FEEDBACK
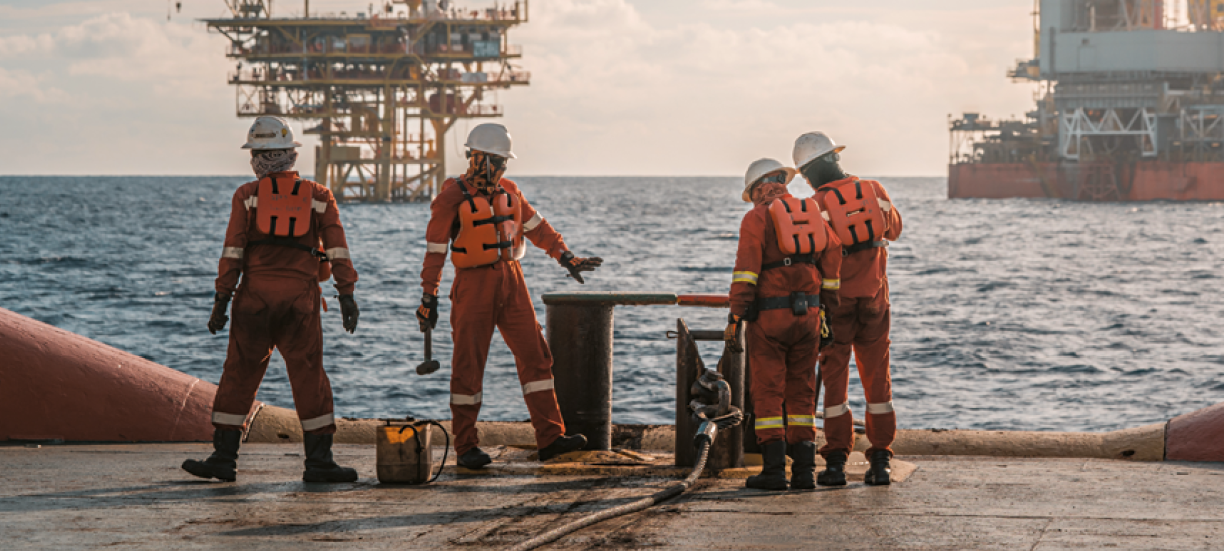
Teamwork Saves Lives
CHIRP has recently received reports from across the maritime sector, and we reflect this in the variety of incidents published in this edition. Although each incident is unique, they all agree that a proactive approach to safety, adherence to guidelines, effective communication and continuous training are essential to preventing incidents.
We start with a potentially hazardous situation that was averted by the quick response of a vigilant and alert crew. The incident also raises questions the adequacy of berth assessments, and underlines the significance of proper mooring system design and maintenance.
CHIRP was contacted by a shore-based contractor who frequently participates in lengthy sea trials. Concerned that fatigue could lead safety incidents, they sought CHIRPs intervention to resolve the situation.
Lithium-ion batteries (LIBs) fires in containers pose serious risks. We report on one incident that reinforces the need for accurate cargo declaration, proper packaging, and adherence to guidelines for the safe carriage of dangerous goods. More generally, improper stowage practices can lead to cargo damage and hazards, and we discuss why compliance with the International Maritime Dangerous Goods Code and the Code of Safe Practice for Cargo Stowage and Securing is necessary to prevent accidents and protect crew, vessels, and the environment.
Sub-aqua diving safety comes under scrutiny following an incident in which a diver was seriously injured by a propeller. We explain why the use of Surface Marker Buoys (SMBs) and shot lines are recommended to improve visibility and coordination during diving operations.
A vessel’s response to an engine failure highlights the need for timely assessment and familiarity with emergency controls. Effective collaboration between bridge and engine teams and the importance of experienced decision-making during emergencies is underscored. Finally, a lucky rescue of a single-handed fisher who had fallen overboard reveals several good safety lessons, including the importance of wearing flotation devices and personal locator beacons (PLBs), carrying means of communication, and implementing self-rescue measures such as ladders.
Remember – your feedback on our FEEDBACK is vital! And keep those reports coming! Sharing your experiences with us directly helps improve maritime safety for others who learn from your incidents.
