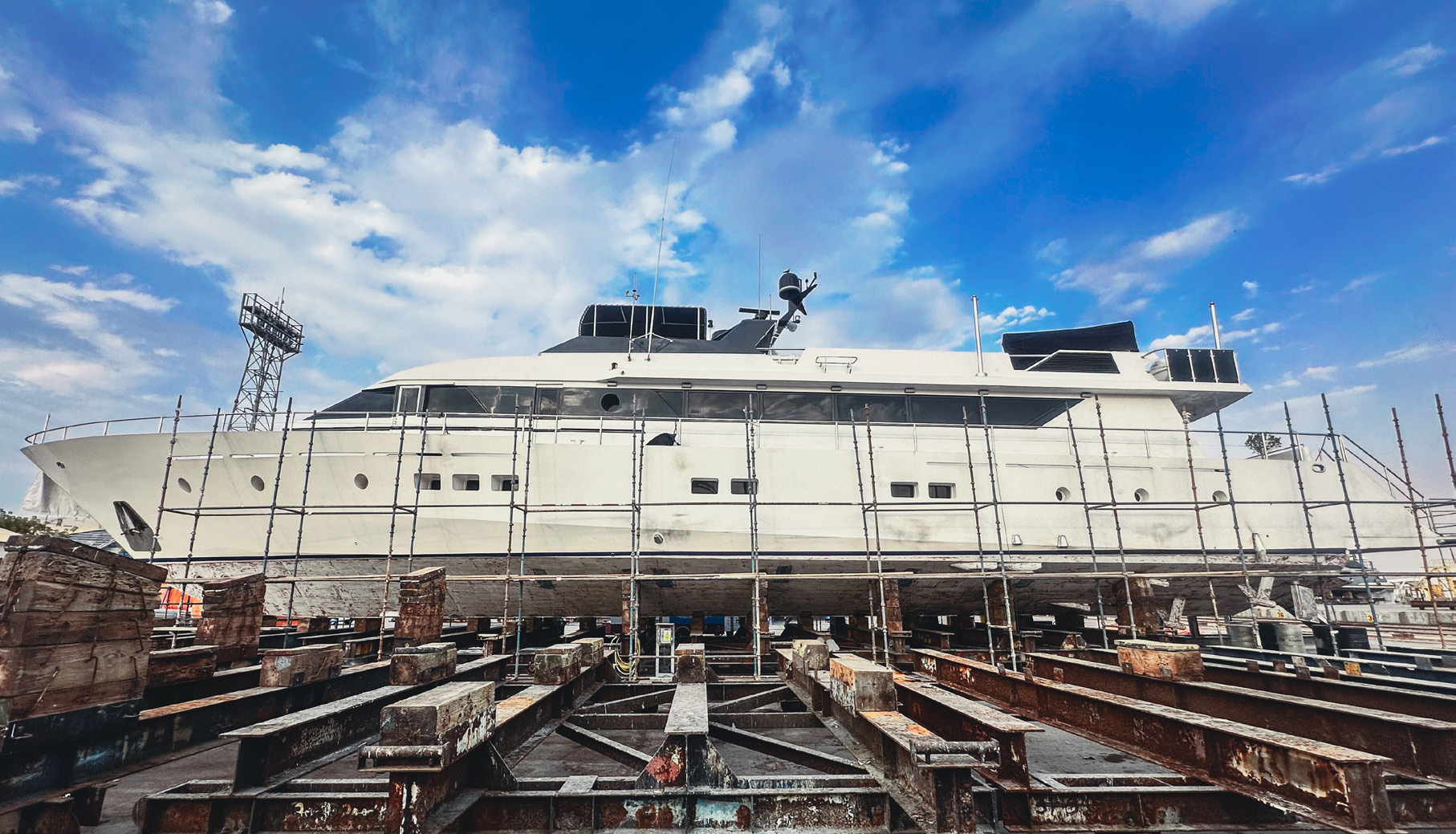
Drugs, Design and Dry-docks!
Contents
- M2319 - Fire on a large motor yacht
- M2325 - MLC living conditions
- M2352 - Drug use on board superyachts
- M2353 - Working aloft: unsafe by design?