Sail Safe,
Your CHIRP Maritime Team
-
M2150
–
Imminent mooring failure averted by vigilant crewImminent mooring failure averted by vigilant crewInitial Report
Whilst the vessel was alongside at our terminal, long-period low amplitude swell waves (groundswell) caused a large bulk carrier to yaw and roll. This motion caused the edge of the roller fairlead to saw through one of the forward spring lines. Fortunately, this was detected by the crew before it was cut all the way through, and they were able to replace the line before it parted.
CHIRP Comment
The crew’s response to the potentially dangerous situation was highly commendable; their alertness and quick action ultimately prevented the parting of mooring lines and potential further complications.
CHIRP wonders whether the chartererâs agent properly assessed the berth for suitability in the prevailing weather conditions? Unsafe berth claims go against the charterer, not the owner, so they should have a local agent on site to satisfy themselves that the berth was suitable and to raise concerns with the terminalâs operator.
The design of the mounting block on which the pairs of roller fairleads are mounted requires review. The 90-degree edges act as a blade on surging ropes. Naval architects are reminded that the edges of these should be considered during the design phase of a new vessel. By eliminating such hazards at this stage can significantly decrease the chances of lines abrading or parting during the vesselâs lifetime. OCIMFâs Mooring Equipment Guidelines (MEG4)[1]Â provide further guidance on the design and construction of the mooring system.
Properly installed moorings are not only essential for the safety of the crew but also for maintaining the ship’s structural integrity. The risks associated with inadequately installed mooringsâincluding the potential for fatalities, injuries, damage, and increased costsâcan be effectively minimised by giving importance to mooring design and construction quality.
Vessel owners remain responsible for maintenance in most cases, and they should ensure that such hidden hazards are removed as soon as possible, or at the latest, during the vesselâs next maintenance period.
[1] https://www.ocimf.org/publications/books/mooring-equipment-guidelines-meg4
Key Issues relating to this report
Communications- Are such design shortcomings fed back to naval architects to ensure that future vessels have these hazards removed?
Fit for purpose- Was the berth fit for purpose in the prevailing weather conditions? Did the chartererâs local agent confirm this was the case? Had they raised concerns with the terminal operator?
Teamwork– This report is a good example of effective monitoring by the shipâs crew.
Design- Naval architects should avoid designing sharp edges over which lines are likely to be run. Crews: does your vessel have this issue? If so â report it!
This data type is not supported! Please contact the author for help.
-
M2163
–
Fatigue issues for Contractors who work on shipsFatigue issues for Contractors who work on shipsInitial Report
A shore-based contractor who often embarks on ships for sea trials contacted CHIRP with concerns that their working routines were leading to them becoming fatigued, and they were anxious that this could result in a safety incident or accident. At sea they regularly worked 12-hour days, sometimes switching between day and night shifts mid-trial. Sea trials typically lasted for 2-3 weeks with no rest days (except when they switched from day to night shift), and fatigue has been a factor.
The reporter asked CHIRP to advise on safe working limits in such circumstances, so that they could have an informed conversation with their employer.
CHIRP Comment
The Maritime Labour Convention defines a seafarer as:
“Any person, including a master, who is employed, or engaged, or works in any capacity on board a ship and whose normal place of work is on a ship.”
Under the Convention, seafarers are entitled to a minimum of 77 hours of rest in any 7-day period and at least 10 hours of rest within any 24-hour period. The schedule of working hours must be recorded and posted for all seafarers to see.
If a personâs normal workplace is ashore, they are categorised as a ‘worker’ and their working hours are regulated by the vesselâs Flag State or local regulations. These commonly (but not always) limit the working week to an average of 48 hours, with the working day an average of 8 hours, with one day a week as a rest day.
The contractorsâ employer is responsible for the health, safety and wellbeing of their employees and should set working limits accordingly. However it is good practice for masters to ask for copies of the contractorsâ fatigue management plans so that they can satisfy themselves that their working routines have properly taken fatigue into account. Ultimately, masters are responsible for the safety of all persons on board and have the authority to grant additional rest periods to ensure that the hazard of fatigue has been controlled to a level that is âas low as reasonably practicableâ.
Other practical steps include the buddy-buddy system where pairs of workers monitor each other for signs of fatigue and bring this to their partnerâs attention. Scheduled rest days at regular intervals and shorter shifts can also help mitigate fatigue-related risks.
CHIRP is pleased to report that in this case, the employer listened to the reporterâs concerns and took action to address their fatigue concerns.
Key Issues relating to this report
Alerting- Alerting the company to high workloads is an essential first step in solving fatigue issues for shore contractors. Does your company empower you to report fatigue concerns, and are you aware of their reporting procedure?
Culture– Employers of shore contractors should have wellbeing policies and fatigue management plans. Masters are strongly encouraged to ask for sight of these when embarking contractors.
Local practices- The buddy-buddy system is a useful tool to spot the early signs of fatigue. This is most beneficial when crew and workers are empowered to report such concerns, and there are well-understood procedures in place to do so.
This data type is not supported! Please contact the author for help.
-
M2155
–
Fire in ContainerFire in ContainerInitial Report
During a voyage, a 20ft container loaded with cargo installed with lithium-ion batteries caught fire. The cargo had been mis-declared as non-DG (dangerous goods). Despite the difficulty and safety risk when gaining access to an above-deck container in a confined space, the crew punctured the container and flooded the burning cargo with water. This action controlled the fire until the vessel got to the next port, where the container was discharged for an investigation by the terminal authorities.
CHIRP Comment
The crewâs actions in containing the fire until the vessel reached port are commended, as is the decision by the port to accept the vessel â many ports turn away vessels if there is a fire of any description on board. However, these fires require specialist equipment and techniques to extinguish, which are only available in port. Both ports and vessel managers need to develop and exercise robust emergency procedures for LIB fires: traditional equipment and training is insufficient.
It is critical that shippers declare LIB and other dangerous goods correctly. Failure to do so potentially puts the lives of crews in danger because they will not have taken this factor into consideration when loading the cargo, nor be prepared to tackle a LIB fire. Regrettably, cargo misdeclaration occurs frequently.
The Cargo Incident Notification System and Network (CINS) has released a comprehensive guidance document (CSAR-101A) which is an invaluable reference document for stakeholders transporting LIBs, and provides guidelines for their safe carriage in containers.
Shippers must strictly comply with all relevant national and international safety, health, and environmental regulations when transporting goods containing LIBs. They must thoroughly evaluate the anticipated transport conditions, including factors like manufacturers and customers involved, and conduct a comprehensive assessment of the risks inherent in the supply chain.
The selection of appropriate containers, and following proper packing procedures, is especially important when shipping LIBs. Use temperature-controlled cargo units or protective stowage locations if the expected temperatures within a container are likely to exceed 40 degrees Celsius during the voyage.
By following the CINS guidelines, stakeholders can significantly reduce the risk of incidents such as thermal runaway, which can be challenging to contain and extinguish. It is essential to mention that a thermal runaway event creates very high temperatures, toxic gases and can be inextinguishable.
Traditional fire-fighting techniques are inadequate for these fires, and there is an urgent need for both training and equipment to evolve to meet the hazards of an LIB fire. In particular, CHIRP is concerned that many ports have not established procedures for tackling such fires on board vessels, nor have yet designated a safe anchorage or berth for such an eventuality.
Key Issues relating to this report
Capability- Cargo misdeclaration happens too frequently. Owners, charterers and shippers should ensure their organizations have good document management skills and processes in place. Similarly, vessels and ports should have a plan and the equipment to tackle a LIB fire. How often are the practiced?
Situational Awareness– Understanding everyoneâs role in the supply chain is the most effective way to transport DGâs safely.
This data type is not supported! Please contact the author for help.
-
M2156/58
–
Incorrect stowage incidentsIncorrect stowage incidentsInitial Report
CHIRP received two cargo stowage-related reports with similarities in causation.
- Leakage of jerricans was caused by improper packing. No dunnage plate had been fitted between layers of jerricans, resulting in the excess weight crushing the lower jerrican tiers. The jerricans were filled with the corrosive substance UN 2789 acetic acid. The leakage caused severe damage to the container interior.
- Four containers loaded onto the vessel were found emitting smoke during the voyage. The cargo was declared as DG, UN1361 Charcoal. The vanning inspection report indicates the charcoal was packed according to IMDG Code. Still, an inspection reveals a significant air space above the charcoal bags allowing more air in the container to react with the charcoal, which self-heated as a consequence.