- M2362 - Near Miss- fatality avoided
- M2361 - Anchor operations compromised by unfamiliarity and tiredness create a hazardous situation
- M2358 - Identification of Enclosed spaces on a Super Yacht
“D” is for danger…
Many of the reports in this excellent edition possess a sense of familiarity, as they resemble recent reports published in Maritime FEEDBACK or in earlier super yacht bulletins.
One familiar theme is that things often go wrong during or shortly after drydockings, and it is worth bearing in mind that management and crew may not have very much experience of dockings, so everyone
needs to remain alert and anticipate problems. Even fewer people have experience of taking delivery of a newbuilding vessel, where design problems can become apparent and where owners and managers
must make every effort to change things which are not safe, even if they have been accepted by other owners, class or flag state surveyors.
We also feature reports highlighting instances where fatigue and insufficient familiarisation training are factors, and we learn about a crane missing a vital safety sensor. Equally unsafe was a yacht where the crew were expected to live on board during dry docking despite the dreadful conditions.
Two reports are especially worrying – one where a super yacht claimed to have no enclosed spaces at all, and one where some officers and crew appear to have had drug problems.
On a positive note, several reporters said they felt emboldened to report to us because they had read similar reports by CHIRP, so they knew something was not right. We are delighted to learn that our efforts are bearing fruit.
Finally, we thank all our reporters for their commitment to safety and for making this such an interesting edition.
Reports
M2319 - Fire on a large motor yacht
Initial Report
After the dry-dock period, the motor yacht was moved to the repair berth, where shore power was unavailable, necessitating the use of the ship’s generators. Before the relocation, the vessel underwent a pre-sale survey, and the ventilation dampers were closed. This raised the temperature in the engine room. The master was not informed about the switch from shore to ship power. According to practice, the ER door was shut after working hours, while the emergency escape hatch was left open for ventilation. Later, the ER fire alarm was activated. The captain briefly inspected the ER, noted haziness but no strong odour or visible fire source, and closed the door.
The fire team disabled technical ventilation and fuel supply to the ER, prepared fire hoses for boundary cooling, and donned fire suits with breathing apparatus. The engineer and deckhand entered the ER, discovering smoke near Generator No. 1, but not directly from it. They shut down the generator, leaving the vessel without power, and secured the emergency hatch.
Significant issues hindered the response: the emergency fire pump was challenging to operate, the emergency generator was inoperative, smoke detectors and atmosphere testing equipment were absent, and the fire system’s UPS battery had failed. Unable to monitor the ER, the master activated the CO2 system. However, unfamiliarity with its release procedure and difficulty accessing the CO2 cabinet led to incomplete activation.
Emergency services intervened, dispersing the accumulated gas and ensuring safe re-entry. Investigations revealed that the fire was caused by the accumulation of exhaust gas due to a leak in the exhaust system and a malfunctioning exhaust valve. Closed dampers that restricted air circulation exacerbated the situation. The failure of the CO2 system resulted from a misconnected compressed air hose linked to the emergency quick-closing system of the fuel valve, resulting in the manual release of the CO2 bottles. While manually releasing the CO2, the crew was unaware that the CO2 cylinder valves must be held open until fully discharged. The vessel remained incapacitated until the CO2 system was recharged.
CHIRP Comment
As highlighted in previous CHIRP feedback, drydock operations pose significant risks, requiring the crew to remain vigilant and well-prepared.
A critical safety protocol is the immediate mustering of all personnel before CO2 is released, especially given the presence of shore workers who may still be on board. However, this report highlights a lack of exposure to drills and training. Management is responsible for ensuring crew members receive adequate training to protect themselves and the vessel.
Serious safety concerns were identified, including the lack of a functioning emergency generator and challenges in operating the emergency fire pump—issues that could render the vessel unseaworthy. Furthermore, drydock periods may result in an overreliance on shoreside resources. Once these resources are withdrawn, the ship’s crew must be completely prepared to regain operational control.
Findings indicate that some crew members were unfamiliar with critical safety equipment, and specific equipment had not been adequately maintained. This highlights a broader issue that requires a cultural shift in management’s approach to safety. Regardless of the vessel’s luxury features, it remains a ship that must support its crew at sea. Prioritising the enhancement of training and dry dock safety management is essential.