CHIRP Comment
In the jerry-can example weight distribution was not properly considered during the vanning operation, which led to issues during the voyage. Using good quality plywood sheeting to distribute the weight of the jerry cans is a recommended practice. This helps to evenly distribute the load of each tier, reducing the chances of movement and potential damage. Additionally, using dunnage within the container prevents cargo shifting within the container. It is also good practice to provide a photo of containers once they have been loaded. This is very valuable for crews in the event of an emergency because it significantly enhances their situational awareness without having to open the container.
The second incident also highlights the importance of packing cargoes, and particularly Dangerous Goods cargoes, correctly. The International Maritime Dangerous Goods Code (IMDG Code) and the Code of Safe Practice for Cargo Stowage and Securing (CSS Code) provide useful guidance on the proper handling, packaging, stowage, and securing procedures to minimise the risk of accidents and protect the crew, the vessel, and the environment.
Bagged charcoal should be left to cool for at least 14 days before packaging, protected from moisture, and placed in sift-free and robust bags without tears. The bags should withstand the weight of other bags stacked on them. Temperature control is also crucial, with the cargo not exceeding 5 degrees above the ambient temperature during the loading process.
All parties involved in the transportation process, including the carrier, charterers, and freight forwarders, should recognise and demand that good stowage practices are followed. Better training and enforcement of the regulations can help prevent accidents, protect personnel, and safeguard the environment.
Key Issues relating to this report
Local Practices– Charterers should ask demanding questions of shippers and freight forwarders. Is the stowage in accordance with industry and seamanship standards? A photograph is a very powerful medium to confirm that this is the case.
Communications- Do the vessel managers have enough information to determine the risks for the DGâs being carried?
Capability- Ensure the management teams have enough resources to manage the carriage of DG cargoes: inadequate resources can lead to dangerous shortcuts. Is your companyâs DG team adequately resourced and skilled to meet the demands placed on them?
Teamwork- Effective supply chain teamwork was not apparent in either of these incidents.
This data type is not supported! Please contact the author for help.
-
M2152
–
Personal injury while divingPersonal injury while divingInitial Report
During a recreational wreck dive off a chartered dive vessel, a diver was hit by the turning blades of the dive boat’s propeller, sustaining significant injuries. The diver was transferred to the local hospital and had their wounds stitched. Coastguard assistance was not requested.
The wreck is best dived while there is still a weak tide over the site, ie close to slack water. The divers had therefore to be dropped up-tide of the wreck to counter the effect of tide while they descended from the surface to the wreck. Once the skipper was satisfied that they were in the right position, the engine was put into neutral to stop the propellor spinning, and the divers entered the water as a group. They swiftly conducted last minute checks before making themselves negatively buoyant and leaving surface.
On the dive boat, the engine is only put back into gear once is it visually confirmed that all divers have left surface. CCTV coverage of blind spots under the hull provide additional assurance. However in this instance, when forward propulsion was engaged, it collided with the diver who sustained serious injuries.
CHIRP Comment
The effect of tide on the boat meant that it drifted back over the location where the divers had entered the water. Although it was visually confirmed that they had all left surface, the crew on board had no way of knowing that at least one diver remained at a shallow depth, with whom they then collided when the engine was put back into gear.
The use of Surface Marker Buoys (SMB), or the laying of a shot line for the divers to hold while they descend would have provided the dive boat a visual clue to the diversâ locations.
This injury was potentially fatal, and CHIRP has contacted the reporter for additional information to determine what happened. With the reporterâs permission, CHIRP has also contacted the relevant Flag and the appropriate Accident Investigation Authority because of the seriousness of the incident.
Key Issues relating to this report
Situational Awareness- It is very difficult to determine the depth of a diver once they have left surface. This was not adequately taken into account by the dive boatâs helm.
Distractions- The boat manoeuvred before it was clear of the diver. Many stimuli, commercial pressure, fatigue, wrong signal cues from the crew, and overconfidence can cause this.
Alerting- given the severity of the incident, medical attention is required immediately. This did not happen, according to the reporter. What are your medical emergency plans in similar circumstances in your company?
This data type is not supported! Please contact the author for help.