A dedicated pre-departure dry-dock checklist should enhance safety, distinct from the standard port departure checklist. This checklist should confirm that all systems and equipment are fully operational, guaranteeing that the vessel is returned safely and seaworthy before leaving the shipyard.
Key Issues relating to this report
Capability – The vessel lacked the necessary experience to perform dry docking. It eventually departed the drydock unseaworthy and could not re-enter service.
Communications – It was unacceptable not to advise the master about the lack of shore power supply, as the emergency generator was inoperable.
Alerting – Given the situation on board with non-operational essential safety appliances, would you have spoken up?
Pressure – The pressure to get the vessel from the drydock to the layup berth following a pre-sale inspection meant that the ship’s staff did not restore the vessel to a seaworthy condition.
Culture – The lack of communication about shore power and misunderstanding of emergency procedures reflect a weak safety culture in which critical issues are not addressed.
M2325 - MLC living conditions
Initial Report
Our reporter stated that during a recent dry-docking period, the crew were compelled to remain on board while the vessel underwent substantial repairs, raising serious safety and welfare concerns. Open fuel tanks were situated in crew living areas, and essential services such as air conditioning, water, and sewage were intermittently shut down for prolonged periods. Galley refrigerators were switched off, necessitating chefs to store food in domestic fridges on the aft deck. Hazardous work, including antifouling, painting, and grinding, occurred throughout the vessel, while smoke detectors were disconnected to facilitate the removal of ceiling panels, compromising fire safety. Despite these issues, no action was taken by management, prompting the crew to report the situation to CHIRP.
CHIRP Comment
CHIRP emphasises that crew living conditions were found inadequate during essential service repairs. According to the Maritime Labour Convention (MLC), management must provide suitable alternative accommodation, whether commercial or private, and health, safety, and environmental (HSE) regulations take precedence during dry-docking periods regardless of vessel size or purpose.
Moreover, the master has a duty of care toward the crew, always ensuring their well-being. During dry dock, the vessel encountered hazardous operations that management should have addressed promptly. The owner’s and manager’s lack of response to crew concerns highlights a poor safety culture within the company.
It’s important to emphasise that standards must be strictly applied whether the vessel is MLC-compliant or a private yacht.
If a proper assessment of the work during the dry dock had been planned, the planned work could have been carefully managed. Management must ensure an experienced team of officers is brought in to manage the dry dock.
Key Issues relating to this report
Culture – Management does not show a duty of care to the crew by not providing appropriate accommodation during a phase of the drydock when living conditions become unacceptable.
Situational awareness – Management has not examined the dry-dock operation in its entirety. It has either failed to recognise or ignored that the crew will face unacceptable living conditions as work progresses on the vessel.
Capability – The management has not supported their crew, and they appear to lack the knowledge and experience to recognise the work requirements during the dry dock.
Communications – Management has not conveyed their expectations regarding the living arrangements during the dry docking period.
M2352 - Drug use on board superyachts
Initial Report
Our reporters sought to illuminate a potentially hazardous situation aboard a sizeable superyacht. The issue reported to CHIRP pertains to the levels of drug consumption occurring among the crew and passengers, fostering a drug-fuelled environment that presents a considerable risk to everyone on board. It starts with the senior officers down, making tender operations dangerous, especially after hearing about recent incidents.
The reporters stated that it is just nerve-wracking and wrong because they know how much drug use occurs on board and how unsafe it can be. The reporters wish to raise their concerns with CHIRP.
CHIRP Comment
CHIRP wishes to thank the reporters for highlighting this serious safety issue. The situation on board has escalated and compromised safety. CHIRP has addressed this matter with the Flag State, which has taken steps to investigate.
CHIRP appreciates Flag State’s strong support for this issue. If you encounter similar levels of danger, please report them to CHIRP.
Key Issues relating to this report
Culture – A dangerous level of safety is being demonstrated by the company by allowing the use of banned drugs to be used in everyday work operations involving passengers.
Local practices – Local practices have become the norm on board this large superyacht, resulting from feeble leadership from management and senior officers.
Teamwork – The reporters exhibited a shared mental model that prompted them to address the deteriorating safety situation, which is commendable. If you are facing a similar issue, please get in touch with CHIRP if you cannot express your safety concerns through the onboard leadership team or management.
M2353 - Working aloft: unsafe by design?
Initial Report
Our reporter had recently joined a vessel during construction. They had read several CHIRP reports that mentioned the need to wear a harness when working at height, so they made a point of checking if their vessel had enough ‘pad eyes’ (strong points) in the right places on their vessel so that a crewmember could work aloft in safety once the vessel was operational.
In their opinion, more pad eyes were needed but when they raised this with the shipyard, they were told that the design had been approved by the owner, the architects and the Classification Society, so they saw no need to make a change.
CHIRP Comment
Once a design is approved, getting shipyards to implement changes becomes nearly impossible due to the high costs and complexity of the reapproval process, which inevitably delays delivery schedules. Additionally, since shipyards often construct multiple vessels based on the same design, the absence of a formal feedback loop from operational vessels back to the architects and Classification Society results in future hulls having the same deficiencies, too. It is therefore imperative that architects seek and incorporate the experiences of operators alongside the wishes of the owner during the design process.
CHIRP urges all authorities involved in superyacht design to consider the safety implications for crew and passengers from the outset and to introduce a formal feedback process so that experiential learning can be incorporated into future hull builds.
Owners, classification societies, and flag states should actively participate in this process during the design phase. Similarly, crews must provide feedback to the flag states regarding design issues. In this context, our reporters have offered an excellent example of active involvement in operational safety for the crews working on superyachts, and CHIRP wants to thank them.
Key Issues relating to this report
Culture – A calculative rather than proactive safety culture prevails. The owners do just enough to meet essential compliance. Would your superyacht benefit from installing additional safety features, particularly when working at height?
Local Practice – Just because a superyacht design is built with limited securing points does not mean it cannot be reconfigured to incorporate additional safety features.
Communications – Do you have your say on safety design? Is there engagement with the flag state, the classification society, and the designers?
M2362 - Near Miss- fatality avoided
Initial Report
Two crew members were onboard during a routine launch of a crew tender in port while the bosun operated the crane from the bridge deck. Following standard procedures, he lowered the tender with the crane fully extended and lifted the hook clear to stow it.
However, the bosun became distracted and inadvertently increased the hoisting speed. The hook struck its stop-stowed position with excessive force, breaking free from its clamped arrangement. The 10kg hook then fell 12 metres, narrowly missing a deckhand by just 20cm before striking the inside of the sponson. The impact sent the hook flying to the side of the boat, causing significant damage to the fairing.
Fortunately, no injuries occurred. The captain’s investigation revealed that the crane’s safety sensor— designed to stop the hook from contacting the job head— was missing. While the crane’s wire remained intact, the lack of this critical safety feature contributed to the incident.
The deck crew received a full debrief to address the near miss, review proper crane operation protocols, and emphasise the importance of functional safety systems. Immediate corrective actions include verifying all safety sensors before operations and reinforcing strict adherence to controlled hoisting speeds.
CHIRP Comment
The late Professor James Reason devoted his life’s work to understanding how such failures occur. His Swiss Cheese Model is a potent reminder that accidents are seldom caused by a single error but rather by multiple weaknesses in a system aligning to create the perfect storm. His contributions to safety and human factors will continue to guide industries in preventing incidents like this, ensuring that every barrier is reinforced before disaster strikes.
Key Issues relating to this report
Communication – A replacement was urgently required when the sensor failed or was missing. To prevent its further use, an out-of-service label was also needed. How well do you deal with a critical safety equipment failure?
Distraction – A significant issue in many incident reports. Given the crane’s missing sensor, heightened awareness was demanded while the crane’s hook was stowed. The bosun’s distraction allowed the hook to be stowed in a non-controlled manner, resulting in a situation where a crew member was nearly killed and damage was sustained.
Situational awareness – Everybody involved in the lifting operation should be focused on what is happening. This was a routine tender lifting operation, but the same applies to all lifting operations. Maintaining heightened situational awareness, where you constantly evaluate your status, is demanding and requires teamwork.
Teamwork – Effective teamwork serves as a strong barrier and can prevent the alignment of errors when everyone collaborates.
M2361 - Anchor operations compromised by unfamiliarity and tiredness create a hazardous situation
Initial Report
In the month leading up to the incident, the deck crew, including the reporter, had been extremely busy, often exceeding the required hours of rest. Fatigue was a persistent issue. The reporter, a relatively new
deckhand on the vessel, had only dropped anchor once or twice.