-
M2154
–
Dredging a shipâs anchor to reach a temporary anchorageDredging a shipâs anchor to reach a temporary anchorageInitial Report
During a daylight approach to a buoyed channel, the main engine of a loaded tanker was stopped to allow more time for congestion at the berth to clear. On passing the harbour’s outer entrance, the main engine was requested to Dead Slow Ahead but failed to start. Several minutes elapsed without explicit information from the engine room as to the nature of the problem, which eventually appeared to be a control issue with fuses.
The engineers, on request by the master and pilot, could not establish local control of the main engine immediately, so it was decided to dredge the starboard anchor to a temporary anchorage close to the safe water area. A tug was requested at the location to assist in relocating the vessel to a designated anchorage area. The engineers eventually provided local control of the main engine. Approx. 2 hours later, the tug arrived on location and was made fast forward before commencing weighing anchor. The vessel was towed to the designated anchorage using the local control of the main engine as required. The vessel remained anchored for three days while repairs involved the Class surveyor’s attendance.
The reporter’s concern was the excessive time to assess the mechanical problem necessitating the immediate need to anchor and the need for more familiarity with the emergency side controls.
CHIRP Comment
The report highlights that accurate assessment skills and familiarity with maritime emergency equipment are crucial in ensuring the safety and effectiveness of maritime operations. The importance of experience in identifying the causes of engineering problems is highlighted, emphasising the need for the engine team to engage in collective thinking to enable effective collaboration with the bridge team for anticipating and planning necessary actions.
However, infrastructure support and assistance availability can vary depending on the vessel’s location, adding extra complexity to emergencies.
In terms of training engineers to collectively address engineering problems, the Short Term Strategy (STS) approach is recommended, especially when no predefined rules or procedures are available. Conducting meetings in the Engine control room to discuss the problem, assess risks, and evaluate available time can significantly enhance teamwork, establish a shared mental model, and improve communication between the engine and bridge teams. This collaborative approach helps ensure a coordinated response to challenges.
The report also suggests that engineers should be well-versed in operating side controls specific to their ship and practice using them regularly to maintain familiarity with the systems. Requiring every engineer to operate the side control at least once during their tour of duty (typically every three months) can help keep their skills sharp and ensure they can effectively manage critical equipment.
The report also acknowledges the professionalism displayed by the master and pilot in the specific incident mentioned. Their actions were in line with the severity of the engine problem, reflecting their expertise and ability to handle challenging situations appropriately.
Key Issues relating to this report
Alerting- Keeping the bridge informed of the problem in the engine room is vital. Information exchange should be concise and clearly transmitted. If you are still trying to figure out the problem, say so. The bridge team can act on this information and make contingency plans. The bridge team should understand that problem-solving can be challenging and consider it during contingency planning.
Teamwork- Create a shared mental model of the problem and encourage challenge. This is a skill set that all operational leaders should be trained to apply during emergency response operations.
Capability- Ask the question on your next ship- do we all know how to operate the engine emergency side controls? When was the last time you practised using them? DPA/Ship managers should request to see the ESC in operation when circumstances allow.
This data type is not supported! Please contact the author for help.
-
M2161
–
Lone fisher falls overboardLone fisher falls overboardInitial Report
During the early evening, a single-handed inshore fishing vessel under 10m was working pots just outside the harbourâs mouth. The fisher lost their balance and fell overboard, and could not self-rescue. Although they wore their flotation device, they could not summon help because their radio was still on the boat. They were in the water for over an hour before they were spotted and recovered by a passing sailing vessel.
Although they were extremely hypothermic, they made a full recovery. Their fishing vessel was recovered the following day.
CHIRP Comment
In this scenario, the fisher was fortunate to be spotted by a passing sailing vessel. Wearing a flotation device was crucial because it reduced the effort required to remain afloat so that they could conserve energy.
When fishing single-handed, CHIRP advises that a ladder is rigged to aid self-rescue or a floating messenger line attached to a lifebuoy streamed from the stern and next to the ladder. Fishers are also strongly encouraged to wear a waterproof hand-held VHF radio or (even better) a Personal Locator Beacon (PLB), which can alert the emergency services if you fall in.
Key Issues relating to this report
Local practices â Rig a ladder or another means of getting back on board if you fall over the side.
Communication â Carrying a means of summoning emergency assistance on your person can save your life. In some regions, fishers operate a regular radio check-in call with someone ashore to alert the authorities if they fail to check in when due.
This data type is not supported! Please contact the author for help.