On this occasion, the crew hurried to anchor. Due to inexperience with the vessel’s anchor markings, the reporter misjudged the length of the deployed chain, thinking that four shackles had been dropped when, in fact, there were five. The final warning markings were very short and close to the chain’s end, making them unclear. As a result, the bitter end unexpectedly emerged from the chain locker. At that moment, the reporter was positioned near the brake wheel, and their hand was nearly crushed as the chain ran out. It was later discovered that the bitter-end shackle lacked a safety pin for securing it—this was on a new vessel.
CHIRP Comment
This incident raises several safety concerns—not just regarding the equipment itself but also in howe we manage fatigue, training, and supervision during critical operations like anchoring. The crew member’s
unfamiliarity with the vessel’s anchor markings significantly contributed to the misjudgement, serving as a reminder of the importance of proper familiarisation training—especially when handling essential equipment.
Securing the bitter end of the anchor should be a part of the mindset for any anchor operation — it’s the last line of defence to prevent it from running free if something goes wrong. Therefore, discovering that a brand-new vessel was delivered without a safety pin raises serious questions about quality control and oversight during the building and commissioning process.
Supervision is crucial, especially during high-risk tasks like anchoring, where even a moment’s inattention or confusion can result in significant consequences. CHIRP strongly encourages vessel operators to prioritise thorough familiarisation for all crew, ensure clear and consistent marking systems, and maintain robust oversight of critical procedures.
It’s not about assigning blame; it’s about learning and improving. These issues are preventable, and with the
proper focus, they can be resolved.
Key Issues relating to this report
Fatigue – Long hours and pressurised work can lead to a loss of clear thinking, as cognitive ability is lessened and risk-taking increases.
Situational awareness – Standing near anchor equipment during an anchor operation is hazardous, and the risk of injury can be severe. This was a close call for the operator and should alert management to current working practices.
Alerting – Given the inexperience and fatigued operator, having another crew member available for the anchoring would provide a cross-check.
M2358 - Identification of Enclosed spaces on a Super Yacht
Initial Report
Our reporter worked on a commercial yacht under 500gt that claimed to have no enclosed spaces onboard. Therefore, it didn’t have gas detection equipment, and it was impossible to determine whether bilge spaces, chain lockers, steering flats, etc., were safe to enter or work in. The reporter sent this message to CHIRP because they believe this is incorrect and that gas detection instrumentation should be supplied to all superyachts.
CHIRP Comment
Given various enclosed spaces within a superyacht, the reporter is justified in questioning the absence of gas monitoring equipment. Gas testing equipment is essential for ensuring safe entry into all enclosed spaces.
Enclosed spaces exist on all vessels—superyachts are no exception. Areas such as engine rooms, fuel and water tanks, below deck storage compartments, hull voids, and electrical control rooms pose serious risks, including oxygen depletion, toxic gas accumulation, and the potential for fire or explosion.
Given these dangers, gas testing equipment is not optional—it is essential. Every vessel must be equipped to conduct gas tests as part of a structured permit-to-work system. Without this, there is a real and preventable risk of asphyxiation, poisoning, or catastrophic incidents.
While regulations mandate safety measures for enclosed spaces, these measures are not consistently implemented at the design stage, especially in the superyacht sector. Assertions that a vessel has “no enclosed spaces” are simply inaccurate and reveal a significant oversight in regulatory design safety management.
CHIRP urges vessel operators and regulators to ensure all enclosed spaces are appropriately identified, marked, and documented, with gas detection equipment readily available and crews trained in its correct use. Ignoring this issue puts lives at risk, and action must be taken to close this safety gap.
CHIRP and other maritime organisations are working to establish an internationally recognised enclosed space sign. This initiative aims to ensure that all seafarers, regardless of the vessel they serve on, can quickly identify these hazardous areas. Standardised signage will help remove ambiguity and reinforce safe working practices across the maritime industry.
Key Issues relating to this report
Communications – The company must communicate to their fleet that learning within the company will only improve if management addresses concerns from the crew or other management and adopts a bottom-up, top-down approach to safety.
Culture – The poor response by management to the use of gas measuring equipment indicates a poor safety culture within the company to crew safety.
Alerting – Alerting management of the lack of equipment to monitor an enclosed space was poorly received.